Home>Devices & Equipment>Music Box>How Would A Comb On A Music Box Be Made
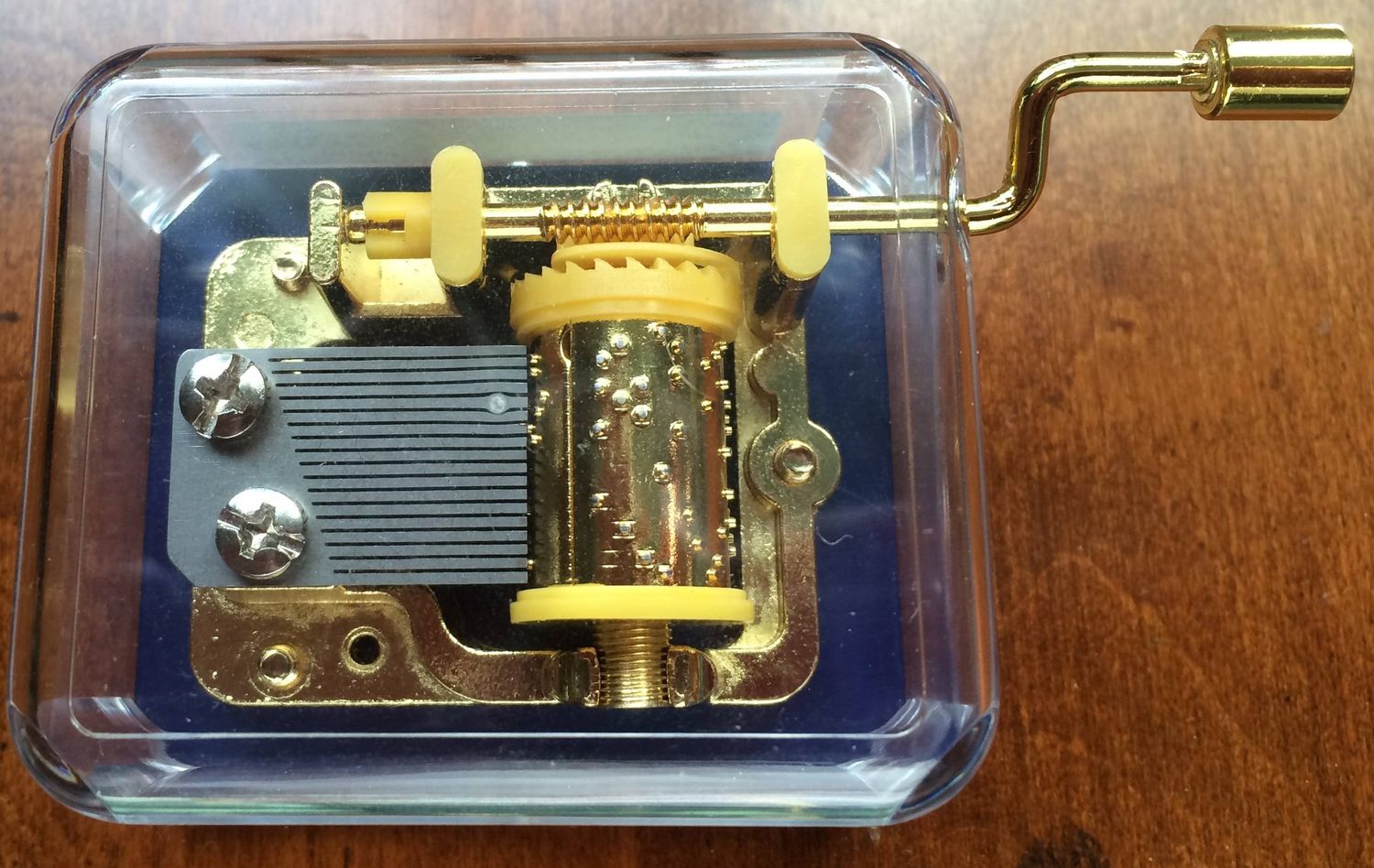
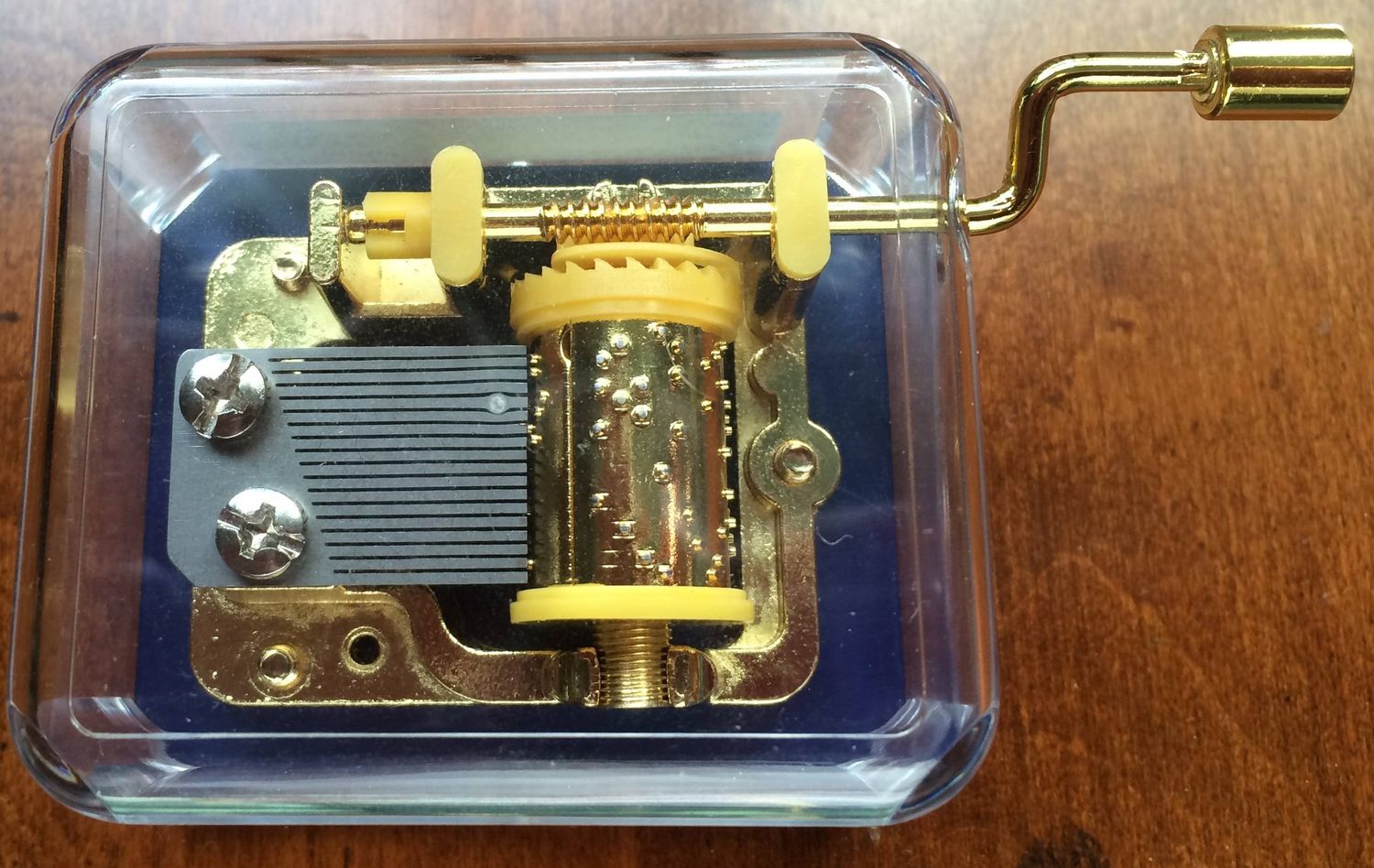
Music Box
How Would A Comb On A Music Box Be Made
Published: January 11, 2024
Discover the process of crafting a comb on a music box, from selecting materials to intricate design, and bring the melodies of a music box to life.
(Many of the links in this article redirect to a specific reviewed product. Your purchase of these products through affiliate links helps to generate commission for AudioLover.com, at no extra cost. Learn more)
Table of Contents
Introduction
Music boxes have captivated people for generations with their enchanting melodies and intricate mechanisms. A music box is a beautifully crafted instrument that produces melodious tunes when a set of tuned metal teeth or tines, known as a comb, is plucked by a revolving cylinder or disk. The comb is the heart and soul of a music box, responsible for creating the magical sounds that bring joy and nostalgia to our ears.
In this article, we will explore the fascinating world of music box combs, delving into the craftsmanship, materials, and techniques involved in creating these delicate yet powerful components. Whether you’re a music box enthusiast, a collector, or simply curious about the intricate workings of these timeless treasures, join us as we unlock the secrets behind the creation of a comb for a music box.
Throughout history, music boxes have evolved from basic, hand-cranked wooden devices to more elaborate and sophisticated designs. Their popularity peaked in the 19th century, becoming coveted items among the aristocracy and middle class alike. Today, music boxes continue to delight people of all ages, preserving a sense of nostalgia and wonder in a world consumed by digital technology.
So, sit back, relax, and allow us to take you on a journey through the history, craftsmanship, and exquisite detail that goes into making the comb for a music box. Discover the artistry and engineering brilliance behind these miniature marvels as we unveil the secrets of their creation.
History of Music Boxes
The history of music boxes can be traced back to ancient civilizations, where mechanical devices were used to produce sounds. However, it wasn’t until the 18th century that the concept of a music box as we know it today began to take shape.
The first music boxes were simple devices, often hand-crafted by skilled artisans. They consisted of a rotating cylinder, which was pierced with pins, and a set of tuned metal teeth or tines. As the cylinder rotated and the pins struck the teeth, enchanting melodies were created.
Originally, music boxes were considered luxury items and were owned mainly by the wealthy elite. However, with advancements in technology and mass production, music boxes became more accessible to the middle class. During the 19th century, music boxes reached the height of their popularity, with countless designs and variations being produced.
The music box industry experienced a decline toward the end of the 19th century due to the rise of the phonograph and later, the gramophone. These new inventions offered the ability to play recorded music, making music boxes seem outdated in comparison.
However, music boxes maintained a niche following, and their craftsmanship continued to evolve. In the 20th century, music boxes began incorporating new features such as interchangeable cylinders and automated movements. Today, they are appreciated as collectible items and cherished heirlooms.
Despite the changes in technology, the charm and allure of music boxes are still celebrated today. Whether it’s a vintage music box passed down through generations or a newly crafted piece, these enchanting devices continue to bring joy and a sense of wonder to those lucky enough to possess them.
In the next section, we will delve into the intricacies of the comb, the vital component that produces the melodious sounds of a music box.
The Mechanism of a Music Box Comb
The music box comb is the heart of the music box, responsible for producing the enchanting melodies that captivate our ears. It is a delicate yet complex mechanism consisting of a set of tuned metal teeth or tines arranged in a comb-like fashion.
The comb is typically made from high-quality steel or other metals that have been precisely shaped, sized, and tuned to produce specific musical notes. The teeth are carefully spaced and graduated in length, with longer teeth producing lower notes and shorter teeth producing higher notes.
When the music box is activated, either by winding a key or turning a crank, a set of gears and levers engages the comb. As the rotating cylinder or disk with strategically placed pins comes into contact with the teeth of the comb, it causes the teeth to vibrate and produce sounds. These vibrations create the distinctive tones and melodies associated with music boxes.
The number of teeth on a music box comb can vary, depending on the complexity and range of the melodies it is designed to play. Some combs may have as few as ten teeth, while more elaborate ones can have over a hundred.
In addition to producing different notes, the comb also determines the timbre or tonal quality of the music. The shape, thickness, and material of the teeth all contribute to the unique sound that each music box produces. Craftsmen carefully design and craft the comb to achieve the desired tone and resonance.
The mechanism of the music box comb is a testament to the precision and artistry involved in creating these magical instruments. From the meticulous shaping and tuning of each tooth to the careful arrangement and spacing, every detail is crucial in ensuring the harmonious and melodic experience that music boxes provide.
In the next section, we will explore the materials used in making music box combs and the considerations involved in their selection.
Materials Used in Making Music Box Combs
The crafting of a music box comb requires careful consideration of the materials used to achieve the desired sound and durability. Here are the primary materials commonly used in making music box combs:
- Steel: Steel is the most common material used for music box combs. It offers excellent durability, resilience, and the ability to produce clear and vibrant tones. High-quality steel is carefully selected for its specific acoustic properties, such as its ability to resonate and sustain vibrations.
- Phosphor Bronze: Another popular material for music box combs is phosphor bronze. It is an alloy of copper and tin, with small amounts of phosphorus added. Phosphor bronze combs are known for their warm and rich tonal qualities.
- Brass: Brass is occasionally used in the construction of music box combs. It is an alloy of copper and zinc, offering a bright and distinct sound. Brass combs may be preferred for certain music box designs or to achieve specific tonal characteristics.
- Wood: While less common, wood has been used in select music boxes for the comb. Typically, hardwoods with desirable acoustic properties, such as rosewood or ebony, are used. Wooden combs can offer a unique and warm sound, adding a touch of organic beauty to the music box.
The choice of material depends on various factors, including the desired tone, durability, and even aesthetic considerations. Craftsmen carefully select the material that best matches the musical vision and overall design of the music box they are creating.
When crafting the comb, the material is shaped and formed into individual teeth, meticulously tuned to their respective notes. The teeth are then precisely arranged on a bed or base, allowing for smooth and accurate plucking when engaged by the pins on the rotating cylinder or disk.
Each material has its own unique properties, contributing to the overall sound and longevity of the music box comb. The selection and craftsmanship involved in the choice of materials are crucial to achieving the desired musical quality and ensuring the comb’s durability over time.
Now that we’ve explored the materials used in making music box combs, let’s dive into the intricate process of designing and crafting a comb for a music box.
Designing a Comb for a Music Box
The design of a music box comb is a meticulous process that involves careful consideration of various factors, including the desired musical range, tonal quality, and overall aesthetic of the instrument. Here are the key steps involved in designing a comb for a music box:
1. Determining the Musical Range: The first step in the design process is to determine the musical range or the number of notes the music box will be able to produce. This will influence the number of teeth required on the comb and the overall size of the instrument.
2. Selecting the Tooth Shape: The shape of the teeth on the comb plays a significant role in the production of sound. Teeth can be designed in various shapes, such as rectangular, triangular, or even custom shapes, each affecting the quality and character of the produced tones.
3. Calculating the Tooth Length and Spacing: Teeth on the comb are graduated in length, with longer teeth producing lower notes and shorter teeth producing higher notes. The length and spacing of the teeth are carefully calculated to ensure accurate tuning and harmonious melodies.
4. Balancing the Tonal Quality: Craftsmen aim to strike a balance between the brightness and warmth of the tonal quality offered by the comb. The thickness of the teeth and the material used can affect the overall sound, allowing for variations and customization based on the desired musical experience.
5. Considering Aesthetics: While the primary focus is on the sound and functionality of the comb, the design also considers the aesthetic appeal of the instrument. The shape and arrangement of the teeth, as well as any decorative elements, contribute to the overall visual beauty of the music box.
Throughout the design process, skilled craftsmen leverage their expertise, experience, and a keen understanding of acoustics to create a comb that will deliver an exceptional musical experience. Each detail is carefully planned and calculated to ensure the optimal balance of sound and aesthetics.
Once the design is finalized, the craftsmen move on to the intricate process of crafting the comb, as we will explore in the next section.
Crafting Process of a Music Box Comb
The crafting process of a music box comb is a fine balance of artistry, precision, and expertise. Skilled craftsmen utilize a combination of traditional techniques and modern tools to transform raw materials into a meticulously crafted comb. Here is an overview of the crafting process:
1. Material Preparation: The first step involves selecting the appropriate material, such as high-quality steel or phosphor bronze. The chosen material is then shaped into a flat sheet or strip, ready for the comb-making process.
2. Shaping and Cutting the Teeth: Using specialized tools, the craftsman cuts and shapes the material to create individual comb teeth. The teeth are carefully measured, ensuring precise length and spacing, as specified in the comb design.
3. Tuning the Teeth: Each tooth is meticulously tuned to produce the correct musical note. This is accomplished by carefully sanding or filing the teeth to adjust their length and thickness. The craftsman tests the sound produced by each tooth and makes further adjustments as needed until the desired tonal quality is achieved.
4. Arranging the Teeth: Once the teeth are tuned, they are arranged on a solid base or bed. The craftsman carefully places each tooth in its designated position, ensuring proper spacing and alignment to ensure accurate plucking and optimal sound production.
5. Securing the Teeth: To ensure stability, the teeth are securely affixed to the base. This is often done by soldering or using adhesive compounds specifically designed for this purpose.
6. Finishing and Polishing: The comb is meticulously inspected, and any rough edges or imperfections are carefully smoothed out. The craftsman then applies a protective finish to the comb, which not only enhances its appearance but also helps protect it from corrosion.
7. Quality Control: The finished comb undergoes a thorough quality control process, where it is carefully inspected and tested to ensure it meets the highest standards of craftsmanship. The comb is examined for proper tooth alignment, accurate tuning, and overall sound quality.
Throughout the crafting process, the music box comb is handled with great care and attention to detail. Each step is aimed at creating a comb that will produce harmonious sounds and withstand the test of time.
Once the comb passes the quality control checks, it is ready to be fitted into the music box mechanism, where its magical sounds will come to life. In the next section, we will explore the final steps of tuning and testing the comb to ensure it delivers the desired musical experience.
Tuning and Testing the Comb
After the crafting process, the music box comb enters the crucial stage of tuning and testing. Skilled craftsmen meticulously fine-tune the comb to ensure it produces accurate notes and harmonious melodies. Here is a closer look at the process of tuning and testing the comb:
1. Tuning the Individual Teeth: Each tooth of the comb is carefully adjusted to produce the correct pitch. The craftsman uses specialized tools, such as a file or sandpaper, to carefully remove or add material to the teeth. These precise adjustments allow for subtle tonal changes, ensuring that each tooth produces the desired note.
2. Checking the Harmonic Accuracy: The craftsman tests the comb to ensure that the harmonies produced by the different teeth are accurate and blend well together. This involves playing various melodies and listening for any dissonance or inconsistencies that need to be addressed.
3. Adjusting the Spacing and Alignment: The spacing and alignment of the teeth on the comb play a crucial role in the clarity and accuracy of the music. The craftsman carefully examines and adjusts the spacing between the teeth, ensuring they are evenly arranged and properly aligned.
4. Filing and Smoothing: Any rough edges or imperfections on the teeth are carefully filed and smoothed out. This step ensures that the teeth can be plucked smoothly and that there are no obstructions that could disrupt the sound production.
5. Dynamic Testing: Lastly, the comb undergoes dynamic testing to assess its performance under varying conditions. The craftsman plays the music box with different degrees of winding, examining the comb’s responsiveness, tonal quality, and sustained vibrations. This step ensures that the comb performs consistently throughout the music box’s operating range.
The tuning and testing process requires an experienced ear and a keen understanding of musical nuances. Skilled craftsmen draw upon their expertise to fine-tune the comb, taking into account factors like resonance, sustain, and tonal balance. The goal is to achieve an instrument that delivers harmonious melodies that are pleasing to the ear.
Once the comb has passed all tests and meets the high standards of quality, it will be integrated into the music box mechanism, ready to create beautiful music for its fortunate owner. In the next section, we will explore the importance of maintenance and repair to ensure the longevity and continued enjoyment of the music box comb.
Maintenance and Repair of a Music Box Comb
Maintaining the condition of a music box comb is essential to ensure its longevity and the continued enjoyment of its melodic tunes. Here are some key considerations for the maintenance and repair of a music box comb:
Regular Cleaning: Dust, dirt, and debris can accumulate on the comb over time, affecting its performance and sound quality. Regularly clean the comb using a soft brush or a gentle stream of compressed air to remove any particles that may have settled between the teeth.
Avoid Moisture and Humidity: Moisture can cause damage to the comb, leading to rust or corrosion. Keep the music box in a dry environment, away from areas with high humidity. If necessary, place a desiccant or silica gel packet near the music box to absorb excess moisture.
Gentle Handling: When handling the music box, take care to avoid putting unnecessary pressure or force on the comb. Excessive force can bend or damage the teeth, affecting their ability to produce accurate notes.
Professional Maintenance and Repair: If the music box comb requires repair or adjustment, it is best to seek the assistance of a professional music box technician or repair specialist. They have the expertise and specialized tools necessary to address any issues with the comb, ensuring its proper functioning.
Replacement of Damaged Teeth: In some cases, a tooth on the comb may become damaged or broken. This can disrupt the harmony and performance of the music box. A skilled technician can replace the damaged tooth, ensuring that the comb continues to produce the intended sound.
Regular Lubrication: The components of the music box, including the comb, benefit from periodic lubrication. Consult the manufacturer’s instructions or seek professional advice on the appropriate lubricant to use and the recommended intervals for lubrication.
Professional Tuning: Over time, the comb may require re-tuning to maintain optimal sound quality. This task is best left to a skilled technician who understands the nuances of comb tuning and can make the necessary adjustments to ensure harmonious melodies.
By following proper maintenance practices and seeking professional assistance when needed, you can extend the lifespan of the music box comb and preserve its ability to produce beautiful music for years to come.
Now that we’ve explored the maintenance and repair of a music box comb, let’s wrap up our journey through the wonders of these enchanting musical instruments in the concluding section.
Conclusion
The comb of a music box is a remarkable piece of craftsmanship, responsible for creating the enchanting melodies that bring joy and nostalgia to our ears. Throughout history, music boxes have captured the hearts of people with their intricate mechanisms and captivating tunes. The comb, with its precision-tuned teeth and thoughtful design, is the heart and soul of these magical instruments.
From the early days of simple hand-cranked devices to the more elaborate and sophisticated designs of today, music boxes continue to captivate people of all ages. The selection of materials, the painstaking design process, and the meticulous craftsmanship involved in creating a music box comb are a testament to the artistry and devotion of the artisans.
As music box enthusiasts, collectors, or simply admirers of these timeless treasures, we have explored the journey of a music box comb – from its historical roots to the intricacies of its mechanism. We have learned about the specific materials chosen, the process of designing and crafting, and the importance of tuning and testing for optimal performance.
Moreover, we have discovered that the care and maintenance of a music box comb are crucial for its longevity and continued enjoyment. Regular cleaning, gentle handling, and seeking professional assistance when needed are essential steps to ensure that the comb remains in pristine condition and continues to produce harmonious melodies for years to come.
Music boxes hold a special place in our hearts, evoking emotions and stirring memories with their whimsical tunes. They remind us of a bygone era, where beauty and craftsmanship converged to create moments of pure joy and wonder. In a world dominated by digital technology, music boxes continue to provide a tangible connection to our past, preserving the magic of mechanical music in an age of innovation.
So, whether you own a vintage music box handed down through generations or a newly acquired piece, take a moment to appreciate the elegance and intricacy of the comb that brings it to life. Let the melodies transport you to another time, and cherish the beauty and artistry of these timeless treasures.