Home>Devices & Equipment>Turntable>What Does Everything Do On A Turntable
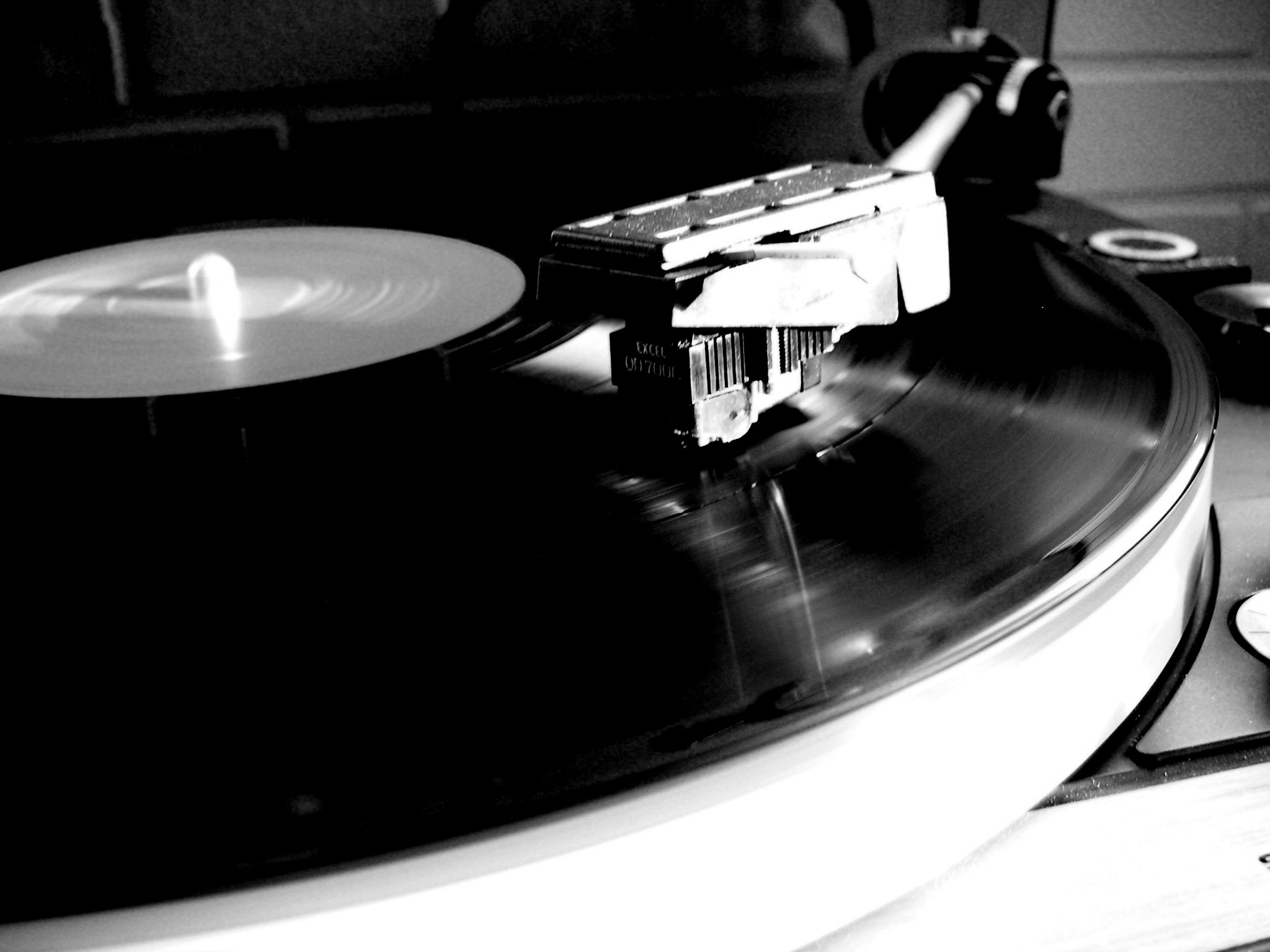
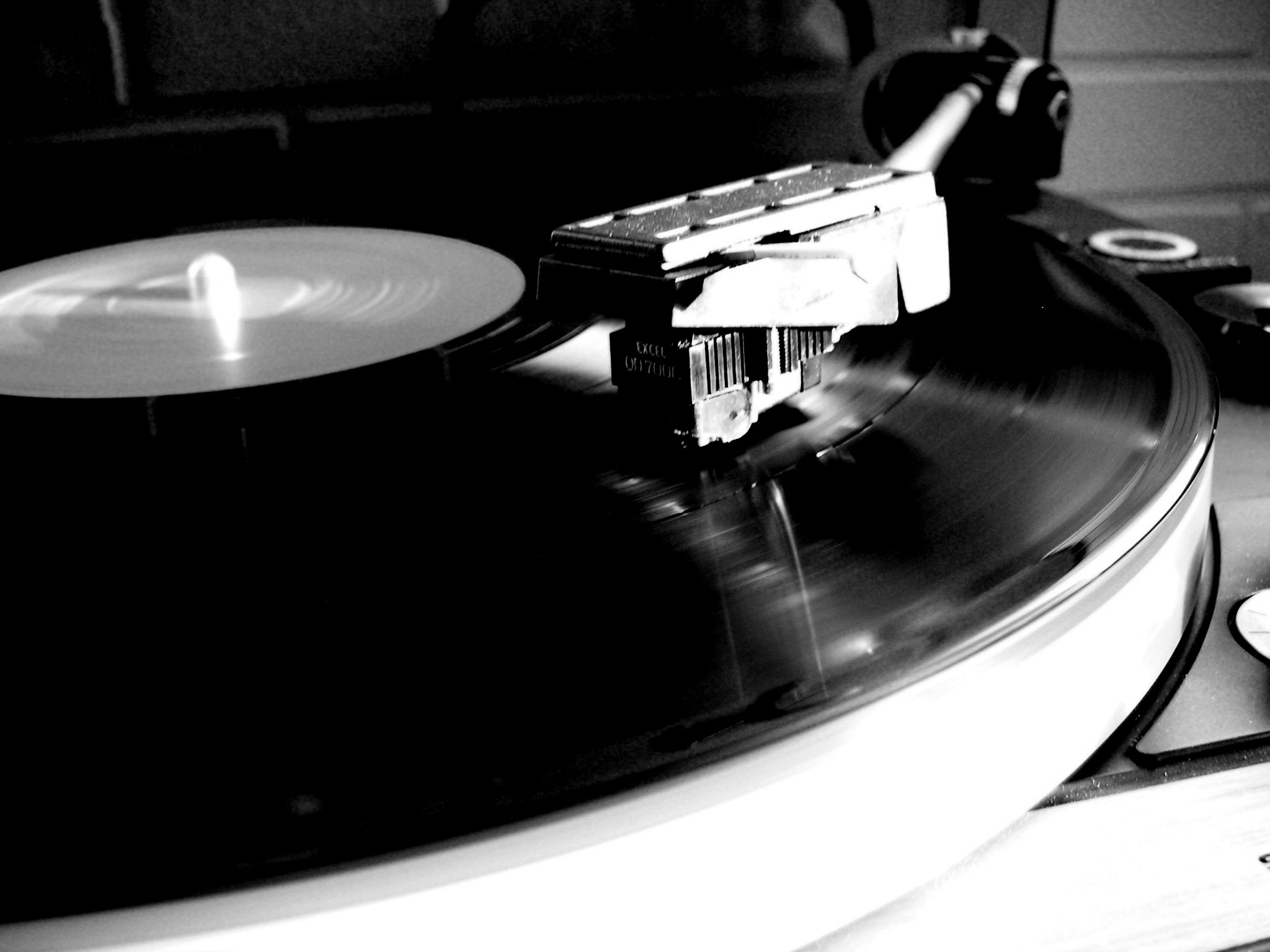
Turntable
What Does Everything Do On A Turntable
Modified: January 22, 2024
Discover what everything does on a turntable and unlock the secrets of this essential music device. Explore the components and functions of a turntable for the ultimate audio experience.
(Many of the links in this article redirect to a specific reviewed product. Your purchase of these products through affiliate links helps to generate commission for AudioLover.com, at no extra cost. Learn more)
Table of Contents
Introduction
Turntables, also known as record players, have been a staple in the world of music for decades. With their unique ability to play vinyl records, turntables offer a nostalgic and authentic listening experience that many audiophiles cherish. Whether you’re a vinyl enthusiast or simply curious about this classic audio device, understanding the various components and functions of a turntable is essential.
In this article, we will explore the different components of a turntable and their respective roles in producing high-quality sound. From the tonearm to the stylus, each element plays a crucial part in delivering a smooth and accurate playback experience.
As we delve into the intricacies of turntable anatomy, we will also touch upon the various controls and adjustments found on these devices. From speed selectors to pitch control, these features allow users to customize their listening experience and optimize the performance of their turntable.
So, whether you’re a curious beginner or a seasoned vinyl lover, let’s dive into the world of turntables and discover what each component does and how they work together to produce the mesmerizing sound of vinyl records.
Turntable Components
A turntable consists of several key components that work together to create a seamless audio experience. Let’s take a closer look at each of these components:
- Tonearm: The tonearm is a crucial part of the turntable, responsible for holding the cartridge and stylus in place while allowing them to track the record groove. It ensures that the stylus follows the record’s grooves accurately, translating the vibrations into electrical signals.
- Cartridge: The cartridge houses the stylus and is responsible for converting the mechanical vibrations from the record groove into electrical signals. There are two types of cartridges: moving magnet (MM) and moving coil (MC). Both types have their unique characteristics and affect the sound reproduction of the turntable.
- Platter: The platter is the rotating disc on which the vinyl record rests. It provides stability and ensures a smooth rotation, allowing the stylus to accurately track the grooves of the record. Platters can be made from various materials, including aluminum, acrylic, or glass, each with its own impact on sound quality.
- Motor: The motor is responsible for driving the rotation of the turntable’s platter. It maintains a consistent spin rate, ensuring accurate playback speed. There are two common types of motors used in turntables: belt-driven and direct-drive. Belt-driven turntables use a belt to connect the motor to the platter, reducing motor noise and vibration for improved sound quality. On the other hand, direct-drive turntables have the motor directly connected to the platter, offering better speed stability and torque.
- Drive System: The drive system refers to the mechanism used to transfer power from the motor to the turntable’s platter. In addition to belt-driven and direct-drive systems, there are also idler-wheel-driven systems, which use a rubber wheel to transfer power. Each drive system has its own advantages and impacts on performance.
- Speed Selector: The speed selector allows users to choose the rotational speed of the turntable. Most turntables offer the standard speeds of 33 1/3 RPM (revolutions per minute) for full-length albums and 45 RPM for singles. Some turntables may also include an option for 78 RPM, which is used for older or specialized vinyl records. The speed selector ensures accurate playback at the desired speed.
- Stylus: The stylus, also known as the needle, is a tiny, diamond-tipped component attached to the cartridge. It makes direct contact with the record groove and, as it follows the grooves, converts the mechanical movement into electrical signals. The type and quality of the stylus significantly impact the sound quality and longevity of both the stylus and the record.
These are just some of the essential components that make up a turntable. Each component plays a vital role in providing a rich, authentic, and detailed sound reproduction. As we delve deeper into the mechanics of turntables, we’ll discover additional features and adjustments that further enhance the listening experience.
Tonearm
The tonearm is a crucial component of a turntable, responsible for holding the cartridge and stylus in place while allowing them to accurately track the grooves of the vinyl record. It plays a vital role in accurately detecting the microgrooves on the record’s surface and converting them into electrical signals.
The tonearm typically consists of three key parts: the tube, the headshell, and the bearing assembly. The tube is the long, slender arm that extends from the turntable’s base, while the headshell is the component that holds the cartridge. The bearing assembly allows the tonearm to pivot smoothly, ensuring precise tracking of the record’s grooves.
One of the most critical aspects of a tonearm is its tracking ability. The tonearm must apply the perfect amount of pressure on the stylus as it moves along the grooves of the record. This tracking force allows the stylus to glide smoothly and precisely, capturing the intricate details of the music. Most turntables have a tracking force adjustment mechanism to fine-tune the pressure exerted on the stylus.
Another essential element of the tonearm is the anti-skate adjustment. This adjustment counteracts the tendency of the tonearm to move towards the center of the record under the influence of the record groove. By applying a slight outward force on the tonearm, the anti-skate mechanism ensures that the stylus maintains optimal contact with the grooves, preventing distortion and wear on the record.
The shape and design of the tonearm also affect its performance. Generally, tonearms come in either straight or S-shaped designs. Straight tonearms offer superior tracking ability and minimize distortion but can be less forgiving of imperfections in record pressing. S-shaped tonearms provide better stylus alignment and have more forgiving tracking characteristics, making them more suitable for beginners or those with older records.
Furthermore, some advanced turntables feature tonearms with adjustable vertical tracking angle (VTA) and azimuth. VTA adjustment allows users to fine-tune the angle at which the stylus contacts the record’s surface, optimizing playback performance. Azimuth adjustment, on the other hand, aligns the cartridge’s stylus with the record grooves, reducing channel separation and improving sound quality.
Overall, the tonearm is a critical component that directly influences the accuracy and quality of the sound produced by a turntable. Its ability to effectively track the record grooves and maintain proper alignment with the stylus is essential for achieving a mesmerizing and faithful audio playback experience.
Cartridge
The cartridge is a vital component of a turntable, responsible for converting the mechanical vibrations from the record groove into electrical signals that can be amplified and reproduced as sound. It houses the stylus or needle, which makes direct contact with the record surface and tracks the grooves to retrieve the audio information encoded on the vinyl.
There are two main types of cartridges commonly used in turntables: moving magnet (MM) and moving coil (MC).
The moving magnet cartridge is the most popular and widely used type. It features a tiny magnet attached to the cantilever, which moves along with the stylus in response to the groove contours. As the magnet moves, it generates electrical signals by inducing voltage changes in the coil surrounding it. The coil is connected to the turntable’s phono stage or preamp, which processes and amplifies the signals before sending them to the speakers.
On the other hand, the moving coil cartridge is an alternative design that offers several advantages. In this type, the coil is attached to the cantilever, while the magnet remains stationary. The motion of the cantilever and coil generates the electrical signals. Moving coil cartridges tend to have lower mass, which allows for better tracking of the record grooves and improved accuracy. They also tend to provide a more detailed and nuanced sound reproduction, albeit at a higher cost compared to moving magnet cartridges.
Both MM and MC cartridges come in different stylus shapes, such as spherical, elliptical, or line contact. The stylus shape determines the contact area with the record grooves, affecting the level of detail and tracking ability. Generally, finer and more intricate stylus shapes, like the line contact or microline, provide superior resolution and tracking, but they may require more careful handling and maintenance.
It’s important to note that the cartridge’s compatibility with the turntable’s tonearm is crucial for optimal performance. Cartridges have different mounting styles, such as standard 1/2 inch or P-mount, and may require specific headshells or adapters for proper installation.
When choosing a cartridge, it’s essential to consider factors like budget, sound preferences, and turntable compatibility. Additionally, regular maintenance, such as cleaning the stylus and replacing the cartridge when necessary, is crucial to ensure optimal sound quality and longevity.
The choice of cartridge significantly influences the overall sound reproduction of a turntable, making it an essential component for audiophiles and music enthusiasts seeking the best possible listening experience.
Platter
The platter is a crucial component of a turntable, serving as the rotating surface on which the vinyl record sits during playback. Its design and construction play a significant role in the overall performance and sound quality of the turntable.
One of the primary functions of the platter is to provide stability and maintain a consistent rotation speed. This is essential for accurate tracking of the record grooves by the stylus. Platters are typically made from various materials, including aluminum, acrylic, or glass.
Aluminum platters are commonly found in entry-level turntables. They offer good balance, stability, and sound reproduction performance. Acrylic platters are often seen in mid-range and high-end turntables, providing enhanced damping properties to reduce unwanted vibrations and resonance. Acrylic platters are known for their excellent sonic characteristics, delivering a more detailed and dynamic audio experience. Glass platters are less common but are lauded for their superior mass and density, further reducing vibration and yielding exceptional sound reproduction.
The surface of the platter must also be smooth to prevent any uneven contact with the record. Even slight imperfections can cause skipping or distortion during playback. Manufacturers often use a special non-slip mat made from materials like rubber or felt to ensure proper grip and reduce slippage between the platter and the record.
In addition, some turntables feature a sub-platter or an inverted bearing assembly beneath the platter. This design enhances stability and minimizes rotational friction, allowing for smoother and more consistent rotation.
Another element to consider is the platter’s mass. Higher mass platters tend to provide better speed stability as they resist variations in rotational speed caused by external factors or changes in load. However, excessively heavy platters can introduce their own challenges, requiring a more robust motor and drive system to maintain proper rotation.
Advanced turntables may also offer features like a platter with a built-in decoupling mechanism. This further isolates the platter from vibrations transmitted from the turntable’s base, minimizing unwanted resonance and improving overall sound quality.
In summary, the platter is a significant component of a turntable, contributing to its overall performance and sound quality. Its material, smoothness, mass, and design all impact the stability and accuracy of rotation, ultimately affecting how faithfully and vibrantly the music is reproduced.
Motor
The motor is a crucial component of a turntable, responsible for driving the rotation of the platter. It plays a vital role in maintaining a consistent and accurate playback speed, which is crucial for faithful reproduction of the music.
There are two main types of motors commonly used in turntables: belt-driven motors and direct-drive motors.
Belt-driven motors use a rubber or synthetic belt to transfer power from the motor to the turntable’s platter. The motor is typically located away from the platter, reducing the transmission of motor-induced vibrations to the record. This design provides several advantages, including lower noise levels, reduced vibration, and improved isolation between the motor and the turntable’s bearing. Belt-driven turntables are known for their smooth and quiet operation, making them popular among audiophiles who prioritize sound quality.
On the other hand, direct-drive motors have the motor directly integrated into the turntable’s platter. This design offers several advantages, including better speed stability and more robust torque, making it ideal for DJs and those who require precise control over playback speed. Direct-drive turntables are typically easier to maintain, as they don’t require periodic belt replacement.
While belt-driven turntables may have better isolation from motor-induced vibrations, direct-drive turntables offer superior speed stability and torque, which can be beneficial in various applications.
It’s worth noting that the motor’s quality and construction directly impact the overall performance of the turntable. High-quality motors provide accurate and consistent rotation, minimizing variations in playback speed that can distort the music. They also generate less vibration and noise, further improving sound quality.
Some advanced turntables may feature additional motor-related features, such as speed adjustment controls. These controls allow users to fine-tune the playback speed manually, ensuring precise synchronization with other audio equipment or accommodating different vinyl playback formats.
Overall, the motor is a crucial component that drives the rotation of the turntable’s platter, setting the foundation for accurate and reliable playback. Whether belt-driven or direct-drive, a high-quality motor is essential for achieving optimal sound reproduction and providing an enjoyable listening experience.
Drive System
The drive system of a turntable refers to the mechanism used to transfer power from the motor to the platter, enabling it to rotate and play the vinyl record. There are three main types of drive systems commonly found in turntables: belt drive, direct drive, and idler wheel drive.
Belt drive systems utilize a rubber or synthetic belt that connects the motor to the turntable’s platter. The motor is typically located away from the platter, with the belt acting as the intermediary to transfer power. Belt drive systems are known for their low noise levels, as the belt helps to isolate motor vibrations from reaching the platter. This design also offers smoother rotation and better resistance to speed fluctuations caused by external factors. Belt drive turntables are favored by audiophiles for their ability to deliver excellent sound quality.
Direct drive systems, on the other hand, have the motor directly integrated into the center of the platter. The motor’s rotor is directly connected to the platter, resulting in a more direct power transfer. Direct drive turntables are popular among DJs and enthusiasts who require precise control over the playback speed. These turntables offer superior torque and speed stability, making them ideal for scratching, mixing, and beat matching.
Idler wheel drive systems use a rubber wheel, known as the idler wheel, to transfer power from the motor to the turntable’s platter. The wheel is placed between the motor and the platter, and a spindle connects the two. Idler wheel drive turntables are known for their high torque and fast startup times, making them popular choices in professional audio environments. However, they can be prone to noise and require periodic maintenance to ensure optimal performance.
Each drive system has its own advantages and drawbacks, and the choice often comes down to personal preference and the intended use of the turntable. Belt drive turntables are favored for their superior sound quality and lower noise levels, making them ideal for critical listening. Direct drive turntables are well-suited for DJing and those who require precise speed control. Idler wheel drive turntables offer high torque and fast startup times, making them preferable for certain professional applications.
It’s worth mentioning that the drive system is a fundamental aspect of a turntable, and its quality and design have a direct impact on the overall performance and user experience. Whether you prioritize sound quality, DJ functionality, or specific technical requirements, selecting the right drive system is essential to ensure a satisfying and enjoyable turntable experience.
Speed Selector
The speed selector is a crucial feature found on most turntables, allowing users to choose the rotational speed at which the platter spins. Different vinyl records are designed to be played at specific speeds, and the speed selector ensures accurate playback of the recorded content.
The most common speed options found on turntables are 33 1/3 RPM (revolutions per minute) and 45 RPM. The 33 1/3 RPM speed is used for playing full-length albums or LPs, while the 45 RPM speed is typically used for singles or EPs. These two speeds cover the vast majority of vinyl records available in the market.
Some turntables may also have an additional speed option of 78 RPM, which is used for playing older or specialized records, such as shellac or early vinyl releases.
It’s important to note that selecting the correct speed is crucial for ensuring the proper playback of the recorded content. Playing a record at the wrong speed can result in inaccurate pitch, distortion, and a subpar listening experience.
The speed selector mechanism varies depending on the turntable’s design. Some turntables have a manual speed selector switch or button that allows users to choose the desired speed manually. Others have an automatic speed detection feature, where the turntable identifies the correct speed based on information encoded on the record itself.
Additionally, some advanced turntables may offer pitch control functionality, which allows users to adjust the rotational speed of the platter slightly. This can be useful for fine-tuning the playback speed or matching the tempo of songs when DJing or creating mixtapes.
Overall, the speed selector is an essential feature of a turntable, ensuring accurate playback of vinyl records at the proper rotational speed. Whether manually selecting the speed or relying on automatic detection, it’s crucial to use the correct speed to ensure optimal sound quality and a faithful reproduction of the music.
Stylus
The stylus, also known as the needle, is a small but crucial component of a turntable’s cartridge. It is responsible for making direct contact with the record’s grooves and retrieving the audio information encoded on the vinyl.
The stylus is typically made with a tiny diamond tip attached to a metal cantilever. As the record spins, the stylus rides along the grooves, picking up vibrations and converting them into electrical signals. These signals are then transmitted to the cartridge, which amplifies and processes them for playback through speakers or headphones.
One of the key factors determining the sound quality and longevity of a stylus is its shape. Three common stylus shapes are spherical, elliptical, and line contact.
A spherical stylus has a rounded tip and makes contact with a small area of the record groove. While it provides adequate sound reproduction and is more forgiving of imperfections in records, it may not capture the same level of detail as other stylus shapes.
An elliptical stylus has an elongated tip that makes contact with a larger area of the groove. This shape allows for better tracking of the intricacies within the grooves, resulting in improved sound quality and higher fidelity playback.
A line contact stylus, also known as a microline or Shibata, has a very narrow and precise contact area with the record groove. This shape provides exceptional tracking ability and can retrieve even the finest details of the recording. Line contact styluses are often preferred by audiophiles and enthusiasts striving for the highest level of fidelity.
It’s important to note that stylus wear occurs over time, and the shape and condition of the stylus can greatly impact the sound quality and preservation of the vinyl record. Regular cleaning and maintenance of the stylus are essential to remove any dust or debris that can affect playback and to ensure optimal performance.
The lifespan of a stylus varies depending on factors such as usage, record condition, and tracking force applied. As the stylus wears down, it may start to exhibit signs of degradation, such as reduced sound quality, distortion, or skipping. In such cases, replacing the stylus is necessary to maintain the best possible playback experience.
Choosing the right stylus for a turntable is an important consideration as it directly impacts the sound quality and performance. The choice of stylus shape should be based on personal preferences, record collection, and budget, with the goal of achieving the desired audio fidelity and preserving the longevity of both the stylus and the vinyl records.
Tracking Force Adjustment
The tracking force adjustment is a crucial feature on turntables that allows users to set the amount of pressure exerted by the stylus on the record’s grooves. Proper tracking force is essential for accurate playback and to prevent excessive wear or damage to both the stylus and the vinyl record.
The tracking force refers to the downward pressure applied by the tonearm through the cartridge onto the record. It is measured in grams and typically ranges from 1 to 3 grams, although specific cartridges may require a different range of tracking force.
Setting the appropriate tracking force ensures that the stylus maintains optimal contact with the record’s grooves, allowing it to accurately read the audio information encoded on the vinyl. Insufficient tracking force can result in poor tracking, causing the stylus to skip or mistrack the grooves, leading to distorted or inaccurate sound reproduction. On the other hand, excessive tracking force can damage both the stylus and the record, causing excessive wear or even groove damage.
To adjust the tracking force, turntables typically feature a counterweight on the rear end of the tonearm. This counterweight can be rotated to calibrate the downward force exerted by the tonearm. Some tonearms may also have a calibrated scale that assists in tracking force adjustment, allowing for precise and repeatable settings.
When adjusting the tracking force, it’s important to consult the manufacturer’s guidelines or the cartridge’s specifications to determine the recommended range. This ensures that the stylus performs optimally and extends both stylus and record life.
It’s worth noting that tracking force can be affected by other factors, such as tonearm balance and anti-skate settings. Therefore, it’s essential to properly set up and calibrate the turntable to achieve accurate tracking force adjustment.
Regularly checking and adjusting the tracking force is crucial, especially when changing cartridges or stylus types. It ensures that the stylus is applying the correct amount of pressure for accurate tracking, minimizing wear on the record and maximizing sound quality.
Overall, the tracking force adjustment is a vital feature on turntables, allowing users to fine-tune the stylus pressure to ensure accurate playback and prolong the lifespan of both the stylus and the vinyl records.
Anti-skate Adjustment
The anti-skate adjustment is a critical feature found on turntables that helps to counteract the inward force applied to the tonearm as it tracks towards the center of the record. This adjustment ensures that the stylus maintains optimal contact with the record’s grooves, reducing distortion and improving overall sound quality.
As a record plays, the groove contours cause a slight inward force on the stylus and the tonearm. This force, known as skating force, can compromise the accuracy of stylus tracking and lead to uneven wear on the record or misalignment between the stereo channels.
The anti-skate adjustment works by applying an outward force on the tonearm, counteracting the inward skating force. It helps to maintain the stylus perpendicular to the record groove, allowing it to track more accurately and reduce channel imbalance.
The anti-skate adjustment mechanism may differ depending on the turntable model. It is usually achieved through a tensioning mechanism, such as a weight or spring, attached to the tonearm. By adjusting the anti-skate control, users can fine-tune the applied force to balance the tonearm and optimize the tracking performance.
Setting the anti-skate adjustment correctly is crucial for achieving optimal sound quality and minimizing record wear. If the anti-skate is set too low, the stylus may not fully track the grooves, causing distortion and compromised fidelity. Conversely, if the anti-skate is set too high, excessive force may be applied to the record, leading to premature wear and potential damage.
Adjusting the anti-skate requires careful attention to the manufacturer’s guidelines or the specific cartridge’s recommendations. It is often recommended to start with the anti-skate adjustment in line with the tracking force and make slight adjustments based on listening tests and performance evaluation.
It’s worth noting that the anti-skate adjustment can interact with other turntable settings. For example, changes in tracking force may necessitate small tweaks to the anti-skate setting. Additionally, different tonearm designs may require specific anti-skate adjustments, so it’s essential to consult the turntable’s manual for specific instructions.
By properly adjusting the anti-skate, users can significantly improve the accuracy of stylus tracking, reducing distortion and ensuring an optimal listening experience. It is an important aspect of turntable setup that should not be overlooked by audiophiles and vinyl enthusiasts.
Cueing Lever
The cueing lever, also known as the tonearm lift or tonearm cue, is a convenient feature found on turntables that allows for precise control when starting and stopping the playback of vinyl records. It enables users to lift and lower the tonearm gently without risking any harm to the stylus or record.
When the cueing lever is engaged, the tonearm is lifted from its resting position and hovers above the record’s surface. This feature allows users to position the stylus accurately at the desired starting point of a track or gently lift it at the end of a song to prevent unnecessary wear on the stylus or record.
The cueing lever typically operates in a vertical motion, lifting the tonearm through a mechanical linkage connected to the tonearm assembly or base of the turntable. Some high-end turntables may have more advanced cueing mechanisms that utilize hydraulic dampening for enhanced control and smoother operation.
This feature is especially useful for DJs, audiophiles, and music enthusiasts who want to carefully manage the playback of their vinyl records. It provides a safer and more controlled way to handle the delicate stylus and protect the integrity of the record grooves.
Additionally, the cueing lever can be used as a visual guide when setting up the turntable. By adjusting the cueing lever’s height, users can achieve the correct tracking and stylus placement, ensuring optimal sound quality and minimizing wear on the record.
When using the cueing lever, it’s essential to operate it gently and avoid any sudden movements or excessive force. Mishandling the cueing lever can cause the stylus to skip or damage the grooves of the record. Care should also be taken to ensure that the stylus is properly aligned with the desired location on the record to avoid incorrect tracking or damage.
While not all turntables have a dedicated cueing lever, many models, especially those designed for performance or audiophile use, offer this convenient feature. Its presence can greatly enhance the overall user experience and provide more precise control over the playback of vinyl records.
Overall, the cueing lever is a valuable tool that enables users to lift and lower the tonearm with precision and control. It serves to protect the stylus and record from damage while allowing for accurate positioning and a seamless listening experience.
Start/Stop Button
The start/stop button is a key feature found on turntables that allows users to control the rotation of the platter and initiate or cease the playback of vinyl records. It offers a convenient way to start and stop the music, providing flexibility and control during the listening experience.
When the start/stop button is pressed, it engages the turntable’s motor, causing the platter to begin rotating at the selected speed. This allows the stylus to make contact with the record’s grooves and initiate the playback of the music. Conversely, when the button is pressed again, the motor is disengaged, and the rotation of the platter comes to a halt, gradually reducing the movement to prevent any sudden jarring.
The start/stop button is particularly useful when manually cueing a record. By pressing the button, users can first position the tonearm and stylus at the desired starting point on the record and then activate the rotation of the platter to begin playback. This feature ensures a seamless and controlled transition from cueing to playback, minimizing the risk of scratching or damaging the record.
Additionally, the start/stop button allows for convenient control over the listening experience. Users can quickly start or stop the music as desired, providing flexibility in managing the playback of vinyl records. It also eliminates the need for manual rotation of the platter, providing a user-friendly and efficient way to control the turntable.
Some turntables may offer additional functionality through the start/stop button, such as auto-stop features. These features automatically stop the rotation of the platter when the record reaches its end, preventing any unnecessary wear on the record and stylus. This is particularly useful when playing longer records, as it ensures that the turntable automatically stops spinning once the final track is finished.
The start/stop button should be operated with care, ensuring gentle and controlled activation or deactivation of the motor. Rough handling of the button or abrupt actions can lead to stylus skips or potential damage to the record. It is important to exercise caution and familiarize oneself with the operation of the start/stop button to ensure the longevity of the equipment and optimum sound quality.
Overall, the start/stop button is a valuable feature on turntables, offering convenient control over the rotation and playback of vinyl records. It provides a seamless transition from cueing to playback and allows users to have greater flexibility and command in managing the music listening experience.
Pitch Control
Pitch control is a feature found on many turntables that allows users to adjust the rotational speed of the platter. It provides the ability to slightly increase or decrease the playback speed, known as the pitch, of the music being played. This feature is particularly useful for DJs, musicians, and audio enthusiasts who require precise control over the tempo and pitch of the music.
Pitch control is achieved by adjusting the voltage supplied to the turntable’s motor. Increasing the voltage leads to a higher rotational speed and a corresponding higher pitch, while decreasing the voltage results in a slower speed and lower pitch. The amount of pitch adjustment available can vary across different turntables.
The pitch control feature offers several benefits. For DJs, it allows for beat matching, where they can synchronize the tempo and phase of two songs to create seamless transitions. It also enables pitch bending, where slight adjustments in the pitch are made to create unique audio effects or to match the key of different songs. Musicians can also use pitch control to practice or play along with records while keeping the music in the desired key.
When using pitch control, it’s important to be mindful of certain considerations. Excessive pitch adjustment beyond the recommended range may result in noticeable distortion or affect the playback quality. It’s essential to listen carefully and make adjustments within reasonable limits to maintain the fidelity of the music.
Some turntables may have pitch control with a selectable range, allowing users to fine-tune the speed adjustments to their preference. Additionally, advanced turntables may offer features such as quartz-lock or digital pitch control, which ensure precise and stable pitch adjustments, even during prolonged playback.
It’s worth noting that the pitch control feature may not be essential for all listeners or turntable users. Those primarily interested in traditional listening experiences may not require or utilize this functionality as extensively as DJs or musicians. However, having access to pitch control provides versatility and allows for creative possibilities when interacting with vinyl records.
In summary, pitch control is a valuable feature found on turntables that enables users to adjust the rotational speed and pitch of the music being played. It offers flexibility for beat matching, pitch bending, and other creative applications, making it a vital tool for DJs, musicians, and audio enthusiasts seeking precise control over the playback experience.
RCA Outputs
RCA outputs are an important feature found on turntables that allow for easy connection to external audio devices such as amplifiers, receivers, or speakers. RCA, or “phono,” outputs utilize the standard red and white connectors that transmit audio signals in analog form.
The RCA outputs on a turntable serve as the primary means of connecting the turntable to an audio system. They provide a direct audio signal path from the turntable’s built-in phono preamp or the phono stage of an external preamp to the audio system, ensuring proper amplification and reproduction of the vinyl record’s sound.
When connecting the turntable to an audio system, the RCA outputs are typically plugged into the corresponding RCA input jacks on the amplifier, receiver, or preamp. The red connector corresponds to the right channel, while the white or black connector corresponds to the left channel, providing a stereo audio signal.
It’s important to note that some turntables may offer additional RCA outputs or features, such as a dedicated grounding terminal. The grounding terminal helps to eliminate any unwanted hum or interference that may occur due to electrical grounding issues. It provides a connection point for an external grounding wire that can be attached to the grounding post of the amplifier or receiver.
Modern turntables often include a built-in phono preamp or a switchable phono/line level output, which allows users to connect directly to line-level inputs on amplifiers or receivers without a separate phono preamp. In such cases, the turntable’s RCA outputs can be connected to any available line-level inputs on the audio system, such as CD, AUX, or line inputs.
When utilizing the RCA outputs, it’s important to use quality shielded RCA cables to minimize interference and ensure optimal signal transmission. Additionally, checking the input sensitivity and impedance settings on the audio system and adjusting them to match the turntable’s output specifications can help optimize sound quality.
RCA outputs provide a versatile and widely compatible interface for connecting turntables to audio systems. They enable users to enjoy the warm and authentic sound of vinyl records through their preferred amplification and speaker setup, making them an essential feature for vinyl enthusiasts and audiophiles.
Grounding Terminal
The grounding terminal is a crucial component found on many turntables that helps eliminate unwanted electrical noise and interference, ensuring optimal audio playback. It provides a connection point for a grounding wire that connects the turntable to an amplifier or receiver.
The ground wire serves to establish a common electrical ground between the turntable and the audio system. It helps to reduce or eliminate any potential hum or buzzing noise that may occur due to grounding issues or electrical interference. The grounding wire provides a path for any stray electrical currents or induced radio frequency interference to exit the turntable and flow into the audio system’s grounding system.
Connecting the grounding wire is a simple process. One end of the wire is typically attached to the grounding terminal on the turntable, while the other end is connected to the grounding post on the amplifier or receiver. The grounding post is typically labeled as “GND” or “Ground,” and it can often be found near the input connectors of the audio system.
The length and quality of the grounding wire can impact its effectiveness. It is generally recommended to use a high-quality, shielded grounding wire that is as short as possible to minimize any potential interference. A quality grounding wire can help maintain a clean and noise-free signal path, ensuring optimal sound quality.
It’s important to note that not all turntables require a separate grounding wire. Some turntables have built-in grounding mechanisms or utilize a grounded power cord to address grounding issues. In such cases, a separate grounding wire may not be necessary. However, if any hum or noise is present during playback, connecting a grounding wire can often resolve the issue.
The grounding terminal is particularly useful in situations where there may be a difference in electrical potential between the turntable and the audio system. This can occur due to various factors, such as different power outlets or electronic equipment in the setup. By establishing a common ground through the grounding terminal, any potential electrical imbalances are addressed, resulting in cleaner and more accurate audio reproduction.
In summary, the grounding terminal plays an essential role in minimizing electrical noise and interference in turntables. Connecting a grounding wire from the turntable to the amplifier or receiver’s grounding post establishes a common ground, reducing hum and ensuring optimal audio playback quality. It is a vital feature for achieving clean and noise-free sound when enjoying vinyl records.
Power Switch
The power switch is a fundamental component found on turntables that provides control over the electrical power supply to the device. It allows users to turn the turntable on or off, providing a convenient way to manage power consumption and operation.
The power switch is typically located on the front, side, or back panel of the turntable, easily accessible for users to toggle the power state. When the power switch is turned on, it enables the turntable’s motor, electronics, and other components to receive power from the electrical outlet.
Turning the power switch off disconnects the turntable from the power source, effectively shutting down all electrical flow and activity within the device. This feature is particularly useful for conserving energy when the turntable is not in use, reducing electricity consumption and prolonging the lifespan of the equipment.
It’s essential to note that when using the power switch, it’s important to follow proper procedures to minimize the risk of damage to the turntable or vinyl records. It’s advisable to wait for the platter to come to a complete stop before turning off the power switch, ensuring the stylus is safely lifted from the record grooves to prevent scratching or any other potential harm.
Some turntables may have additional power-related features, such as automatic power-off or standby modes. These features automatically shut down or enter a low-power state after a specific period of inactivity, further reducing power consumption and extending the life of the device.
When setting up a turntable, it’s essential to ensure that the power switch is in the correct position, in line with the appropriate voltage and electrical standards of the region. Using the incorrect voltage setting can potentially damage the turntable’s electronics or lead to inadequate performance.
Overall, the power switch is a crucial feature that provides users with control over the turntable’s electrical power supply. It allows for energy conservation and safety measures, ensuring efficient use and protection of the equipment. Proper handling and adhering to safety precautions when using the power switch contribute to the longevity and optimal performance of the turntable.
Conclusion
Turntables are captivating audio devices that offer a unique and authentic listening experience for vinyl enthusiasts and music lovers alike. Understanding the various components and features of a turntable is essential for maximizing its performance and enjoying the full potential of vinyl records.
In this article, we explored the key components of a turntable, including the tonearm, cartridge, platter, motor, drive system, speed selector, stylus, tracking force adjustment, anti-skate adjustment, cueing lever, start/stop button, pitch control, RCA outputs, grounding terminal, and power switch.
The tonearm holds the cartridge and stylus, allowing for precise tracking of the record grooves. The cartridge, with its stylus, converts the mechanical vibrations into electrical signals for sound reproduction. The platter ensures smooth rotation and stability while maintaining accurate speeds.
The motor and drive system transfer power and provide stability for consistent playback. Speed selectors allow users to choose the appropriate rotation speed for different vinyl records. The stylus is responsible for reading the grooves accurately, while tracking force adjustment and anti-skate adjustment fine-tune the pressure and alignment for optimal playback.
The cueing lever offers precise control over the tonearm’s positioning, while the start/stop button initiates or ceases playback. Pitch control allows for adjustments of the playback speed for beat matching or creative effects. RCA outputs provide connections to external audio devices, while the grounding terminal helps eliminate unwanted electrical noise.
By understanding and utilizing these components and features, users can achieve enhanced sound quality, extended longevity of equipment and records, and a more immersive vinyl listening experience.
In conclusion, turntables are not just audio devices; they are gateways to a nostalgic and rich musical journey. Whether you’re an audiophile, a DJ, or simply a music enthusiast, exploring the intricacies of turntable components and features allows you to unlock the true potential of vinyl records and immerse yourself in the beauty of analog sound.
So, dust off your vinyl collection, set up your turntable, and savor the unique experience of spinning records and letting the music come to life.