Home>Devices & Equipment>Turntable>How Does A Turntable Work
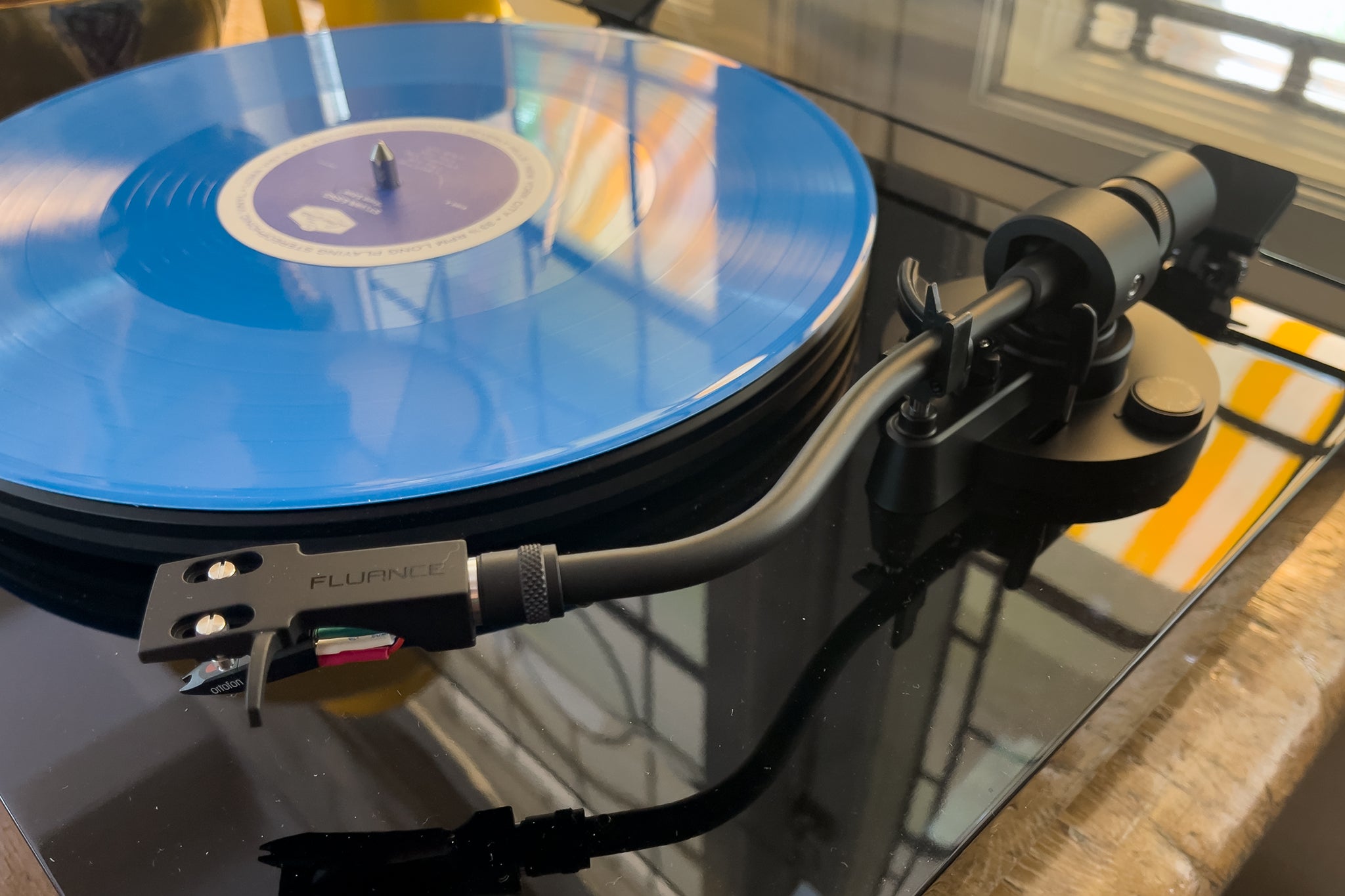
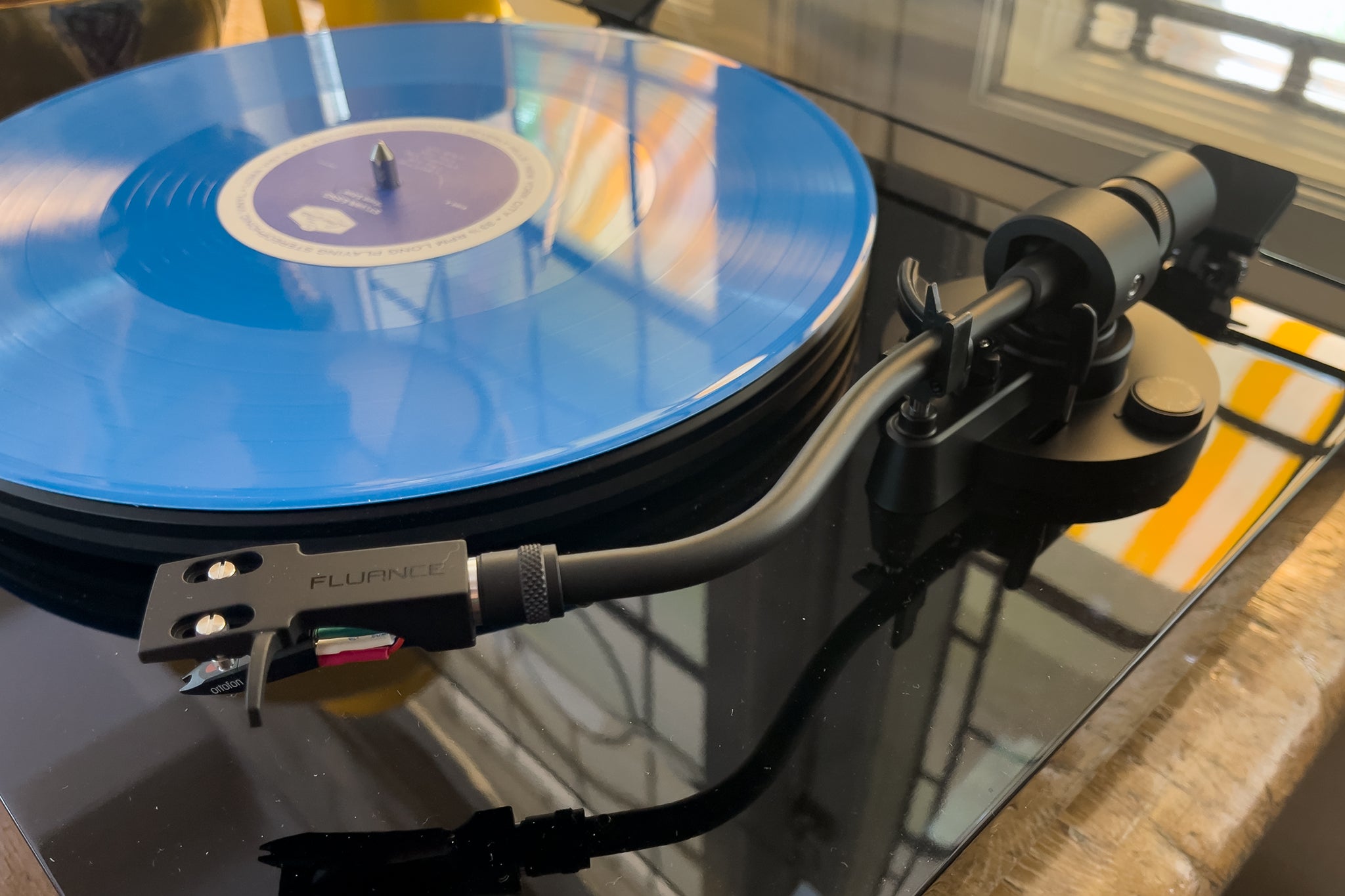
Turntable
How Does A Turntable Work
Modified: January 22, 2024
Discover the inner workings of a turntable and learn how this classic audio device brings your vinyl records to life. Explore the mechanics and sound technology behind turntables.
(Many of the links in this article redirect to a specific reviewed product. Your purchase of these products through affiliate links helps to generate commission for AudioLover.com, at no extra cost. Learn more)
Table of Contents
Introduction
Turntables have been the preferred audio playback devices for music enthusiasts for decades. While digital formats have gained popularity in recent years, the distinct sound and nostalgia of vinyl records continue to captivate a dedicated following. In this article, we will delve into the inner workings of turntables, exploring the components and mechanisms that make them function.
A turntable, also known as a record player, is a device that plays vinyl records. It consists of several key components that work together to reproduce sound. Understanding these components is crucial in appreciating the intricacies of turntables and the unique experience they offer.
By examining the platter, motor, tonearm, cartridge, stylus, and other related mechanisms, we can truly grasp the magic behind the turntable. Additionally, we will explore how these components interact to produce sound, as well as the role of vinyl records in the process.
While turntables may seem simple on the surface, they possess a complexity that distinguishes them from other audio playback devices. By unraveling this complexity, we can gain a deeper appreciation for the craftsmanship and engineering that goes into creating a quality turntable.
So, let’s take a closer look at the fascinating world of turntables and uncover the secrets behind their smooth operation and exceptional sound reproduction.
Components of a Turntable
A turntable is composed of several crucial components that work together to create a rich and accurate audio experience. Understanding these components is essential for anyone seeking to delve into the world of vinyl records and appreciate the craftsmanship of a well-designed turntable. Let’s explore each of these components in detail:
- The Platter: The platter is the circular platform where the vinyl record is placed. It provides stability and rotational motion, allowing the record to spin smoothly.
- The Motor: The motor is responsible for driving the rotation of the platter. There are two main types of motors used in turntables: belt-driven and direct-drive. Belt-driven turntables use an elastic belt to transfer power from the motor to the platter, reducing motor noise and vibrations. Direct-drive turntables, on the other hand, have the motor directly connected to the platter, offering more accurate speed control and eliminating belt-related issues.
- The Tonearm: The tonearm is a crucial component that holds the cartridge and stylus and guides them along the grooves of the vinyl record. It is responsible for maintaining consistent and accurate tracking of the record. Tonearms can come in different designs, such as the traditional pivoted tonearm or the more modern linear tracking tonearm.
- The Cartridge: The cartridge is a small device that houses the stylus and converts the mechanical vibrations from the record grooves into electrical signals. There are two main types of cartridges: moving magnet (MM) and moving coil (MC). Each type offers its own characteristics in terms of sound quality and tracking ability.
- The Stylus: The stylus, also known as the needle, is the part of the cartridge that makes direct contact with the record grooves. Its shape and quality are crucial factors in accurately and delicately tracing the grooves and extracting the audio signals.
These components work in harmony to reproduce the audio from the vinyl record. The platter rotates the record, the tonearm guides the cartridge and stylus along the grooves, and the cartridge’s stylus translates the mechanical vibrations into electrical signals. This electrical signal is then amplified and sent to speakers or headphones, resulting in the beautiful sound we hear.
Understanding these components is not only fascinating but also important when it comes to selecting a turntable. The quality of these components directly impacts the performance and sound reproduction of the turntable. Therefore, investing in a well-built turntable with high-quality components is crucial for a satisfying vinyl listening experience.
The Platter
The platter is a crucial component of a turntable, serving as the foundation for playing vinyl records. It is a circular platform that provides stability and rotational motion, allowing the record to spin smoothly. While it may seem like a simple part, the platter plays a significant role in ensuring accurate sound reproduction and minimizing unwanted vibrations.
Platters can be made from various materials, each with its own characteristics and impact on sound quality. Some common materials used for platters include aluminum, acrylic, glass, and even high-density polymers. The choice of material can affect the overall weight, resonance, and dampening properties of the platter.
Weight is an important consideration when it comes to platters. A heavier platter helps maintain speed stability by reducing fluctuations caused by external factors such as vibrations or variations in motor torque. Additionally, a heavier platter can improve the overall sound quality by mitigating resonances and vibrations that can interfere with the stylus’ tracking ability.
Another consideration is the platter’s surface. A smooth and level surface ensures that the vinyl record remains stable during playback, minimizing any unwanted wow and flutter effects. Some platters even incorporate additional features, such as a mat or a vinyl grip, to provide additional damping and grip for the record.
In modern turntables, you may also come across the concept of a sub-platter. The sub-platter sits on the main platter and is connected to the motor. Its purpose is to reduce motor noise and isolate any vibrations generated by the motor from directly affecting the main platter and record playback. This isolation helps maintain audio fidelity and reduce interference.
When it comes to platter design, you may encounter both single-piece and multi-piece platters. Single-piece platters are made from a single material, while multi-piece platters may have a separate center hub and a different material for the outer portion. Multi-piece platters offer benefits such as improved weight distribution and improved resonance control.
Overall, the platter is a critical component of a turntable, providing stability, rotational motion, and contributing to the overall sound quality. It is worth considering the material, weight, and design of the platter when selecting a turntable, as it can have a noticeable impact on your vinyl listening experience.
The Motor
The motor is a fundamental component of a turntable that drives the rotation of the platter. It plays a crucial role in maintaining a consistent and accurate speed, which is essential for precise sound reproduction. There are two main types of motors used in turntables: belt-driven and direct-drive.
In a belt-driven turntable, the motor is located off-center and drives the platter through an elastic belt. This design reduces motor noise and vibrations from directly affecting the platter, resulting in smoother rotation. The belt acts as a buffer, isolating any mechanical disturbances that the motor might generate. It also helps reduce wow and flutter, which are speed variations that can distort the sound quality.
On the other hand, in a direct-drive turntable, the motor is placed directly under the platter, with no need for a belt. This design offers more direct control over the platter’s rotation speed since there is no intermediary mechanism. Direct-drive turntables are capable of faster start-up times and more precise speed adjustments. They also tend to be more durable and have higher torque, making them suitable for DJing and scratching applications.
When it comes to motor types, turntables can use either synchronous or asynchronous motors. Synchronous motors rely on the frequency of the power supply to determine their rotational speed. They are commonly used in belt-driven turntables and require stable power to maintain consistent speed. Asynchronous motors, on the other hand, are self-regulating and do not rely on the power supply frequency. They are commonly found in direct-drive turntables and offer better speed stability and accuracy.
A high-quality motor is essential for accurate speed control and overall performance. The motor’s ability to maintain a constant speed directly impacts the accuracy of audio playback. Additionally, low vibration and noise levels are critical to minimize unwanted interference with the stylus’ tracking ability and decrease background noise.
Some advanced turntables may incorporate additional motor control features, such as electronic speed adjustment or the ability to switch between different playback speeds (e.g., 33 1/3 RPM and 45 RPM). These features provide further flexibility and convenience for the user, allowing them to adapt to different vinyl records and preferences.
Ultimately, whether belt-driven or direct-drive, synchronous or asynchronous, the motor is a vital component of a turntable. Its performance directly influences the accuracy of speed control and the overall sound quality. When considering a turntable, it is essential to evaluate the motor’s design and specifications to ensure optimal performance and a satisfying vinyl listening experience.
The Tonearm
The tonearm is a critical component of a turntable that holds the cartridge and stylus and guides them along the grooves of the vinyl record. Its primary function is to ensure accurate tracking and maintain consistent contact between the stylus and the record surface. The design and quality of the tonearm greatly impact the overall performance and sound reproduction of a turntable.
Tonearms come in various designs, but the two most common types are pivoted and linear tracking tonearms.
Pivoted tonearms are the traditional and widely used type. They consist of a straight arm with a pivot point near the base. The cartridge and stylus attach to the end of the tonearm, allowing them to float and move freely across the record surface. The counterweight at the rear of the tonearm provides proper tracking force, ensuring the stylus maintains contact with the grooves. Pivoted tonearms offer a balance of simplicity and performance, allowing for effective tracking and sound reproduction.
On the other hand, linear tracking tonearms are a more advanced and complex design. Instead of pivoting, the tonearm moves laterally in a straight line across the record. This design minimizes tracking error, as the stylus maintains a consistent angle and contact across the entire record surface. Linear tracking tonearms often incorporate additional features such as sensors and servo motors to ensure precise tracking and reduce friction.
Key considerations when evaluating tonearm performance include effective mass, anti-resonance features, and adjustability. Effective mass refers to the mass of the tonearm and how it interacts with the cartridge’s compliance (the cartridge’s ability to follow the grooves’ movements). A well-balanced combination of effective mass and cartridge compliance is essential for accurate tracking and optimal sound quality.
Anti-resonance features aim to minimize vibrations and resonance within the tonearm, reducing interference with the cartridge and stylus. This can include materials with high damping properties or innovative construction techniques to dampen vibrations that could degrade the sound quality.
Adjustability is another critical aspect of a tonearm. Being able to adjust tracking force, anti-skating force (which prevents the tonearm from pulling towards the center), and vertical tracking angle allows for fine-tuning the tonearm’s performance to ensure precise tracking and optimal sound quality.
The tonearm is a meticulous balance of mechanical precision and design. It plays a crucial role in translating the mechanical movements of the stylus into electrical signals that can be amplified and heard. A well-crafted tonearm ensures accurate tracking, minimal distortion, and faithful sound reproduction that captures the true essence of the music.
The Cartridge
The cartridge is a vital component of a turntable that houses the stylus and is responsible for converting the mechanical vibrations from the record grooves into electrical signals. This electrical signal is then amplified and sent to speakers or headphones, allowing us to hear the music. The design and quality of the cartridge greatly influence the accuracy and fidelity of the sound reproduction.
There are two main types of cartridges used in turntables: moving magnet (MM) and moving coil (MC).
• Moving Magnet (MM) Cartridges: MM cartridges are the most common and widely used type. They have a magnet attached to the end of the stylus cantilever, which moves within fixed coils. As the stylus tracks the record grooves, the vibrations create changes in the magnetic field, generating small electrical signals. MM cartridges generally offer good sound quality, ease of use, and compatibility with a wide range of turntables.
• Moving Coil (MC) Cartridges: MC cartridges are considered to offer higher fidelity and more detailed sound reproduction compared to MM cartridges. In this design, the coils are attached to the cantilever, and the magnet is fixed. The movement of the coils within the fixed magnet generates electrical signals. MC cartridges usually require more precise setup and are more expensive than MM cartridges, but they can provide exceptional sound quality for discerning audiophiles.
When selecting a cartridge, several factors should be considered:
• Sound Quality: The cartridge should be capable of accurately reproducing the frequencies and nuances within the record grooves. The choice between MM and MC will depend on personal preference and the desired level of sonic detail.
• Tracking Ability: A cartridge with good tracking ability ensures that the stylus stays in the record groove without jumping or skipping, even in demanding sections or with heavily modulated records.
• Tracking Force: The tracking force is the downward pressure applied by the cartridge’s stylus onto the record surface. It should be set correctly within the cartridge’s recommended range to avoid excessive wear on the stylus or record groove distortion.
• Compatibility: Some cartridges may require specific tonearm compatibility due to their weight and compliance characteristics. It is essential to ensure that the cartridge is compatible with your turntable’s tonearm and mounting options.
It’s worth noting that stylus shapes can also vary, with popular options being elliptical, conical, or line contact. Each shape offers advantages and trade-offs in terms of sound quality, tracking ability, and record wear.
Ultimately, the cartridge is a critical component that directly affects the sound quality and overall performance of a turntable. Choosing the right cartridge for your turntable is a crucial step in ensuring an enjoyable and accurate audio playback experience.
The Stylus
The stylus, also known as the needle, is a small but crucial part of the turntable’s cartridge. It is the component that makes direct contact with the record grooves, tracing the intricate patterns and translating them into audible sound. The design and quality of the stylus greatly impact the accuracy, tracking ability, and overall sound quality of a turntable.
Styli come in various shapes, each offering different advantages and characteristics:
• Conical: Conical stylus is the most common and affordable type. It has a rounded shape with a spherical tip, allowing it to make contact with a larger surface area of the groove. Conical styli are durable and can handle a wide range of record conditions but may lack the precision and detail of more specialized shapes.
• Elliptical: Elliptical styli have an elliptical-shaped tip, providing better contact with the record groove’s walls. This shape allows for more accurate tracing of the groove’s contours, resulting in improved detail and clarity in the sound reproduction. Elliptical styli are a popular choice for high-fidelity listening.
• Line Contact (or Microline): Line contact styli have a very narrow contact area with the record groove, tracing the grooves with the highest precision. This shape provides exceptional detail retrieval and resolution, capturing the subtlest nuances of the music. Line contact styli are often used by audiophiles and enthusiasts seeking the utmost fidelity.
When it comes to stylus materials, diamond is the most commonly used due to its hardness and durability. The stylus tip is usually made of a small diamond bonded to a metal shank. The quality of the diamond used in the stylus can impact its longevity and ability to accurately trace the record grooves.
It’s important to note that the stylus is a wear-and-tear component that requires proper care and occasional replacement. Over time, the stylus can wear down, leading to a decrease in sound quality and potential damage to the record surfaces. Regular cleaning and inspection of the stylus are recommended to ensure optimal performance and to prevent any potential damage to your records.
Choosing the right stylus for your turntable’s cartridge is crucial for accurate sound reproduction and preserving the condition of your records. The stylus shape, material, and quality directly impact the level of detail, tracking ability, and overall fidelity you can achieve. Understanding these factors will help you make informed decisions when selecting a stylus that best suits your listening preferences and equipment.
Understanding Vinyl Records
Vinyl records have been around for decades and continue to hold a special place in the hearts of music enthusiasts. Understanding the structure and characteristics of vinyl records can enhance your appreciation for the unique listening experience they offer.
Vinyl records are analog audio storage mediums that consist of a circular disc made of vinyl material. The record is divided into two sides, with each side containing grooves that spiral from the outer edge towards the center. These grooves hold the audio information that is played back by the turntable’s stylus.
The audio information on a vinyl record is encoded through the physical variations in the groove walls. As the stylus moves along the grooves, it vibrates according to the variations in the groove walls, generating electrical signals that correspond to the original sound waves.
There are two main sizes of vinyl records: 12-inch LP (long play) records and 7-inch singles. LP records typically hold around 20 minutes of music per side and are commonly used for full album releases, while singles typically hold one song per side.
Vinyl records also come in different speeds, with the most common being 33 1/3 revolutions per minute (RPM) for LP records and 45 RPM for singles. The speed at which the record spins affects the playback time and pitch of the audio. Some records may also be mastered at 78 RPM or have special editions with alternative speed options.
The material and quality of the vinyl used in records can vary, but most records are made from polyvinyl chloride (PVC). The vinyl disc is pressed with grooves using a master disc, creating a replica of the original recording. Additional care is given during the pressing process to ensure accurate groove depth and spacing to preserve the audio fidelity.
It’s worth noting that vinyl records require specific care to maintain their optimal condition and sound quality. Proper cleaning and handling techniques, as well as a clean and calibrated turntable setup, are crucial for enjoying the best possible playback and avoiding unnecessary wear on the record and stylus.
While digital music formats have become more prevalent, vinyl records continue to attract enthusiasts who appreciate the tactile experience, warm sound reproduction, and artistic value that they offer. Understanding the structure and characteristics of vinyl records can deepen your connection with the music and enrich your overall listening pleasure.
How Rotation and Speed Control Work
Rotation and speed control are critical aspects of a turntable’s operation, ensuring smooth playback and accurate sound reproduction. Let’s explore how rotation is achieved and how speed control is maintained in a turntable.
Rotation in a turntable is facilitated by the motor, which is responsible for spinning the platter that holds the vinyl record. The motor’s power is transmitted to the platter either directly (in direct-drive turntables) or indirectly through a belt (in belt-driven turntables).
In a direct-drive turntable, the motor is situated directly beneath the platter and is mechanically connected to it. The motor spins the platter directly, providing precise control over its rotation speed. Direct-drive turntables offer fast start-up times and accurate speed control, making them suitable for DJing and professional applications.
In a belt-driven turntable, the motor is located in a separate motor housing and drives the platter via an elastic belt. The motor’s rotation is transferred to the platter through the belt’s movement, resulting in the platter’s rotation. Belt-driven turntables provide additional isolation from motor vibrations and often exhibit smoother operation and lower noise levels compared to direct-drive models.
Speed control in turntables is crucial to maintain the correct playback speed of the vinyl record. Most turntables support at least two standard speeds: 33 1/3 revolutions per minute (RPM) for LP records and 45 RPM for singles. Some turntables also offer a third speed at 78 RPM for vintage or specialty records.
Speed control is achieved through a combination of mechanical and electronic mechanisms. In mechanical systems, the turntable may have different-sized pulleys or a manual speed selection mechanism to change between desired speeds. By adjusting the belt position on the pulley, the effective diameter of the platter changes, affecting its rotational speed.
Electronic systems use sensors and feedback loops to monitor and adjust the motor’s speed, ensuring accurate playback. These systems may incorporate quartz-locked or microprocessor-controlled technology to maintain precise speed control. Such systems can compensate for any speed fluctuations caused by factors like motor rpm variations, power fluctuations, or external factors that could affect the speed stability of the turntable.
Some advanced turntables may have user-selectable speed adjustments, allowing for finer control over the playback speed. These adjustments can be useful for fine-tuning the speed according to personal preference or compensating for slight variations in the recording or mastering process.
By maintaining consistent and accurate rotation speeds, turntables ensure that the stylus can accurately trace the grooves of the vinyl record, resulting in faithful sound reproduction. Whether through direct-drive or belt-driven mechanisms, combined with mechanical or electronic speed control, turntables provide a stable and controlled rotation that is essential for an enjoyable vinyl listening experience.
How Sound is Produced
Understanding how sound is produced in a turntable involves unraveling the intricate process by which mechanical vibrations from the record grooves are transformed into audible sound. Let’s explore this fascinating journey from the stylus to the speakers.
At the heart of the process is the stylus, also known as the needle. As the stylus traverses the record grooves, its tiny tip encounters the variations in the groove walls. These minute undulations result from the complex waveforms of the original music that was recorded.
As the stylus encounters these variations, it vibrates in response, causing the attached cartridge to move along with it. The cartridge contains magnets and coils that transform these mechanical vibrations into small electrical signals. These signals are essentially analog representations of the original audio waveforms.
The electrical signals generated by the cartridge are then carried through the tonearm wires to the turntable’s phono preamplifier. The phono preamp is responsible for amplifying and equalizing the delicate electrical signals from the cartridge to a level suitable for further amplification.
From the phono preamp, the amplified signals pass through the amplifier, which further boosts their power. At this stage, the signals are at a level sufficient to drive speakers or headphones, allowing us to hear the music.
With the amplified signals in hand, they are sent to the speakers or headphones, where they are converted back into sound. The speakers consist of drivers, which are composed of a diaphragm surrounded by a coil. As the electrical signals flow through the coil, it creates a magnetic field that interacts with a fixed magnet, causing the coil to move. This movement, in turn, vibrates the diaphragm, producing sound waves that we perceive as music.
It’s important to note that the quality of the turntable’s components, including the stylus, cartridge, tonearm, and speakers, greatly affects the accuracy and fidelity of sound reproduction. A well-designed and calibrated system ensures that the mechanical vibrations from the grooves are faithfully transformed into electrical signals and ultimately into immersive sound.
By understanding the remarkable journey from the stylus to the speakers, we can truly appreciate the complexity and ingenuity behind turntables and their ability to bring music to life in the analog realm. The magic lies in the precise tracking, conversion, amplification, and reproduction of the mechanical vibrations encoded within the vinyl record grooves.
Tracking and Anti-Skating Mechanisms
Tracking and anti-skating mechanisms play a crucial role in the performance of a turntable by ensuring accurate tracking of the stylus and minimizing unwanted tracking errors. Let’s delve into these mechanisms and understand their significance in delivering optimal sound reproduction.
Tracking Mechanism: The tracking mechanism refers to the system that maintains precise alignment of the stylus within the grooves of the vinyl record as it moves across its surface. Proper tracking ensures that the stylus reproduces the recorded sound accurately.
The tonearm, which holds the cartridge and stylus, is responsible for tracking. It is designed to balance the forces acting on the stylus, mainly tracking force and skating force, to achieve stable and accurate tracking.
Tracking force, often measured in grams, refers to the downward pressure exerted by the stylus on the record’s surface. This force ensures proper contact between the stylus and the groove walls. The appropriate tracking force varies depending on the cartridge’s specifications and typically falls within a recommended range provided by the manufacturer.
Anti-skating force is a counteracting force applied to the tonearm to prevent it from being pulled towards the center of the record by the groove modulation. The skating force results from the diagonal force generated by the stylus as it tracks the record grooves. Anti-skating mechanisms, such as weights or springs, apply an opposing force to counteract the skating force and maintain the stylus in the optimal position within the grooves.
Accurate tracking is vital as it ensures the stylus remains in the intended part of the groove, minimizing distortion and wear on both the stylus and the record. Improper tracking can lead to issues such as skipping, mistracking, or excessive record wear.
Anti-Skating Mechanism: The anti-skating mechanism helps address the skating force, minimizing its effect on the tonearm’s positioning and ensuring balanced tracking across the record. It helps to prevent the stylus from being pulled towards the center, resulting in more accurate groove tracing.
Typically, an anti-skate mechanism uses a mechanism such as a bias weight or a thread and weight system. The mechanism applies a force in the opposite direction of the skating force, offsetting its impact and keeping the tonearm in balance. Manufacturers often provide a recommended anti-skating setting, but adjustments might be necessary to achieve optimal performance for different cartridges and records.
Properly adjusted anti-skating contributes to improved channel balance, reduced distortion, and optimal stylus contact with the grooves. It helps maintain accurate stereo imaging and minimizes stress on the stylus, prolonging its lifespan.
By ensuring precise tracking and employing effective anti-skating mechanisms, turntables can provide a stable and reliable platform for reproducing the recorded sound with fidelity. Properly calibrated tracking and anti-skating systems enhance the overall audio experience and contribute to accurate playback of vinyl records.
Conclusion
Turntables are more than just devices for playing vinyl records; they are gateways to a world of immersive audio experiences. Understanding the inner workings of turntables can enhance our appreciation for the meticulous engineering and craftsmanship that goes into creating these musical marvels.
We explored the components of a turntable, including the platter, motor, tonearm, cartridge, and stylus. Each component plays a vital role in ensuring accurate sound reproduction and delivering a high-quality listening experience. The platter provides stability, the motor drives rotation, the tonearm guides the stylus, and the cartridge and stylus convert mechanical vibrations into electrical signals.
We also examined vinyl records, their sizes, speeds, and how they encode audio information within the grooves. Vinyl records offer a tactile and immersive listening experience that continues to attract a dedicated following. Understanding their structure and characteristics allows us to fully appreciate the beauty and nostalgia of vinyl playback.
Rotation and speed control mechanisms are crucial in maintaining accurate playback and speed consistency. Whether through direct-drive or belt-driven systems, coupled with mechanical or electronic speed control, turntables ensure stable rotation, preserving the fidelity of the sound and delivering a true representation of the recorded music.
Finally, we explored the tracking and anti-skating mechanisms that ensure precise stylus alignment and minimize tracking errors. These mechanisms contribute to accurate groove tracing, reduced distortion, and prolonged stylus and record longevity.
In conclusion, turntables are fascinating devices that blend art and science in delivering rich, analog audio experiences. From the intricate components to the precise tracking and anti-skating mechanisms, turntables offer a unique way to enjoy music by preserving the warmth, depth, and character of vinyl records. Whether you are a seasoned audiophile or new to the world of turntables, understanding their inner workings enhances your appreciation for the craftsmanship and brings you closer to the magic of vinyl sound reproduction.