Home>Instruments>Drums>How To Make Drums
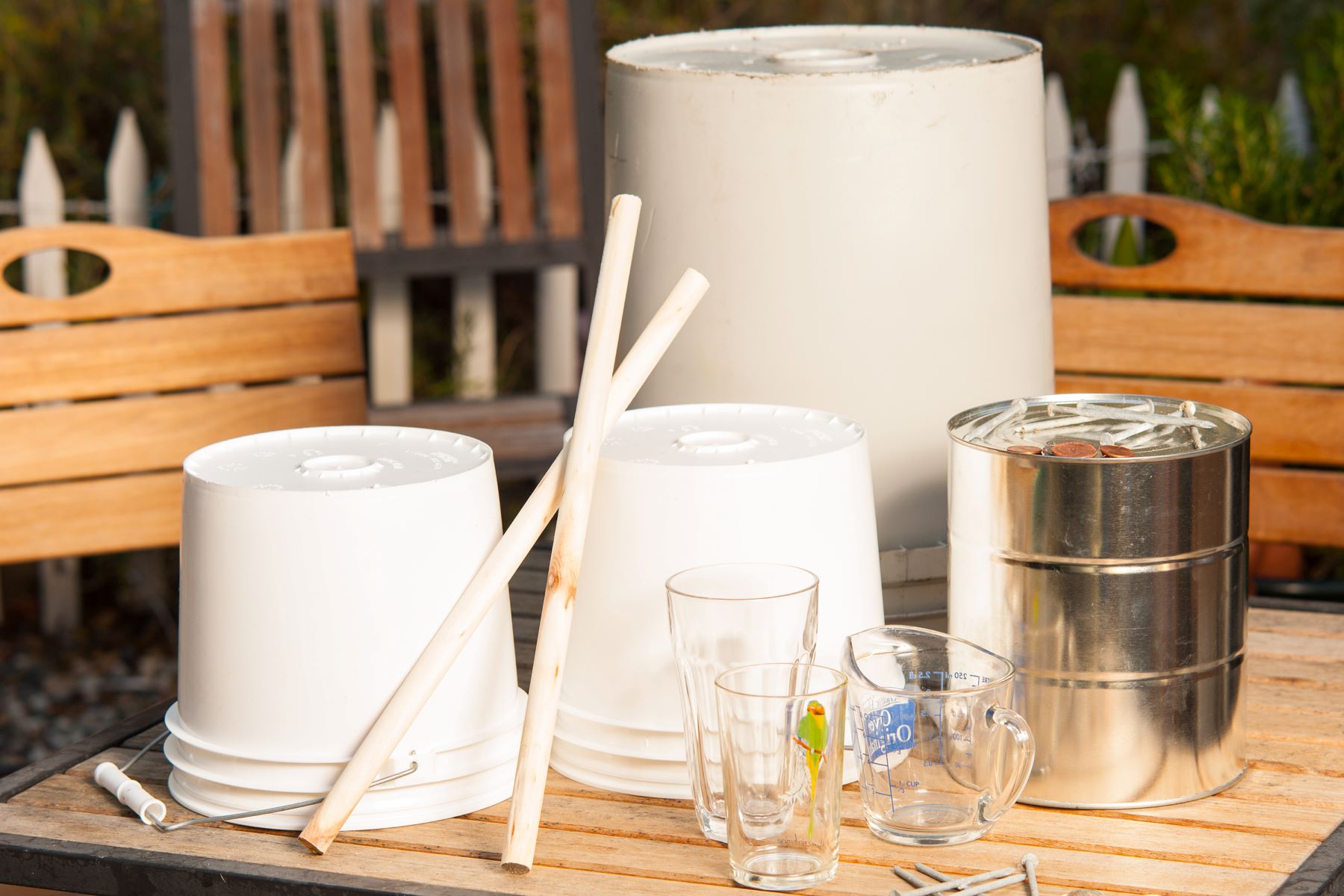
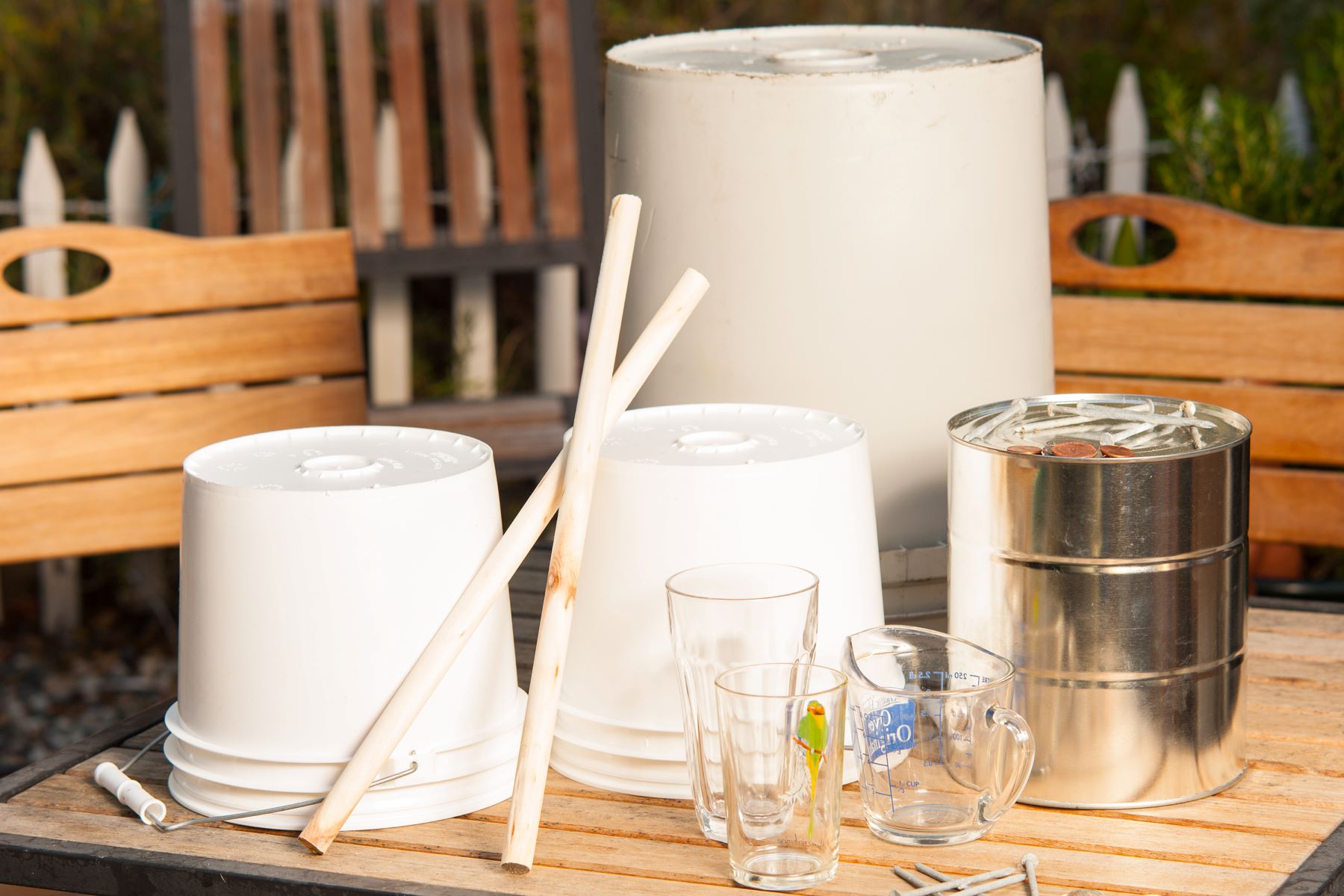
Drums
How To Make Drums
Published: February 8, 2024
Learn how to make drums from scratch with our step-by-step guide. Discover the essential tools and techniques for crafting your own unique percussion instrument. Start your drum-making journey today!
(Many of the links in this article redirect to a specific reviewed product. Your purchase of these products through affiliate links helps to generate commission for AudioLover.com, at no extra cost. Learn more)
Table of Contents
Introduction
Making drums is a fascinating and rewarding craft that has been practiced for centuries. The art of crafting a drum involves a deep understanding of materials, woodworking, and acoustics. Whether you are a percussion enthusiast, a musician seeking a custom sound, or simply an individual interested in hands-on craftsmanship, creating your own drum can be a fulfilling and enriching experience.
Throughout history, drums have held significant cultural and spiritual importance in various societies around the world. They have been used in rituals, ceremonies, and musical performances, serving as a means of communication and expression. Today, the tradition of drum making continues to thrive, with artisans and hobbyists alike honing their skills to produce unique and high-quality instruments.
In this comprehensive guide, we will delve into the intricacies of crafting a drum, from selecting the finest materials to tuning the instrument for optimal sound. Whether you aspire to construct a traditional hand drum, a snare drum, or a full drum kit, the principles and techniques outlined in this guide will provide you with a solid foundation to embark on your drum-making journey.
By understanding the nuances of drum construction, you can tailor the instrument to your specific preferences, creating a piece that resonates with your individual style and musical aspirations. So, roll up your sleeves, unleash your creativity, and let's explore the art of making drums from scratch.
Materials Needed
Before embarking on the exciting journey of drum making, it’s essential to gather the necessary materials and tools to ensure a smooth and successful crafting process. Here’s a comprehensive list of the primary materials and tools required:
- Wood for the drum shell
- Drum hardware (tension rods, lugs, and rims)
- Drumheads (top and bottom)
- Adhesives (wood glue, shellac, or other appropriate adhesives)
- Finishing materials (stains, lacquers, or oils)
- Woodworking tools (saws, chisels, planes, and sanding tools)
- Clamps
- Measuring tools (ruler, calipers, or measuring tape)
- Drill and drill bits
- Hammer and screwdriver
- Protective gear (safety goggles, gloves, and dust mask)
When selecting materials, it’s crucial to prioritize quality and suitability for the intended drum type. The wood chosen for the drum shell significantly influences the instrument’s tone and resonance, making it a pivotal aspect of the crafting process. Additionally, investing in durable drum hardware and high-quality drumheads is paramount for achieving a professional and long-lasting result.
By ensuring that you have all the necessary materials and tools at your disposal, you can approach the drum making process with confidence and focus on honing your woodworking skills and bringing your musical vision to life.
Choosing the Right Wood
When it comes to crafting a drum, the selection of wood for the drum shell is a critical decision that significantly impacts the instrument’s sound and overall quality. Different types of wood offer distinct acoustic properties, grain patterns, and durability, making the choice of wood a pivotal aspect of the drum-making process.
Several factors should be considered when choosing the wood for a drum shell:
- Acoustic Characteristics: Each type of wood possesses unique acoustic properties that contribute to the drum’s tone, resonance, and projection. For instance, maple is revered for its balanced and warm sound, birch offers pronounced attack and clear highs, and mahogany produces rich and deep tones.
- Strength and Durability: The chosen wood should be resilient enough to withstand the tension of the drumheads and the rigors of playing. Hardwoods such as oak and birch are favored for their durability, while softer woods like mahogany can offer a more resonant and lively sound.
- Grain Pattern: The grain pattern of the wood contributes to the visual appeal of the drum shell. Some drum makers prioritize visually striking grain patterns, while others focus on the sonic characteristics of the wood.
- Sustainability and Sourcing: Ethical considerations should be taken into account when selecting wood, ensuring that it is sourced responsibly and aligns with environmental conservation efforts.
Common woods used for drum shells include maple, birch, mahogany, oak, cherry, and walnut, each offering a unique sonic signature and aesthetic appeal. It’s essential to research and experiment with different wood types to gain a deeper understanding of their sonic qualities and suitability for specific drum designs.
Ultimately, the choice of wood is a deeply personal decision that reflects the desired sound, visual aesthetics, and craftsmanship philosophy of the drum maker. By carefully considering the acoustic characteristics, strength, grain pattern, and ethical sourcing of the wood, you can select the ideal material to bring your custom drum to life.
Cutting and Shaping the Drum Shell
The process of cutting and shaping the drum shell is a pivotal stage in drum making, requiring precision, attention to detail, and a deep understanding of woodworking techniques. The following steps outline the fundamental process of crafting a drum shell:
- Preparing the Wood: Start by selecting high-quality wood that aligns with the desired sonic characteristics and visual appeal of the drum. Ensure that the wood is free from defects and has been properly seasoned to prevent warping or cracking.
- Cutting the Staves: The drum shell is typically constructed from staves, which are individual segments of wood that form the circular shell. Carefully measure and cut the staves at precise angles to ensure a tight and seamless assembly.
- Shaping the Staves: Utilize woodworking tools such as planes and sanders to shape the staves with precision, ensuring that the edges align perfectly for a seamless shell construction. Attention to detail in this stage is crucial for achieving a uniform and structurally sound shell.
- Gluing and Clamping: Apply a high-quality wood glue to the edges of the staves and carefully assemble them into a circular form. Secure the staves with clamps, ensuring even pressure to promote strong and seamless adhesion.
- Trimming and Sanding: Once the glue has cured, carefully trim the excess wood from the shell and sand the exterior and interior surfaces to achieve a smooth and uniform finish. This step is essential for preparing the shell for the application of finishes and drum hardware.
Throughout the cutting and shaping process, meticulous attention to detail, patience, and a commitment to precision are essential. The craftsmanship and care invested in this stage directly impact the structural integrity, visual appeal, and sonic characteristics of the finished drum shell.
While the process of cutting and shaping a drum shell demands technical skill and woodworking expertise, it also offers an opportunity for creativity and individual expression. Each step in the process contributes to the unique character and quality of the drum, reflecting the artisan’s dedication to their craft and the pursuit of sonic excellence.
Assembling the Drum
Assembling the drum is a pivotal stage in the drum-making process, where the individual components come together to form a cohesive and functional instrument. This phase requires precision, attention to detail, and an understanding of drum hardware and construction techniques. The following steps outline the essential process of assembling a drum:
- Attaching Drum Hardware: Begin by carefully installing the drum hardware, including tension rods, lugs, and rims, onto the drum shell. Ensure that the hardware is positioned evenly and securely to facilitate proper tensioning of the drumheads.
- Installing the Drumheads: Place the appropriate drumheads (top and bottom) onto the drum shell, ensuring that they are aligned and seated correctly. The choice of drumheads significantly influences the drum’s sound and responsiveness, making it essential to select high-quality heads that suit the desired tonal characteristics.
- Securing the Drumheads: Use tension rods and tuning lugs to secure the drumheads onto the shell, applying even tension across the drumhead surface. Carefully tune the drumheads to achieve the desired pitch and resonance, taking care to maintain even tension and consistent tuning across all lugs.
- Quality Control and Fine-Tuning: Conduct a thorough inspection of the assembled drum, ensuring that all components are securely fastened and aligned. Fine-tune the drum’s hardware and tuning to optimize its sound and responsiveness, making any necessary adjustments to achieve the desired tonal characteristics.
Assembling a drum demands a meticulous approach, where each component’s placement, alignment, and tension significantly impact the instrument’s playability and sonic qualities. The artisan’s attention to detail and commitment to precision during this phase directly contribute to the drum’s overall quality and performance.
Moreover, the assembly process offers an opportunity for the drum maker to imbue the instrument with their unique craftsmanship and attention to detail, resulting in a custom drum that reflects their dedication to the art of drum making.
By following the prescribed steps and exercising care and precision throughout the assembly process, the drum maker can bring the instrument to life, ready to be played and appreciated for its exceptional craftsmanship and sonic character.
Adding Drumheads
Adding drumheads is a crucial step in the drum-making process, as the selection and installation of drumheads significantly influence the instrument’s sound, responsiveness, and tonal characteristics. Whether crafting a hand drum, snare drum, or bass drum, the choice of drumheads and their proper application are essential for achieving the desired sonic qualities. The following steps outline the process of adding drumheads to a drum:
- Selection of Drumheads: Choose drumheads that align with the desired sound and performance characteristics of the drum. Consider factors such as thickness, material composition, and coating options, as they directly impact the drum’s tonal response, sustain, and durability.
- Preparing the Drum Shell: Ensure that the drum shell is clean and free from any debris or residue that may affect the adhesion and performance of the drumheads. The bearing edges of the drum shell should be smooth and level to facilitate proper seating of the drumheads.
- Applying the Drumheads: Carefully position the selected drumheads onto the drum shell, ensuring that they are aligned and seated evenly. Pay close attention to the orientation of the drumheads, as their placement can influence the drum’s overall sound and playing feel.
- Tensioning the Drumheads: Use tension rods and tuning lugs to apply even tension across the drumheads, gradually tightening them to achieve the desired pitch and responsiveness. Consistent tensioning and tuning are essential for optimizing the drum’s sound and playability.
- Fine-Tuning and Testing: Once the drumheads are installed and tensioned, fine-tune their pitch and responsiveness to suit the desired tonal characteristics. Test the drum’s sound and responsiveness, making any necessary adjustments to achieve optimal performance.
Adding drumheads demands precision, patience, and a keen ear for sound quality, as the characteristics of the drumheads directly shape the instrument’s sonic identity. The artisan’s attention to detail and commitment to proper drumhead application contribute to the overall quality and playability of the drum.
Furthermore, the process of adding drumheads offers an opportunity for the drum maker to tailor the instrument’s sound and performance to their specific preferences, resulting in a custom drum that embodies their musical vision and craftsmanship.
By following the prescribed steps and exercising care and precision during the drumhead application process, the drum maker can ensure that the instrument delivers exceptional sound, responsiveness, and tonal versatility, ready to be enjoyed and appreciated for its craftsmanship and sonic character.
Tuning the Drum
Tuning a drum is a skillful art that significantly influences the instrument’s sound, resonance, and overall performance. Whether it’s a snare drum, bass drum, or tom-tom, achieving the perfect pitch and tonal characteristics is essential for maximizing the drum’s sonic potential. The following steps outline the process of tuning a drum to achieve optimal sound and responsiveness:
- Understanding Drum Tuning: Familiarize yourself with the fundamentals of drum tuning, including the impact of tension on the drumheads, the relationship between lugs, and the importance of achieving even tension across the drumhead surface. A well-tuned drum exhibits balanced pitch, clear tone, and consistent resonance.
- Initial Tensioning: Begin by applying even tension to the drumheads using a drum key or tuning wrench. Turn each tension rod in small increments, gradually tightening the drumheads to remove any wrinkles or slack while ensuring that the tension is consistent across all lugs.
- Listening and Adjusting: As you tension the drumheads, periodically tap the drum with a drumstick to assess the pitch and resonance. Listen for any inconsistencies or dissonance, and make precise adjustments to the tension of individual lugs to achieve uniform pitch and tone across the drumhead surface.
- Fine-Tuning the Sound: Once the initial tensioning is complete, fine-tune the drum’s sound by making subtle adjustments to the tension of specific lugs. Pay close attention to the drum’s responsiveness and tonal characteristics, aiming to achieve the desired pitch and resonance that complement the drum’s musical context and playing style.
- Testing and Refining: Test the drum’s sound and responsiveness by playing various patterns and dynamics. Make any necessary refinements to the tensioning based on the drum’s performance, ensuring that the instrument delivers the desired sound quality and playability.
Tuning a drum requires a combination of technical proficiency, a discerning ear, and a deep appreciation for sound quality. The artisan’s ability to meticulously tune a drum directly impacts its tonal versatility, responsiveness, and overall musical expressiveness.
Furthermore, the process of tuning a drum offers an opportunity for the drum maker to fine-tune the instrument’s sound to their specific preferences, resulting in a custom drum that embodies their musical vision and attention to sonic detail.
By following the prescribed steps and exercising care and precision during the drum tuning process, the drum maker can ensure that the instrument delivers exceptional sound, responsiveness, and tonal versatility, ready to be enjoyed and appreciated for its craftsmanship and sonic character.
Conclusion
The art of making drums is a deeply enriching and rewarding endeavor that intertwines craftsmanship, creativity, and a profound appreciation for sound. From selecting the finest materials to meticulously tuning the instrument, the process of crafting a drum is a testament to the artisan’s dedication to sonic excellence and musical expression.
Throughout history, drums have held profound cultural significance, serving as vehicles for communication, ritual, and artistic expression in diverse societies worldwide. The tradition of drum making continues to thrive, with artisans and enthusiasts channeling their passion and expertise into creating unique and exceptional instruments that resonate with individuality and artistry.
By delving into the intricacies of drum construction, aspiring drum makers can embark on a journey that not only yields a custom instrument but also fosters a deeper understanding of acoustics, woodworking, and the boundless possibilities of sound. The process of making drums is a celebration of craftsmanship, where each stage, from cutting and shaping the shell to fine-tuning the drum’s sound, reflects the artisan’s commitment to excellence and the pursuit of sonic perfection.
Furthermore, the act of crafting a drum is an act of storytelling, where the instrument becomes a tangible embodiment of the artisan’s creativity, dedication, and reverence for musical traditions. Whether crafting a traditional hand drum, a versatile snare drum, or a thunderous bass drum, the artisan’s imprint is woven into every aspect of the instrument, resulting in a truly personalized and exceptional creation.
Aspiring drum makers are encouraged to embrace the art of drum making with passion, patience, and a spirit of exploration. Each drum crafted is not only a testament to the artisan’s skill but also a unique voice in the symphony of percussion, poised to inspire and resonate with musicians and enthusiasts alike.
Ultimately, the journey of making drums transcends the mere act of construction; it is a transformative experience that unites tradition with innovation, craftsmanship with creativity, and the universal language of rhythm with the individual expression. Through the art of making drums, artisans continue to enrich the world of percussion, infusing it with their unique perspectives, and contributing to the timeless legacy of drum making.