Home>Production & Technology>Soundproofing>What Can I Mix Into Cement For Soundproofing
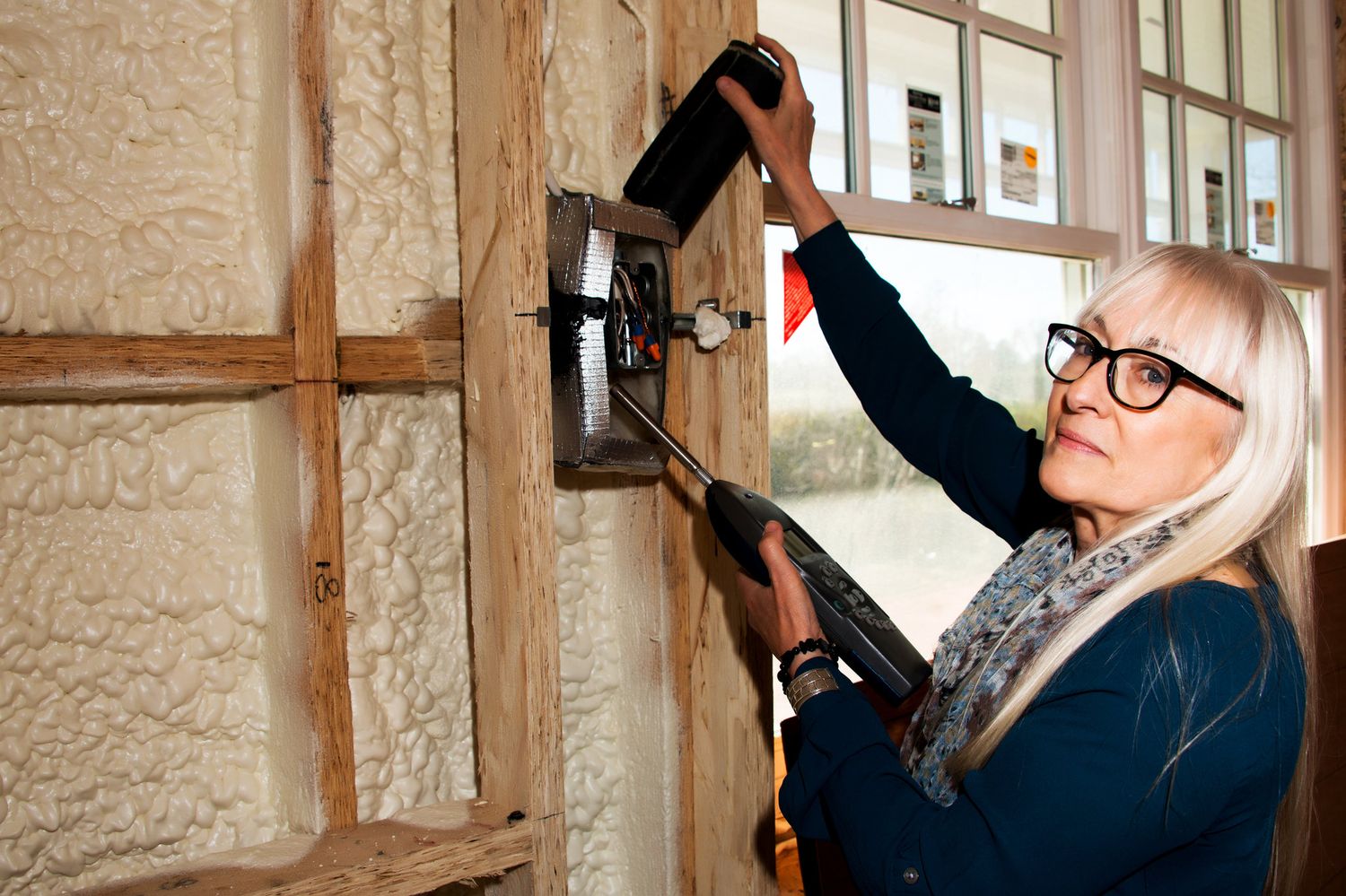
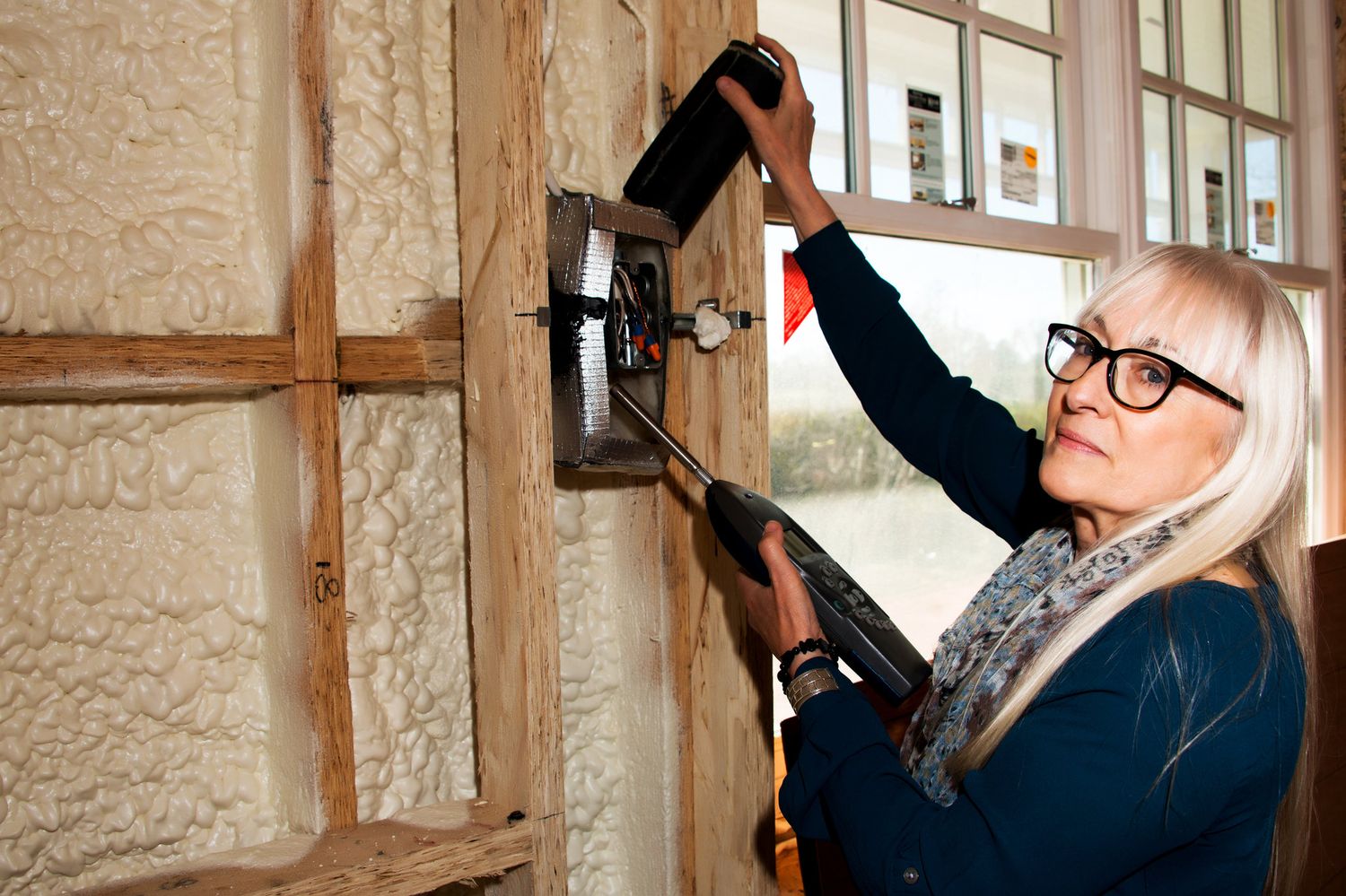
Soundproofing
What Can I Mix Into Cement For Soundproofing
Published: January 27, 2024
Enhance the soundproofing of your space by discovering what materials can be mixed into cement for effective noise reduction. Explore various options and techniques for a quiet and peaceful environment.
(Many of the links in this article redirect to a specific reviewed product. Your purchase of these products through affiliate links helps to generate commission for AudioLover.com, at no extra cost. Learn more)
Table of Contents
Introduction
Soundproofing is a crucial element in creating a peaceful and comfortable environment. Whether you live in a noisy neighborhood, work in a bustling office, or have a home recording studio, soundproofing can help minimize external noise and ensure better acoustics. While there are various methods and materials available for soundproofing, one effective approach is incorporating soundproofing additives into cement mixtures.
Soundproofing cement is a specialized type of concrete that contains materials designed to reduce sound transmission. By using soundproofing additives in cement, you can enhance its sound-dampening properties and create a barrier against unwanted noise. This can make a significant difference in reducing sound transfer between rooms, floors, or even outdoor spaces.
But what exactly are these soundproofing additives, and how do they work? In this article, we will delve into the world of soundproofing cement and explore the various materials that can be mixed into cement to enhance its soundproofing capabilities. We will discuss the benefits of fiber reinforcement, soundproofing additives, and insulating materials, as well as the proper mixing techniques and application methods.
Furthermore, we will also look at the considerations and limitations of using soundproofing cement, as it is important to understand its potential drawbacks and ensure that it is the right solution for your specific soundproofing needs. By the end of this article, you will have a comprehensive understanding of soundproofing cement and be armed with the knowledge to effectively utilize it in your soundproofing projects.
Understanding Soundproofing Cement
Soundproofing cement, also known as sound-dampening concrete, is a specialized type of concrete that is designed to reduce sound transmission. It consists of ordinary Portland cement mixed with various sound-absorbing materials. These materials help to absorb and dissipate sound waves, preventing them from passing through the cement structure.
The principle behind soundproofing cement is simple: by incorporating sound-absorbing materials into the mixture, it creates a dense, resilient, and acoustically efficient barrier. When sound waves encounter the soundproofing cement, they are partially absorbed and deflected, reducing their intensity and preventing them from traveling to the other side of the structure.
What sets soundproofing cement apart from conventional concrete is its ability to effectively block airborne sound and reduce structure-borne sound. Airborne sound refers to sound waves traveling through the air, while structure-borne sound refers to vibrations transmitted through physical structures, such as walls or floors. Soundproofing cement provides a dual benefit by attenuating both types of sound, making it an ideal choice for various applications.
It is important to note that soundproofing cement is not a complete solution for soundproofing. While it can significantly reduce noise transmission, achieving complete sound isolation often requires a combination of different soundproofing techniques, such as insulation, acoustic panels, and strategic placement of sound barriers. Soundproofing cement serves as a valuable addition to these methods, enhancing their effectiveness and providing an additional layer of sound insulation.
The effectiveness of soundproofing cement depends on various factors, such as the composition of the additives, the thickness of the cement layer, and the overall construction of the structure. It is essential to choose the right materials and follow proper mixing and application techniques to maximize the soundproofing performance of the cement.
In the following sections, we will explore the different materials that can be mixed into cement to enhance its soundproofing properties, as well as the proper techniques for mixing and applying soundproofing cement.
Common Soundproofing Materials for Cement Mixtures
When it comes to soundproofing cement, there are several materials that can be mixed into the cement mixture to enhance its sound-dampening properties. These materials work by absorbing or blocking sound waves, reducing the transmission of noise through the cement structure. Let’s take a look at some of the most commonly used soundproofing materials for cement mixtures:
1. Fiber Reinforcement: Fiber reinforcements, such as fiberglass or cellulose fibers, can be added to the cement mixture to improve its strength and soundproofing capabilities. These fibers help to reduce the transfer of sound waves by increasing the density and reducing the resonance of the cement structure. Additionally, they can enhance the overall durability and crack resistance of the soundproofing cement.
2. Soundproofing Additives: There are various soundproofing additives available in the market that are specifically designed to enhance the soundproofing properties of cement. These additives typically consist of minerals, fillers, and polymers that help to absorb and dissipate sound waves. They are mixed with the cement to create a more effective barrier against noise transmission.
3. Insulating Materials: In addition to sound absorption, incorporating insulating materials into the cement mixture can help to reduce sound transmission through thermal insulation. Materials like expanded polystyrene (EPS) foam or mineral wool can improve the overall soundproofing performance of the cement by providing an additional layer of insulation against both airborne and structure-borne noise.
4. Mass-Loaded Vinyl (MLV): Mass-loaded vinyl is a dense, flexible material that can be integrated into the cement mixture to block sound waves. It is highly effective at reducing both airborne and impact noise, making it a popular choice for soundproofing applications. MLV can be sandwiched between layers of soundproofing cement or used as a separate barrier to enhance the soundproofing performance of the cement structure.
5. Acoustic Panels: While not directly mixed into the cement, acoustic panels can be installed on the surface of the cement structure to further enhance its soundproofing abilities. These panels are designed to absorb sound waves and prevent them from bouncing off hard surfaces, effectively reducing echo and reverberation in the space.
It is important to note that the effectiveness of these soundproofing materials may vary depending on the specific requirements of your project. Consulting with a soundproofing expert or contractor can help you determine the most suitable materials for your cement mixture based on factors such as the level of noise reduction desired and the specific application.
In the next sections, we will explore the proper mixing techniques and application methods to ensure the optimal performance of soundproofing cement.
Fiber Reinforcement
Fiber reinforcement is a commonly used method to enhance the soundproofing properties of cement mixtures. Fibers, such as fiberglass or cellulose fibers, are added to the cement mixture to improve its strength, durability, and sound-dampening capabilities. Let’s take a closer look at how fiber reinforcement works:
1. Improved Strength: Adding fibers to the cement mixture increases its tensile strength, making it more resistant to cracking and structural damage. This is particularly beneficial in soundproofing applications, as the fibers help to maintain the integrity of the cement structure even under heavy vibrations or impact.
2. Density and Resonance: The presence of fibers in the cement mixture increases its density, which can help to reduce the transfer of sound waves. The fibers also disrupt the resonance of the cement structure, preventing sound from resonating or amplifying within the material.
3. Sound Absorption: Fibers have sound-absorbing properties, meaning they can absorb and dissipate sound energy. By incorporating fibers into the cement mixture, you create additional surfaces for sound waves to interact with, effectively reducing their transmission through the structure.
4. Flexibility: Fiber-reinforced cement tends to be more flexible than conventional cement, which can help to absorb and dampen vibrations. This is particularly useful for soundproofing applications where impact or structure-borne noise is a concern.
When using fiber reinforcement for soundproofing cement, it is important to choose the right type and amount of fibers. Fiberglass fibers, due to their high tensile strength and sound-absorbing qualities, are commonly used in soundproofing applications. Cellulose fibers, derived from wood or other plant sources, are another popular choice as they are eco-friendly and offer good sound-dampening properties.
The fibers should be evenly distributed throughout the cement mixture to ensure uniform soundproofing performance. Proper mixing techniques, such as using a concrete mixer and following manufacturer’s recommendations, help to achieve a homogenous distribution of fibers and optimize the strength and soundproofing capabilities of the cement.
It is important to note that while fiber reinforcement significantly improves the soundproofing properties of cement, it might not be sufficient on its own. It is often recommended to combine fiber reinforcement with other soundproofing materials and techniques, such as soundproofing additives or insulation, to achieve optimal noise reduction results.
In the next sections, we will explore the different types of soundproofing additives and insulating materials that can be mixed into cement to further enhance its sound-dampening capabilities.
Soundproofing Additives
Soundproofing additives are specifically designed materials that can be mixed into cement to enhance its sound-dampening properties. These additives work by absorbing or dissipating sound waves, reducing their transmission through the cement structure. Let’s delve into some of the common soundproofing additives used in cement mixtures:
1. Mineral Fillers: Mineral fillers, such as silica, limestone, or fly ash, can be added to the cement mixture to improve its soundproofing capabilities. These fillers help to increase the density of the cement, reducing the transfer of sound waves. They also assist in better sound absorption and resonance reduction.
2. Polymers: Soundproofing polymers, such as polyvinyl acetate (PVA) or polyurethane, are often used as additives in cement mixtures. These polymers act as viscoelastic materials, absorbing and dampening sound waves. The addition of polymers enhances the soundproofing properties of the cement, making it more effective in reducing noise transmission.
3. Rubber Granules: Incorporating rubber granules into the cement mixture can help to improve soundproofing performance. Rubber is known for its elasticity and ability to absorb sound energy. When added to the cement, the rubber granules act as shock absorbers, reducing impact noise and vibrations.
4. Viscoelastic Damping Compounds: These compounds are designed to reduce vibration and control noise transmission. They are typically mixed with the cement to create a sound-dampening layer. Viscoelastic damping compounds are effective at absorbing sound and dissipating vibration energy, making them an excellent choice for soundproofing applications.
5. Acoustic Fillers: Acoustic fillers, such as expanded perlite or vermiculite, can be added to the cement mixture to enhance its soundproofing properties. These fillers have excellent sound absorption capabilities and help to reduce sound transmission through the cement structure.
When incorporating soundproofing additives into cement mixtures, it is crucial to follow the manufacturer’s recommendations and guidelines. This ensures the proper mixing ratios and the desired soundproofing performance. It is also important to consider the specific requirements of your project and consult with soundproofing experts if needed.
Combining soundproofing additives with other soundproofing materials, such as fiber reinforcement or insulation, can further enhance the sound-dampening capabilities of the cement. By using a combination of additives and other techniques, you can create a robust soundproofing solution that effectively reduces noise transmission and enhances acoustic comfort.
In the next section, we will explore the role of insulating materials in soundproofing cement mixtures.
Insulating Materials
Insulating materials play a vital role in soundproofing cement mixtures by providing an additional layer of sound insulation. These materials are typically added to the cement mixture to enhance its sound-dampening properties and further reduce noise transmission. Let’s explore some commonly used insulating materials for soundproofing cement:
1. Expanded Polystyrene (EPS) Foam: EPS foam is a lightweight and versatile insulating material that is often added to the cement mixture. It helps to decrease sound transmission by absorbing and dissipating sound waves. EPS foam also has excellent thermal insulation properties, making it beneficial for both soundproofing and energy efficiency in buildings.
2. Mineral Wool: Mineral wool, also known as rock wool or stone wool, is a commonly used insulating material in soundproofing applications. It is made from natural or recycled minerals, such as basalt or limestone, and is highly effective at absorbing sound waves. Mineral wool can be included in the cement mixture to improve the overall soundproofing performance of the construction.
3. Foam Panels: Foam panels, such as polyurethane foam or acoustic foam, are frequently used in combination with soundproofing cement. These panels can be applied on top of the cement surface to further enhance its sound-dampening capabilities. Foam panels are designed to absorb sound waves and reduce echoes and reverberations in a space, making them an excellent addition to cement-based soundproofing systems.
4. Fiberglass Insulation: Fiberglass insulation is widely used for thermal insulation, but it can also provide soundproofing benefits. It can be inserted between layers of soundproofing cement to reduce the transmission of airborne and impact noise. Fiberglass insulation is lightweight, cost-effective, and easy to install, making it a popular choice for soundproofing applications.
5. Acoustic Underlayment: Acoustic underlayment materials, such as rubber or cork, can be used in conjunction with soundproofing cement to isolate and reduce impact noise. These materials are typically placed underneath the cement layer to absorb vibrations and prevent noise transmission through the floor. Acoustic underlayment can greatly enhance the overall soundproofing performance of cement-based applications.
When incorporating insulating materials into soundproofing cement, it is important to consider factors such as thickness, density, and the specific requirements of the project. Consulting with a soundproofing professional can help determine the most suitable insulating materials for your specific application.
By combining insulating materials with other soundproofing techniques, such as fiber reinforcement or soundproofing additives, you can create a comprehensive soundproofing system that effectively reduces noise transmission and enhances acoustic comfort.
In the next section, we will explore proper mixing techniques and the application of soundproofing cement.
Proper Mixing Techniques
Proper mixing techniques are essential to ensure optimal performance and soundproofing capabilities of cement mixtures. By following the correct procedures, you can achieve a homogenous and well-blended mixture that maximizes the effectiveness of the soundproofing materials. Here are some important factors to consider when it comes to mixing soundproofing cement:
1. Mixing Equipment: It is recommended to use a concrete mixer or a mortar mixer for mixing soundproofing cement. These machines ensure thorough and consistent mixing, resulting in a uniform distribution of soundproofing additives and fibers. Hand-mixing can be done if necessary, but it may be more challenging to achieve a consistent mixture.
2. Ratios and Measurements: Follow the manufacturer’s instructions and guidelines when it comes to mixing ratios and measurements. The correct proportions of cement, sand, water, and soundproofing additives should be used to achieve the desired soundproofing performance. Over or underestimating the amounts can compromise the effectiveness of the mixture.
3. Gradual Addition: When adding soundproofing additives, fibers, or insulating materials, it is best to add them gradually during the mixing process. This allows for better dispersion and integration throughout the cement mixture. Mix the cement and water first, and then slowly incorporate the additives while continuing to mix until a homogenous consistency is achieved.
4. Mixing Time: It is important to mix the cement mixture for the recommended duration to ensure proper blending. This duration may vary depending on the specific soundproofing materials used and the type of mixer employed. Adequate mixing time helps in achieving a consistent distribution of additives, fibers, and aggregates, resulting in a cohesive and effective soundproofing cement.
5. Monitoring Consistency: Pay attention to the consistency of the cement mixture during the mixing process. The ideal consistency may vary depending on the intended application. However, it is generally recommended to have a mixture that is not too dry or too wet. It should be workable and easy to apply, ensuring proper adhesion and soundproofing performance.
6. Testing and Adjustments: Perform periodic tests during the mixing process to ensure the desired properties are achieved. This can include slump tests to determine the workability of the mixture or density measurements to assess the soundproofing capabilities. If necessary, make adjustments to the mixture by adding additional materials or adjusting the water content to achieve the desired consistency and soundproofing performance.
Remember to consult the specific instructions provided by the manufacturers of the soundproofing materials and additives. They may have specific guidelines or ratios to follow for optimal soundproofing results.
By adhering to proper mixing techniques, you can ensure that your soundproofing cement mixture is well-prepared and optimized for sound insulation. In the next section, we will explore the application of soundproofing cement in different scenarios.
Application of Soundproofing Cement
The application of soundproofing cement is a crucial step in ensuring the desired soundproofing performance. The proper application technique will help create a solid barrier against noise transmission. Here are some key considerations when applying soundproofing cement:
1. Surface Preparation: Before applying soundproofing cement, ensure that the surface is clean, dry, and free from any contaminants. Remove any loose particles, dirt, or debris. If necessary, prime the surface to promote adhesion and improve the bond between the existing substrate and the soundproofing cement.
2. Masking and Protection: Prior to application, mask off and protect any adjacent areas or surfaces that should not be coated with soundproofing cement. Use drop cloths or plastic sheeting to prevent any splatters or spills from affecting other surfaces.
3. Application Techniques: Soundproofing cement can be applied using various techniques, such as troweling, spraying, or pouring. The specific method will depend on the project requirements and the consistency of the mixture. Follow the manufacturer’s instructions and guidelines for the recommended application technique.
4. Layer Thickness: The thickness of the soundproofing cement layer will depend on the specific soundproofing requirements and the materials used. It is important to achieve the desired thickness to effectively block and absorb sound waves. Multiple layers may be necessary to achieve optimal soundproofing performance, especially in areas with higher noise levels.
5. Curing and Drying: After application, allow the soundproofing cement to cure and dry as per the manufacturer’s recommendations. This curing process helps to develop the necessary strength and soundproofing properties. Ensure proper ventilation and curing time for the cement to fully set and achieve its optimal sound-dampening capabilities.
6. Maintenance and Finishing: Once the soundproofing cement is cured, it can be finished or painted as desired. Protect the surface from potential damage or wear by applying a protective coating or sealant. Regular maintenance and inspection are essential to ensure the long-term performance of the soundproofing cement.
It is worth noting that soundproofing cement is most effective when used in combination with other soundproofing techniques, such as proper sealing, insulation, or the use of acoustic panels. Consider the specific requirements of your project and consult with soundproofing experts to determine the best approach for achieving optimal soundproofing results.
In the next section, we will discuss some considerations and limitations when using soundproofing cement.
Considerations and Limitations
While soundproofing cement offers numerous benefits in reducing noise transmission, it is essential to understand its considerations and limitations to make informed decisions for your soundproofing project. Here are some important factors to consider:
1. Effectiveness: Soundproofing cement can significantly reduce noise transmission, but it may not provide complete sound isolation. The level of noise reduction achieved depends on various factors, such as the thickness of the cement layer, the specific soundproofing materials used, and the overall construction of the structure. It is crucial to have realistic expectations and assess whether soundproofing cement alone is sufficient for your desired level of noise reduction.
2. Application Area: Soundproofing cement is commonly used on walls, floors, and ceilings. However, it may not always be suitable for all surfaces or structural elements. Consider factors such as load-bearing capacity, flexibility requirements, and expansion and contraction properties when determining the applicability of soundproofing cement in your project.
3. Cost: Soundproofing cement can be more expensive than traditional cement due to the inclusion of additives, fibers, or insulating materials. The cost of materials and labor should be taken into account when budgeting for soundproofing projects. It is recommended to assess the cost-effectiveness and long-term benefits of soundproofing cement in relation to the specific noise reduction requirements.
4. Professional Expertise: Soundproofing projects may benefit from the expertise of soundproofing professionals or contractors who specialize in the field. They can provide valuable insights and recommendations tailored to your specific needs. Consulting with experts can help ensure that the right materials, techniques, and application methods are utilized for optimal soundproofing performance.
5. Structural Considerations: Soundproofing cement can add weight and thickness to the structure. It is important to assess the load-bearing capacity and structural integrity of the building to accommodate the additional weight. Consulting with structural engineers can help determine if any reinforcements or modifications are required to support the added mass of the soundproofing cement.
6. Building Codes and Regulations: Before embarking on a soundproofing project, it is important to familiarize yourself with local building codes and regulations. Some jurisdictions may have specific requirements or restrictions regarding soundproofing materials or techniques. Compliance with these regulations ensures a safe and legal soundproofing installation.
Understanding these considerations and limitations can help you make informed decisions and set realistic expectations when using soundproofing cement. Additionally, consulting with soundproofing professionals can provide valuable guidance to ensure an effective and long-lasting soundproofing solution for your space.
In the concluding section, we will summarize the key points discussed in this article.
Conclusion
Soundproofing cement is an effective solution for reducing noise transmission and creating a more peaceful environment. By incorporating soundproofing additives, fiber reinforcement, and insulating materials into cement mixtures, you can enhance its sound-dampening properties and create a barrier against unwanted noise. However, it is important to consider the limitations and factors discussed in this article to ensure optimal results in your soundproofing project.
Understanding the principles of soundproofing cement and the role of various materials, such as fiber reinforcement and soundproofing additives, is crucial. Proper mixing techniques, including gradual addition of additives and required mixing time, ensure a well-blended and consistent mixture. When applying soundproofing cement, surface preparation, layer thickness, and curing time are important factors to consider for optimal soundproofing performance.
However, it is essential to recognize that while soundproofing cement is effective in reducing noise transmission, it may not provide complete sound isolation. Additional soundproofing methods, such as insulation, acoustic panels, or strategic placement of sound barriers, may be necessary to achieve desired results.
Considering cost, structural considerations, and compliance with building codes and regulations is important as well. Consulting with soundproofing professionals can provide valuable expertise and guidance to tailor the soundproofing solution to your specific needs.
In conclusion, soundproofing cement is a valuable tool in creating a quieter and more comfortable environment. By utilizing the right materials, following proper mixing and application techniques, and considering the limitations and factors discussed, you can achieve effective noise reduction and enhance the acoustic comfort of your space.
Remember, soundproofing is a multifaceted process, and a comprehensive approach that combines various techniques and materials will yield the best results. Whether you’re soundproofing a residential, commercial, or industrial space, the application of soundproofing cement can contribute significantly to creating a tranquil and peaceful environment.