Home>Instruments>Brass Instruments>What Do You Call A Person That Makes Brass Instruments
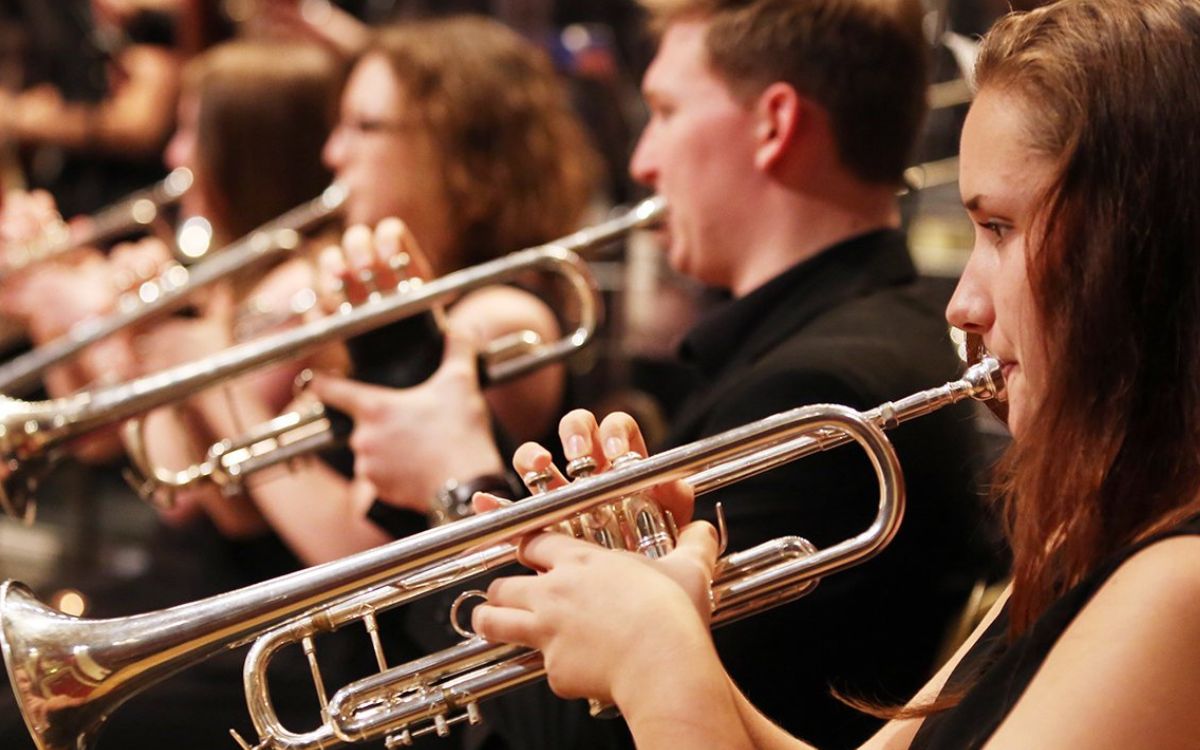
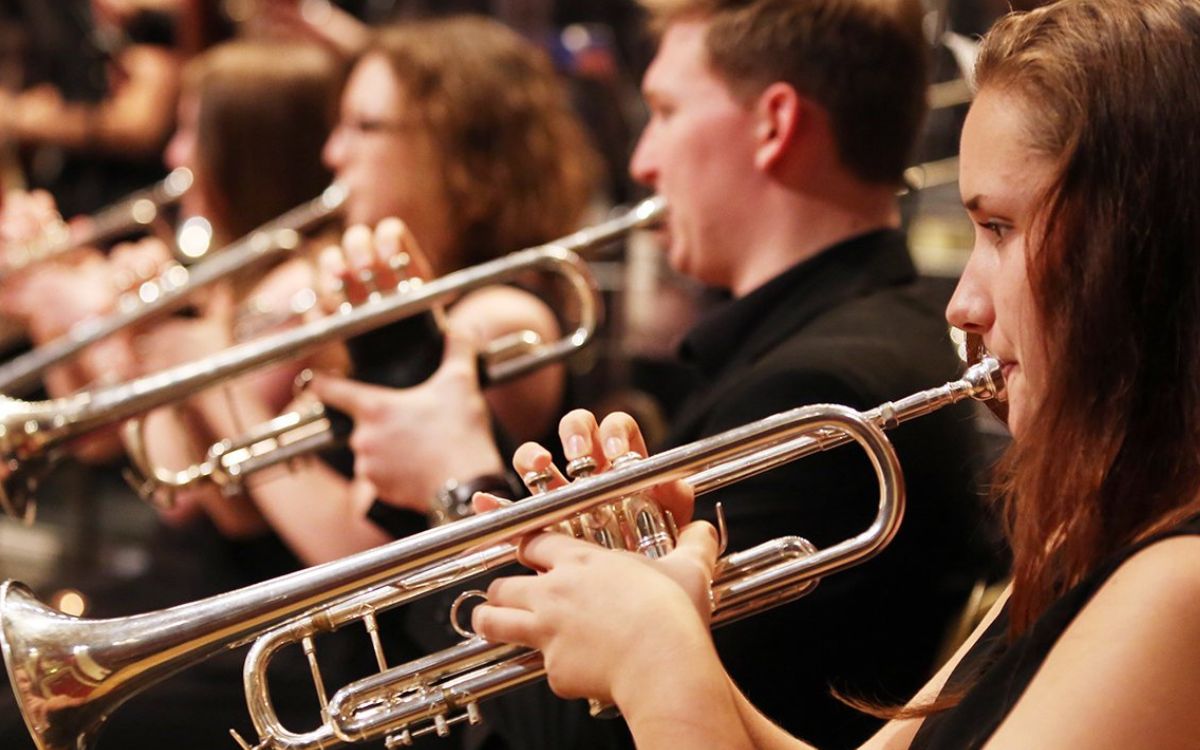
Brass Instruments
What Do You Call A Person That Makes Brass Instruments
Published: January 15, 2024
Looking for a professional who crafts brass instruments? Find out what to call a person skilled in making brass instruments and discover the world of brass craftsmanship.
(Many of the links in this article redirect to a specific reviewed product. Your purchase of these products through affiliate links helps to generate commission for AudioLover.com, at no extra cost. Learn more)
Table of Contents
Introduction
Have you ever wondered who is responsible for crafting those beautiful brass instruments that produce mesmerizing melodies? Well, look no further than the skilled artisans known as brass instrument makers. These individuals possess a deep understanding of the intricate art of instrument-making and play a vital role in the music industry.
Brass instrument makers, also commonly referred to as instrument technicians or luthiers, are highly skilled craftsmen who specialize in creating, repairing, and maintaining brass instruments. They are passionate about their work and have a deep appreciation for the rich history and unique characteristics of each instrument they create.
From trumpets and trombones to tubas and French horns, brass instrument makers have a profound impact on the sound and quality of these iconic instruments. They strive to create instruments that not only look visually stunning but also produce the rich and resonant sound that musicians strive for.
While the role of a brass instrument maker requires technical expertise and precision, it is also a creative and artistic pursuit. These craftsmen have a keen eye for detail and a deep understanding of the materials and techniques required to create instruments that meet the highest standards of quality.
Whether working in large-scale instrument manufacturing companies or operating as independent artisans, brass instrument makers play a crucial role in the music industry. They collaborate with musicians, composers, and fellow craftsmen to create instruments that fulfill the unique needs and preferences of each individual player.
In the following sections, we will explore the skills and qualifications required to become a brass instrument maker, the tools and equipment they utilize, the various types of brass instruments they create, the intricate crafting process involved, quality control measures, as well as the opportunities and career paths available in this fascinating field.
Role of a Brass Instrument Maker
The role of a brass instrument maker is multifaceted and requires a combination of technical skills, craftsmanship, and artistic sensibility. These skilled professionals are responsible for creating, repairing, and maintaining a wide variety of brass instruments. Let’s delve into the different aspects of their role:
- Instrument Creation: A significant part of a brass instrument maker’s job involves creating new instruments from scratch. This process includes selecting the appropriate materials, shaping and assembling the various components, and fine-tuning the instrument to produce the desired sound quality. Each instrument requires careful attention to detail and precise craftsmanship to ensure its playability and tonal characteristics.
- Repair and Restoration: Brass instruments, like any other musical instruments, may experience wear and tear over time. Brass instrument makers are skilled in the art of repairing and restoring these instruments to their optimal condition. They can fix dents, replace damaged parts, and perform adjustments to maintain the instrument’s performance and integrity. Their expertise in troubleshooting and problem-solving is vital in returning instruments to their original glory.
- Customization: Brass instrument makers often work closely with musicians to create custom-made instruments that cater to their unique playing styles and preferences. They take into account the musician’s specific requirements, such as tone, projection, and ergonomic considerations, to design and build instruments that are tailor-made for the individual’s needs. This level of customization allows musicians to have instruments that are truly personalized and optimized for their artistic expression.
- Maintenance and Servicing: Regular maintenance and servicing are crucial for keeping brass instruments in optimal playing condition. Brass instrument makers are responsible for evaluating and diagnosing issues, conducting routine maintenance procedures, and ensuring that all components are functioning properly. This involves tasks such as cleaning, lubricating, and adjusting valves, slides, and other movable parts to ensure optimal performance.
Brass instrument makers serve as vital contributors to the music industry by ensuring that musicians have instruments that meet their artistic needs. Through their craftsmanship, attention to detail, and understanding of the unique properties of brass instruments, they contribute to the creation of instruments that inspire and enhance the musical experience.
Next, let’s take a closer look at the skills and qualifications required to become a successful brass instrument maker.
Skills and Qualifications
Being a brass instrument maker requires a unique combination of technical skills, artistic talent, and a deep understanding of musical instruments. Here are the key skills and qualifications needed to excel in this field:
- Technical Knowledge: To create and repair brass instruments, a solid foundation in technical knowledge is essential. Brass instrument makers should have a thorough understanding of the different types of brass instruments, their components, and how they function. They should be familiar with materials, such as brass, silver, and gold, and their properties, as well as the various construction methods used in instrument making.
- Craftsmanship: Brass instrument making is a highly skilled craft that requires precision and attention to detail. Makers must have exceptional hand-eye coordination, dexterity, and the ability to work with various tools and equipment. They should possess the craftsmanship necessary to shape, solder, and assemble instrument components with precision, while ensuring proper alignment and fit.
- Problem-Solving: Brass instrument makers often encounter challenges when repairing or customizing instruments. The ability to troubleshoot problems and find creative solutions is vital. They must have a keen eye for identifying issues, whether it’s a leaky valve or a misalignment, and the problem-solving skills to rectify them effectively.
- Artistic Sensibility: While technical knowledge is important, a successful brass instrument maker must also possess artistic sensibility. They should have an ear for sound quality and an understanding of the tonal characteristics of different instruments. This helps them in fine-tuning an instrument to produce the desired sound and helps them create uniquely tailored instruments that meet the needs and preferences of individual musicians.
- Patience and Attention to Detail: Creating and repairing brass instruments requires patience and meticulous attention to detail. From soldering small components to aligning valves and slides, every aspect must be executed with precision. Patience is also crucial when working with musicians, as it may take time to understand their specific requirements and translate them into the final instrument design.
- Continuous Learning: The field of brass instrument making is constantly evolving, and it’s essential for brass instrument makers to stay updated with the latest advancements and techniques. They should actively seek opportunities for professional development, whether through workshops, apprenticeships, or networking with other experienced craftsmen.
While formal education in instrument making or a related field can be beneficial, many brass instrument makers acquire their skills through hands-on experience and apprenticeships. However, a passion for music, an eye for detail, and a commitment to craftsmanship are essential qualities that cannot be taught through formal education alone.
Now that we have explored the necessary skills and qualifications, let’s dive into the tools and equipment used by brass instrument makers.
Tools and Equipment Used
Brass instrument makers rely on a variety of specialized tools and equipment to carry out their craft. These tools are designed to facilitate the precise shaping, assembly, and maintenance of brass instruments. Here are some of the key tools and equipment commonly used by brass instrument makers:
- Bench Tools: Brass instrument makers work at dedicated workbenches equipped with a range of essential tools. These include bench vises, mandrels, hammers, and mallets, which are used for shaping and forming metal components. Additionally, files, saws, and rasps are used for refining the shape and contours of the instrument.
- Soldering Tools: Soldering is a crucial aspect of instrument making, and brass instrument makers use specialized tools for this purpose. They typically use propane or butane torches to heat the solder to the appropriate temperature and soldering stations that include temperature control settings. Various types of fluxes and solders, such as silver solder, are used depending on the specific application.
- Measuring and Marking Tools: Accurate measurement is essential in the precise construction of brass instruments. Therefore, brass instrument makers rely on tools such as calipers, rulers, micrometers, and dial indicators to ensure precise measurements. Marking tools like scribes and center punches are used to mark reference points and guide the construction process.
- Finishing Tools: To achieve a polished and professional appearance, brass instrument makers use a variety of finishing tools. These include sandpaper, emery cloths, buffing wheels, and polishing compounds. The goal is to remove any imperfections, scratches, or marks and achieve a smooth and lustrous finish.
- Specialized Machinery: Some brass instrument makers work with specialized machinery to aid in specific tasks. These may include lathes, which are used for turning and drilling metal components, and milling machines for precision milling and shaping of parts. However, many makers still rely on traditional hand tools and craftsmanship for the majority of their work.
In addition to these tools and equipment, brass instrument makers also use a wide variety of materials, such as brass sheets and tubes, soldering materials, lacquers, and finishes, depending on the specific requirements of the instrument’s construction or repair.
Now that we are familiar with the tools and equipment used by brass instrument makers, let’s explore the various types of brass instruments that these skilled craftsmen create.
Types of Brass Instruments
Brass instruments come in a wide variety of shapes and sizes, each with its own unique sound and playing characteristics. Brass instrument makers are proficient in creating and repairing various types of brass instruments. Let’s explore some of the most common types:
- Trumpet: The trumpet is a small, high-pitched instrument with a cylindrical bore and three valves. It is known for its bright and piercing sound and is often found in orchestras, marching bands, and jazz ensembles.
- Trombone: The trombone is a versatile instrument with a long slide and a cylindrical bore. It has a rich and mellow sound and is used in orchestras, brass bands, and jazz settings.
- Tuba: The tuba is the largest and lowest-pitched brass instrument. It has a wide conical bore and produces a deep and resonant sound. Tuba players are found in orchestras, wind ensembles, and brass bands.
- French Horn: The French horn is a conical bore instrument with a coiled shape and a unique sound. It is widely used in orchestras and wind ensembles, adding depth and texture to the overall musical arrangement.
- Cornet: The cornet is similar to the trumpet, but it has a mellower sound and a conical bore. It is often used in brass bands and is sometimes found in orchestras and jazz ensembles.
- Euphonium: The euphonium is a medium-sized brass instrument with a conical bore and a mellower sound. It is commonly found in brass bands, wind ensembles, and orchestras, and often plays a supporting role in the musical arrangement.
- Baritone Horn: The baritone horn is similar to the euphonium in size and shape but has a brighter, more focused sound. It is commonly used in brass bands and marching bands.
These are just a few examples of the diverse range of brass instruments that brass instrument makers are skilled at creating and repairing. Each instrument requires a deep understanding of its specific construction and playing characteristics to ensure optimal sound quality and performance.
Now that we have explored the types of brass instruments, let’s delve into the intricate process involved in crafting these beautiful instruments.
Crafting Process
The crafting process of brass instruments involves a combination of traditional techniques, modern technology, and skilled craftsmanship. Brass instrument makers follow a series of meticulous steps to create instruments that are not only visually appealing but also produce the desired tone and playability.
Here is an overview of the general crafting process followed by brass instrument makers:
- Design and Planning: The process begins with designing the instrument and planning its dimensions, components, and specifications. Factors such as bore size, bell shape, valve placement, and materials are taken into consideration to achieve the desired sound quality and playability.
- Material Selection: Brass instrument makers carefully select the appropriate materials for each instrument. Brass sheets and tubes are commonly used for the main body, while valves and other small components are made of brass or other alloys. Some instruments may incorporate silver or gold plating for added aesthetics and durability.
- Shaping and Forming: The selected materials are shaped and formed using various techniques. Brass sheets are cut and bent to create the instrument’s body, while brass tubing is manipulated to form the various sections, such as the leadpipe, tuning slide, and main slide.
- Joining and Soldering: The different components of the instrument are joined and soldered together to create a cohesive unit. This requires precision and skill in aligning the parts and applying the appropriate amount of heat and solder to achieve strong, secure connections.
- Valve and Slide Assembly: Valves and slides are crucial to the functionality of brass instruments. Brass instrument makers meticulously assemble and fit these components to ensure smooth operation and airtightness. Valves are tested for proper alignment and responsiveness, while slides are carefully adjusted for optimal tuning and slide action.
- Tuning and Voicing: Once the instrument is assembled, brass instrument makers fine-tune it to achieve the desired pitch and tonal characteristics. This involves adjusting the length and position of the tubing, as well as making small modifications to the bell or leadpipe to optimize the instrument’s timbre and response.
- Finishing and Polishing: The final step in the crafting process is the finishing and polishing of the instrument. This includes removing any imperfections, buffing the surfaces to a smooth finish, and applying lacquer or finish coats to protect the instrument and enhance its appearance.
Throughout the crafting process, brass instrument makers exercise patience, attention to detail, and expertise to ensure that every instrument meets the highest standards of quality. Each instrument is meticulously crafted to not only produce beautiful melodies but also to provide a comfortable and enjoyable playing experience for musicians.
Now that we have explored the crafting process, let’s turn our attention to the quality control measures and testing that brass instruments undergo before they reach the hands of musicians.
Quality Control and Testing
Quality control is a critical aspect of the brass instrument-making process. Brass instrument makers implement rigorous measures to ensure that each instrument meets the highest standards of craftsmanship, playability, and sound quality. Let’s delve into the key components of quality control and testing in brass instrument making:
- Visual Inspection: Brass instrument makers carefully examine each instrument for any visual imperfections, such as dents, scratches, or inconsistencies in the finish. They ensure that the instrument’s overall appearance is aesthetically pleasing and free from any defects that may affect its performance or longevity.
- Playability Testing: Every instrument must undergo rigorous playability testing to ensure its responsiveness and sound quality. Brass instrument makers play the instrument themselves or collaborate with skilled musicians to assess its tonal characteristics, intonation, and overall playability. This stage allows for fine-tuning adjustments to achieve the desired sound and response.
- Air Tightness Testing: Brass instruments rely on airtight seals and properly functioning valves and slides. During the quality control process, makers check the instrument’s airtightness by performing tests such as air leakage detection and seal testing. This ensures that the instrument functions as intended and does not have any air leakage that may affect its sound production.
- Intonation Verification: Brass instrument makers verify the intonation of the instrument to ensure that it produces accurate pitches across different registers. This involves testing the instrument’s tuning with the use of electronic tuners or by playing specific scales and intervals to assess the accuracy of the notes produced. Adjustments are made if necessary to achieve optimal intonation.
- Mechanical Operation Testing: Valve and slide action are crucial to the playability of brass instruments. Brass instrument makers test the mechanical operations of valves and slides to ensure smoothness, responsiveness, and precision. They ensure that valves move freely and silently, and that slides glide easily while maintaining a proper seal.
- Endurance and Durability Testing: Instruments are subjected to endurance and durability tests to assess their ability to withstand the demands of regular playing. This includes evaluating the strength and stability of the instrument’s joints, assessing the reliability of valve mechanisms, and verifying the durability of slide movements.
- Sound Testing: Sound quality is of paramount importance in brass instruments. Brass instrument makers meticulously evaluate the tonal characteristics, projection, and resonance of each instrument. They listen for any discrepancies or abnormalities in the sound and make necessary adjustments to ensure a clear, vibrant, and balanced tone.
By implementing thorough quality control measures and testing procedures, brass instrument makers ensure that every instrument that leaves their workshop meets the highest standards of craftsmanship and performance. This dedication to quality not only satisfies the needs of musicians but also upholds the reputation of the maker.
Now let’s explore the importance of maintenance and repair in preserving the integrity and longevity of brass instruments.
Maintenance and Repair
Maintenance and repair are essential aspects of preserving the performance, longevity, and value of brass instruments. Brass instrument makers play a significant role in providing maintenance services and carrying out repairs to ensure that these instruments continue to function optimally. Let’s delve into the importance of maintenance and repair in the world of brass instruments:
Maintenance:
Maintaining a brass instrument involves regular care and attention to ensure its optimal performance. Here are some key maintenance practices that brass instrument makers and musicians undertake:
- Cleaning: Regular cleaning is essential to remove dirt, oils, and debris that accumulate over time. Brass instrument makers guide musicians on proper cleaning techniques and suggest appropriate cleaning agents to avoid damaging the instrument’s finish or internal components.
- Lubrication: Brass instruments have various movable parts, such as valves and slides, that require lubrication to function smoothly. Brass instrument makers recommend the use of suitable lubricants and guide musicians on the proper application to maintain optimal action and prevent friction-related issues.
- Inspections: Routine inspections help identify any signs of wear and tear or potential problems before they worsen. Brass instrument makers carefully examine the instrument for issues such as valve alignment, slide movement, and structural integrity. Early detection of problems allows for prompt repair and avoids further damage.
- Tuning and Adjustments: Over time, brass instruments may require tuning or adjustments to maintain proper intonation and playability. Brass instrument makers possess the expertise to fine-tune the instrument, adjust valve and slide mechanisms, and make necessary adjustments to ensure optimal performance.
Repair:
Despite meticulous maintenance, brass instruments may encounter issues that require professional repair. Brass instrument makers play a critical role in diagnosing and addressing these problems to restore the instrument’s functionality. Common repair services provided by brass instrument makers include:
- Dent Removal: Dents can occur from accidental impacts or mishandling, affecting the instrument’s playability and sound quality. Brass instrument makers possess specialized tools and techniques to carefully remove dents without compromising the instrument’s structural integrity.
- Valve and Slide Repair: Valves and slides may experience wear and tear over time or become misaligned, affecting the instrument’s playability. Brass instrument makers can disassemble, clean, repair, or replace these components as needed to restore optimal performance.
- Leak and Seal Repair: Leaks in the joints, tubing, or valve casings can affect the instrument’s airtightness and sound production. Brass instrument makers employ various techniques to locate and repair these leaks, ensuring the instrument functions as intended.
- Tonal Adjustment: Over time, the tonal characteristics of an instrument may change due to factors such as wear, damage, or changes in the instrument’s structural integrity. Brass instrument makers possess the expertise to assess and adjust the instrument’s tonal characteristics, bringing it back to its optimal sound quality.
By providing maintenance services and expert repairs, brass instrument makers contribute to the preservation and extended lifespan of these beloved instruments. Their skills and knowledge ensure that musicians can continue to create beautiful music with instruments that are in pristine condition.
Now, let’s explore the career opportunities available in the field of brass instrument making.
Career Opportunities
For those passionate about brass instruments and skilled in the art of instrument making, a variety of career opportunities await in the field of brass instrument making. Let’s explore some of the avenues where brass instrument makers can find fulfilling careers:
- Instrument Manufacturing Companies: Many brass instrument makers find employment in large-scale instrument manufacturing companies. These companies produce a wide range of brass instruments for musicians worldwide. Working in such companies allows brass instrument makers to be part of a larger production process and collaborate with teams of skilled craftsmen to create high-quality instruments.
- Independent Instrument Shops: Some brass instrument makers prefer to operate their own independent instrument shops. These shops offer personalized instrument-making services, repairs, and maintenance to musicians. It provides creative freedom and the opportunity to work directly with musicians, catering to their unique needs and preferences.
- Custom Instrument Making: Brass instrument makers with exceptional craftsmanship and a reputation for excellence may specialize in creating custom-made instruments. These instruments are tailored to the specific requirements and playing styles of individual musicians. Custom instrument making allows for artistic expression and the satisfaction of crafting unique instruments that perfectly match the musician’s vision.
- Repair and Restoration Services: Repair and restoration services are in high demand in the world of brass instruments. Brass instrument makers can establish themselves as experts in repairing and restoring brass instruments, catering to musicians, music stores, and orchestras. This work allows them to utilize their skills in diagnosing and addressing instrument issues, while breathing new life into older or damaged instruments.
- Instrument Technician or Luthier: Some brass instrument makers specialize in instrument maintenance and servicing. They work as instrument technicians or luthiers, providing regular maintenance, adjustments, and repairs to brass instruments. These professionals play a vital role in ensuring that instruments are in optimal playing condition and helping musicians achieve their best performance.
- Teaching and Education: Experienced brass instrument makers may choose to share their knowledge and skills by becoming teachers or educators. They can teach instrument making and repair techniques at vocational schools, colleges, or workshops, passing on their expertise to aspiring instrument makers and technicians.
These are just a few examples of the diverse career opportunities available in the field of brass instrument making. The field offers a blend of creativity, technical proficiency, and a deep appreciation for the world of music. Whether working in large manufacturing companies, running independent shops, or specializing in custom instrument making, brass instrument makers contribute significantly to the music industry by creating and maintaining instruments that inspire musicians and enhance their musical experiences.
Now, let’s wrap up the article with a summary of the key points we’ve covered.
Conclusion
Brass instrument makers are passionate artisans who play a vital role in the creation, repair, and maintenance of brass instruments. Their expertise in crafting instruments with precision and care allows musicians to bring magical melodies to life. Throughout this article, we have explored the various aspects of the brass instrument maker’s role, from the skills and qualifications required to the intricate crafting process involved.
We learned that brass instrument makers possess a combination of technical knowledge, craftsmanship, problem-solving skills, and artistic sensibility. They work with a wide range of tools and equipment to shape, assemble, and fine-tune instruments to produce the desired tonal characteristics. Quality control and testing ensure that every instrument meets the highest standards of craftsmanship and performance.
Maintenance and repair services provided by brass instrument makers are essential in preserving the integrity and longevity of these instruments. They ensure that instruments remain in optimal playing condition, allowing musicians to continue creating beautiful music. Brass instrument makers can pursue various career opportunities, whether in instrument manufacturing companies, independent instrument shops, custom instrument making, repair and restoration services, or teaching and education.
Brass instrument makers are the unsung heroes behind the scenes, contributing their skills and expertise to the rich soundscape of music. Their dedication and craftsmanship ensure that brass instruments continue to captivate audiences and inspire musicians for generations to come.
So, the next time you are enchanted by the beautiful sound of a trumpet, trombone, or tuba, remember the skilled hands and hearts of brass instrument makers who make it all possible.