Home>Production & Technology>Vinyl>How Is Music Stored On A Vinyl Record
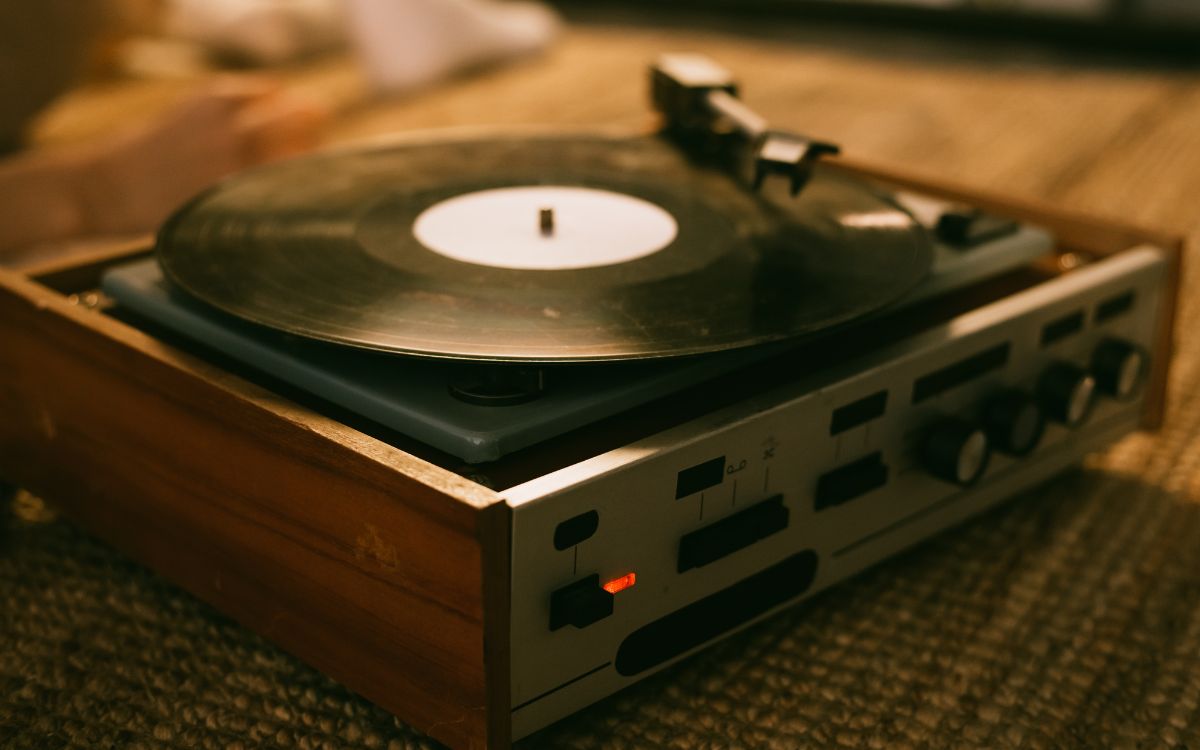
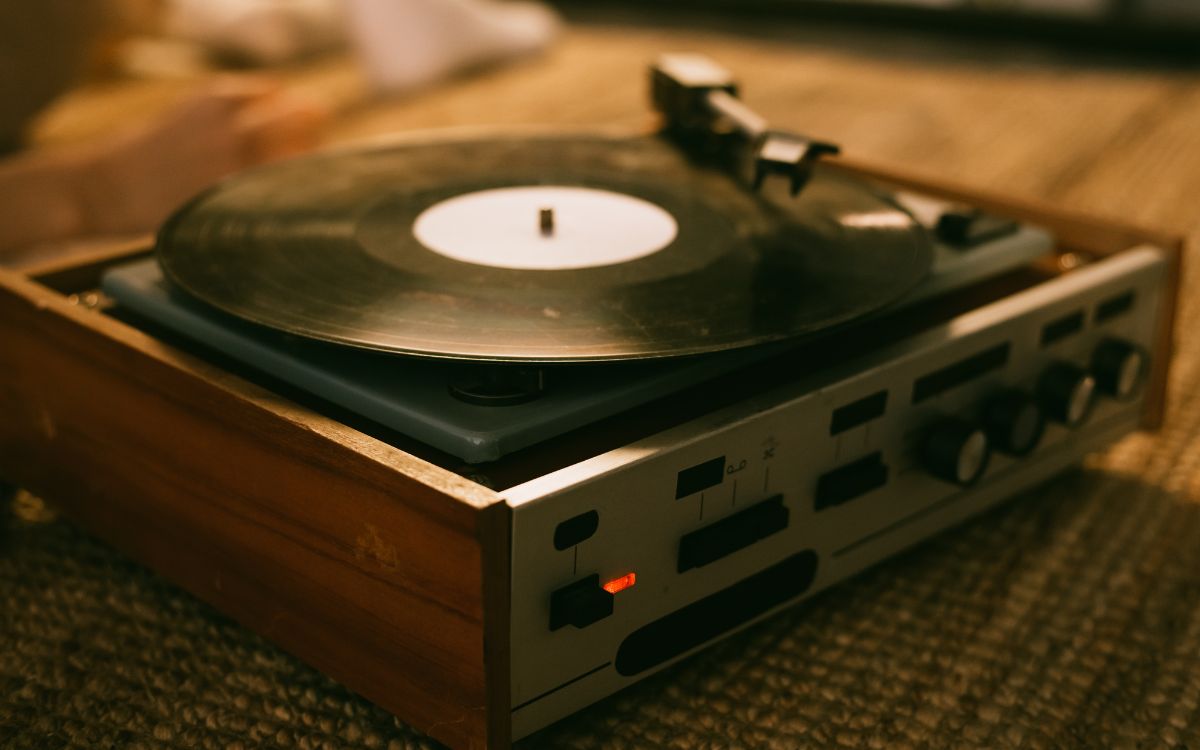
Vinyl
How Is Music Stored On A Vinyl Record
Modified: January 22, 2024
Discover the magic of vinyl records and how music is stored on them. Explore the unique way that vinyl captures and preserves sound.
(Many of the links in this article redirect to a specific reviewed product. Your purchase of these products through affiliate links helps to generate commission for AudioLover.com, at no extra cost. Learn more)
Table of Contents
Introduction
With the rise of digital music platforms and streaming services, it’s easy to forget the rich history and unique charm of vinyl records. Vinyl records have been a staple in the music industry for decades, captivating listeners with their warm sound, large artwork, and nostalgic appeal. But have you ever wondered how music is stored on a vinyl record? In this article, we will delve into the fascinating world of vinyl records and explore the physical structure, the role of the groove, and how sound waves are translated into grooves.
Vinyl records, also known as phonograph records or simply “records,” were introduced in the late 19th century and became the primary medium for music consumption until the rise of cassette tapes and CDs in the late 20th century. Despite the advancements in digital technology, vinyl records have experienced a resurgence in recent years, gaining a dedicated following of audiophiles and music enthusiasts.
The physical structure of a vinyl record consists of a flat disc made from polyvinyl chloride (PVC). The disc is typically 12 inches in diameter and has a small center hole that fits onto a turntable’s spindle. The two sides of the record are referred to as Side A and Side B, each containing a different set of tracks.
The key to music storage on a vinyl record lies in the groove. The groove is the spiral track that runs from the outer edge of the record to the center. It is within these grooves that the audio information is physically stored. But how does this work? How are sound waves translated into these grooves? To understand this process, we need to explore the role of the turntable and the needle, also known as a stylus, in extracting the audio information from the grooves.
The Physical Structure of a Vinyl Record
To truly understand how music is stored on a vinyl record, it’s important to have a basic understanding of its physical structure. A vinyl record consists of a circular disc made from polyvinyl chloride (PVC), a durable and flexible material. The standard size for a vinyl record is 12 inches in diameter, although there are smaller versions such as 7-inch singles and larger formats like 10-inch records. The thickness of the record can vary, but it is typically around 1.5 to 2 millimeters.
The vinyl disc is divided into two sides, commonly referred to as Side A and Side B. Each side contains a different set of tracks or songs. The sides are labeled with numbers or letters to indicate their sequence. Side A is typically the first side played when the record is placed on a turntable, while Side B is flipped over and played after Side A is finished.
In the center of the vinyl record, there is a small hole known as the spindle hole. This allows the record to be placed and secured onto the spindle of a turntable. The spindle is connected to the turntable’s motor, which rotates the record at a precise speed. The most common rotational speeds for vinyl records are 33 1/3 revolutions per minute (RPM) for full-length albums and 45 RPM for singles. There are also less common speeds such as 78 RPM used for early shellac records.
The surface of the record is divided into concentric circles, and within these circles lies the all-important groove. The groove is a spiral track that starts at the outer edge of the record and winds its way towards the center. It is within this narrow, undulating groove that the audio information is stored.
The outer edge of the record is typically the widest part and contains the first track or song of Side A. As the groove spirals inward, it gradually becomes narrower, which allows for more music to be stored on the record. The innermost part of the groove is where the last track of Side B is found.
In addition to the audio information, vinyl records often feature artwork and information printed on the record labels and album covers. These visuals add to the aesthetic appeal of vinyl and provide additional context and enjoyment for the listener.
Now that we have a clear understanding of the physical structure of a vinyl record, let’s explore the role of the groove and how it plays a vital role in storing music.
The Groove and its Role in Music Storage
The groove is at the heart of a vinyl record’s ability to store music. It is a spiral track that runs from the outer edge of the record to the center, and it is within these grooves that the audio information is physically stored. The groove contains a series of bumps and pits that represent the sound waves of the recorded music.
When a vinyl record is played on a turntable, a stylus or needle, connected to a tonearm, is placed in the groove. As the record rotates, the stylus moves along the groove, tracing the contours of the bumps and pits. The stylus is designed to vibrate as it encounters these variations in the groove, and these vibrations are then translated into electrical signals.
The depth and width of the groove play a crucial role in the storage of music. The width of the groove determines the range of frequencies that can be reproduced, with narrower grooves capable of storing higher frequencies. The depth of the groove represents the amplitude of the sound, dictating the volume or loudness of the music.
During the mastering process, the audio engineer carefully cuts the grooves into the lacquer or metal master disc using a lathe. The artist’s recorded music is converted into an analog signal, and the engineer uses various techniques to optimize the sound for vinyl playback. This includes adjusting the volume levels, equalization, and spacing between the grooves to ensure optimal sound quality.
It is important to note that the playing time of a vinyl record is limited by the amount of space available within the grooves. As the music plays, the stylus moves towards the center of the record, and the grooves become narrower. This reduction in groove space restricts the playing time, especially for records with longer tracks or albums with a large number of songs.
The groove is responsible for the unique sound characteristics of vinyl records. The physical nature of the groove and the playback process contribute to the warm and rich quality often associated with vinyl. The imperfections and nuances in the groove can add a certain depth and texture to the sound, creating a distinct listening experience.
Now that we have explored the role of the groove in music storage, let’s take a closer look at how sound waves are translated into the grooves on a vinyl record.
How Sound Waves are Translated into Grooves
One of the wonders of vinyl records lies in the process by which sound waves are translated into grooves. It involves a combination of physics, engineering, and craftsmanship to transform the audio recording into a physical representation.
When sound is recorded, it is converted into electrical signals representing the varying amplitude and frequency of the audio. These electrical signals are then fed into a cutting lathe during the mastering process. The cutting lathe contains a cutting head that consists of a heated stylus and a sharp diamond tip.
As the electrical signal is fed into the cutting head, it heats up the stylus, making it malleable. When the stylus comes into contact with the lacquer or metal master disc, it begins to vibrate rapidly. These vibrations are determined by the electrical signal and correspond to the varying amplitude and frequency of the audio.
The vibrating stylus cuts grooves into the master disc, shaped according to the audio signal. The variations in the electrical signal cause the stylus to move side-to-side and up-and-down, creating the undulating grooves that represent the sound waves.
During this process, the depth and width of the groove are carefully controlled. The amplitude of the audio signal determines the depth of the groove, while the frequency of the audio signal influences the width of the groove. By manipulating these factors, audio engineers can optimize the storage of the music on the record.
It is worth noting that the process of cutting grooves on a vinyl record is an intricate and delicate task. The mastering engineer must carefully balance the depth and width of the grooves to ensure optimal playback quality. If the grooves are cut too shallow, the stylus may skip or jump, leading to a disrupted listening experience. On the other hand, if the grooves are cut too deep, it can lead to distortion or damage to the record during playback.
Once the grooves are cut into the master disc, it goes through several stages of production to create the final vinyl record. This includes the creation of metal stampers used for mass production and the pressing of vinyl discs with the grooves imprinted on them.
When a vinyl record is played, the stylus of the turntable’s cartridge is placed in the groove and is guided through the undulations. As the stylus moves along the grooves, it vibrates, producing electrical signals that are then amplified and sent to speakers, resulting in the reproduction of the recorded music.
Understanding the process of how sound waves are translated into grooves provides a deeper appreciation for the art and craftsmanship involved in creating vinyl records. It also showcases why vinyl records offer a unique and captivating listening experience, where music is not just stored digitally but etched physically.
Next, let’s explore the role of mastering and the manufacturing process in ensuring the quality of the final vinyl record.
The Role of Mastering and the Manufacturing Process
The process of creating a vinyl record involves not only the cutting of grooves but also the crucial steps of mastering and manufacturing. These stages play a vital role in ensuring the quality and fidelity of the final product.
Mastering is the final stage in the audio production process before the music is transferred to a vinyl record. It involves a skilled audio engineer, known as a mastering engineer, who carefully prepares the audio recordings for optimal playback on vinyl.
During mastering, a variety of adjustments are made to the audio signals to ensure they translate accurately to the grooves. The engineer works with the original recordings, adjusting the volume levels, applying equalization to balance the frequencies, and making any necessary edits or enhancements. This process ensures that the music sounds its best when played back on a vinyl record.
Another crucial aspect of the manufacturing process is the creation of metal stampers. Metal stampers are produced from the original lacquer master disc and are used to press vinyl records. The stampers hold the negative impression of the grooves and are responsible for transferring the audio information onto the vinyl discs during pressing.
Once the metal stampers are created, the manufacturing process continues with the pressing of vinyl records. Vinyl pellets are molded and heated, then placed between the stampers. As pressure is applied, the grooves on the stampers impress onto the vinyl, creating the familiar spiral tracks. The vinyl is then allowed to cool, resulting in a solid record.
Quality control is a critical component of the manufacturing process. Vinyl records undergo strict inspection to detect any defects, such as surface imperfections, warping, or debris. Records that pass the quality control checks are then packaged, often in protective sleeves and album jackets, ready for distribution.
The role of mastering and the manufacturing process is essential in ensuring the final vinyl records meet the highest standards of sound quality and durability. Skilled mastering engineers bring out the full potential of the music, optimizing it for the unique characteristics of vinyl playback. The meticulous manufacturing process ensures that each vinyl record is a faithful representation of the audio and can withstand repeated plays without degradation.
As a result of these careful processes, vinyl records offer a level of attention to detail and craftsmanship that digital media often struggle to replicate. They provide a tangible and immersive experience for music lovers, capturing the essence of the music and the artistry involved in its creation.
Now that we understand the role of mastering and the manufacturing process, let’s explore the factors that can affect the sound quality of vinyl records.
Factors Affecting Sound Quality on Vinyl Records
The sound quality of vinyl records is influenced by various factors that can greatly impact the listening experience. These factors include the mastering process, vinyl quality, pressing techniques, and playback equipment. Let’s delve into each of these factors in more detail:
1. Mastering: The quality of the audio mastering has a significant impact on how the music translates onto vinyl. A well-mastered record will have balanced frequency response, proper dynamics, and appropriate spacing between the grooves. A skilled mastering engineer ensures that the music is optimized for vinyl playback, resulting in a faithful, detailed, and enjoyable listening experience.
2. Vinyl Quality: The quality of the vinyl used for pressing records is crucial. Higher-quality vinyl formulations with a lower noise floor and better durability will result in improved sound quality. Vinyl records made from virgin vinyl, as opposed to recycled vinyl, tend to offer better audio reproduction. Additionally, the thickness of the vinyl can affect the overall sound and durability, with thicker records often exhibiting better bass response and resistance to warping.
3. Pressing Techniques: The pressing process plays a critical role in determining the sound quality of a vinyl record. Factors such as the temperature and duration of the pressing, the quality of the stampers, and the cleanliness of the pressing machines can all impact the final product. Neglecting these factors can lead to issues like surface noise, distortion, and inconsistencies in the audio playback.
4. Vinyl Care and Handling: Proper care and handling of vinyl records are essential for maintaining sound quality. Dust, dirt, and scratches can all degrade the audio performance, causing pops, crackles, and skips. Regular cleaning and proper storage in protective sleeves can help preserve the condition of the record and ensure optimal sound quality over time.
5. Playback Equipment: The quality and condition of the turntable, cartridge, stylus, and other playback equipment directly impact how well a vinyl record sounds. High-quality turntables with well-aligned tonearms and precisely calibrated cartridges can extract the best possible audio from the grooves. Additionally, regular maintenance and replacement of worn-out styluses are necessary to achieve optimal sound reproduction.
6. Environment and Acoustics: The listening environment and acoustics of the room can affect the sound quality of vinyl records. Factors like room reflections, background noise, and speaker placement can all impact the perceived audio quality. Creating an optimized listening environment with proper speaker placement, acoustic treatment, and minimal background noise can enhance the overall sound experience.
By considering these factors, vinyl enthusiasts can ensure that they are getting the most out of their records. Investing in high-quality mastering, vinyl, and playback equipment, coupled with proper care and an optimized listening environment, can result in a truly immersive and satisfying vinyl listening experience.
Now that we understand the factors that can affect sound quality on vinyl records, let’s explore some tips for vinyl record care and maintenance.
Vinyl Record Care and Maintenance
Proper care and maintenance are essential for preserving the sound quality and longevity of vinyl records. By following a few simple steps, you can ensure that your vinyl collection remains in optimal condition for years to come:
1. Handling: Always handle records with clean hands and avoid touching the playing surface. Hold records by their edges or by placing your fingers in the center label area, taking care not to bend or put pressure on the vinyl.
2. Cleaning: Regularly clean your records to remove dust, dirt, and other contaminants that can impact sound quality. Use a microfiber brush or a carbon fiber brush to gently sweep away surface particles. For more thorough cleaning, consider using a record cleaning solution and a soft brush or a record cleaning machine for deep cleaning.
3. Storage: Store vinyl records upright in a vertical position to prevent warping. Use sturdy, acid-free inner sleeves to protect the record surface from scratches. Keep records in a cool and dry environment, away from direct sunlight and extreme temperature fluctuations.
4. Sleeve Protection: Keep records in their original album jackets or invest in protective outer sleeves. These sleeves not only shield the cover artwork from wear and tear but also provide an extra layer of protection against dust, moisture, and other potential damage.
5. Needle Care: Regularly inspect and clean the stylus of your turntable’s cartridge. Use a stylus brush to remove debris and dust. If the stylus is worn or damaged, it should be replaced promptly to prevent further damage to your records.
6. Turntable Setup: Ensure your turntable is properly set up, with a properly aligned cartridge and correct tracking force. Incorrect setup can result in unnecessary wear on your records and compromised sound quality.
7. Avoid Extremes: Keep records away from extreme temperatures, high humidity, and exposure to direct sunlight. Vinyl records are sensitive to heat and can warp under extreme conditions. Excessive humidity can also cause mold and mildew to develop on the record surface.
8. Playback Care: Be gentle when placing and removing the stylus from the record surface. Abrupt movements or mishandling can cause scratches or groove damage. Avoid repeated playbacks in quick succession, as this can generate additional heat and potentially damage the vinyl.
9. Rotation: Regularly rotate records in your collection and give them a rest between plays to prevent excessive wear. Overplaying the same record repeatedly can lead to groove wear, affecting sound quality over time.
By following these care and maintenance practices, you can ensure that your vinyl records remain in excellent condition, preserving their sound quality and extending their lifespan for many years of enjoyable listening.
Now that we have covered vinyl record care and maintenance, let’s summarize what we’ve learned.
Conclusion
Vinyl records have a rich history and unique charm that continues to captivate music enthusiasts. Understanding how music is stored on vinyl enhances our appreciation for the art and craftsmanship involved in the vinyl record production process.
From the physical structure of a vinyl record to the role of the groove in music storage, each element contributes to the overall experience. The mastering process ensures that the audio is optimized for vinyl playback, while the quality of the vinyl and the pressing techniques play a crucial role in sound reproduction.
Caring for vinyl records is also essential for maintaining their sound quality and longevity. Proper handling, cleaning, storage, and maintenance practices all contribute to preserving the integrity of the records and ensuring a pristine audio experience with each playback.
Vinyl offers a unique and tactile listening experience, with its warm sound, expansive artwork, and nostalgic appeal. By investing in a high-quality turntable, cartridge, and other playback equipment, along with a carefully curated vinyl collection, you can truly immerse yourself in the rich world of vinyl records.
Whether you’re a seasoned vinyl enthusiast or new to the format, exploring the intricacies of vinyl record storage and music reproduction adds a deeper level of understanding and enjoyment to the hobby. So, dust off your favorite records, put them on the turntable, and let the warm sound of vinyl transport you to a bygone era.
As technology continues to advance, vinyl records remain a testament to the enduring allure of physical media and the unique connection it fosters between the listener and the music. So, embrace the crackles, pops, and imperfections that make vinyl records truly special, and enjoy the magic of music stored on a vinyl record.