Home>Instruments>Brass Instruments>Of What Material Are Brass Instruments Made?
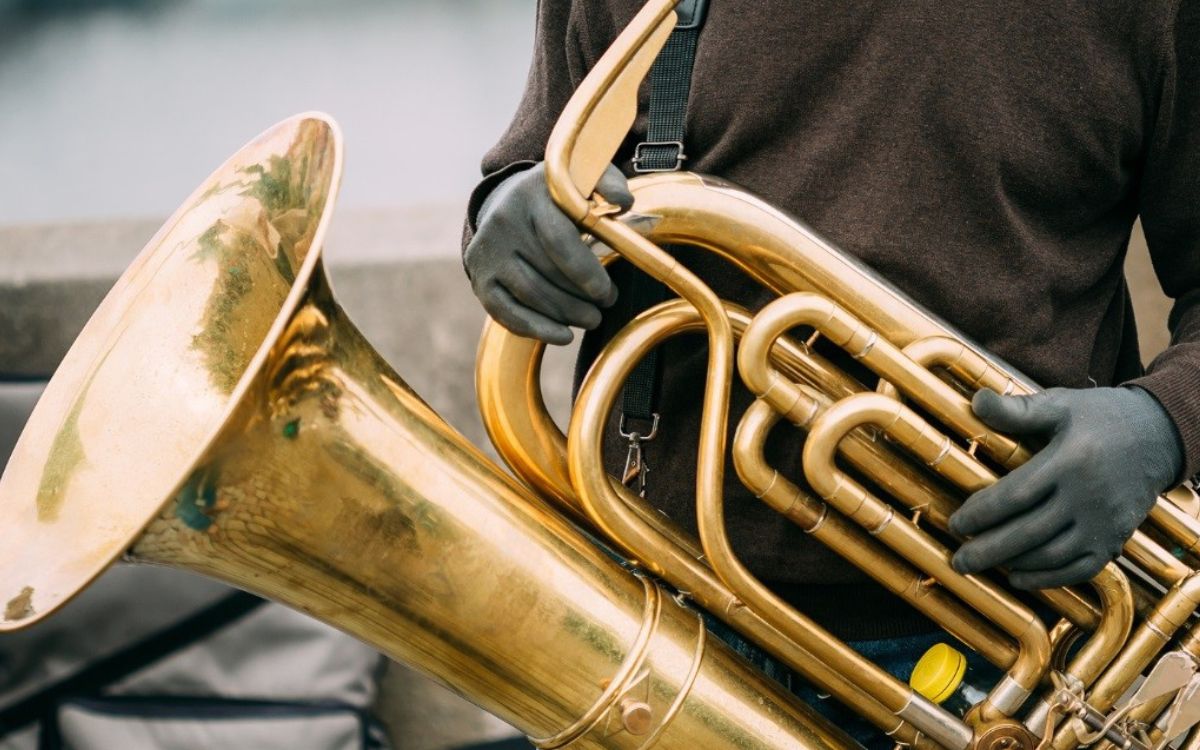
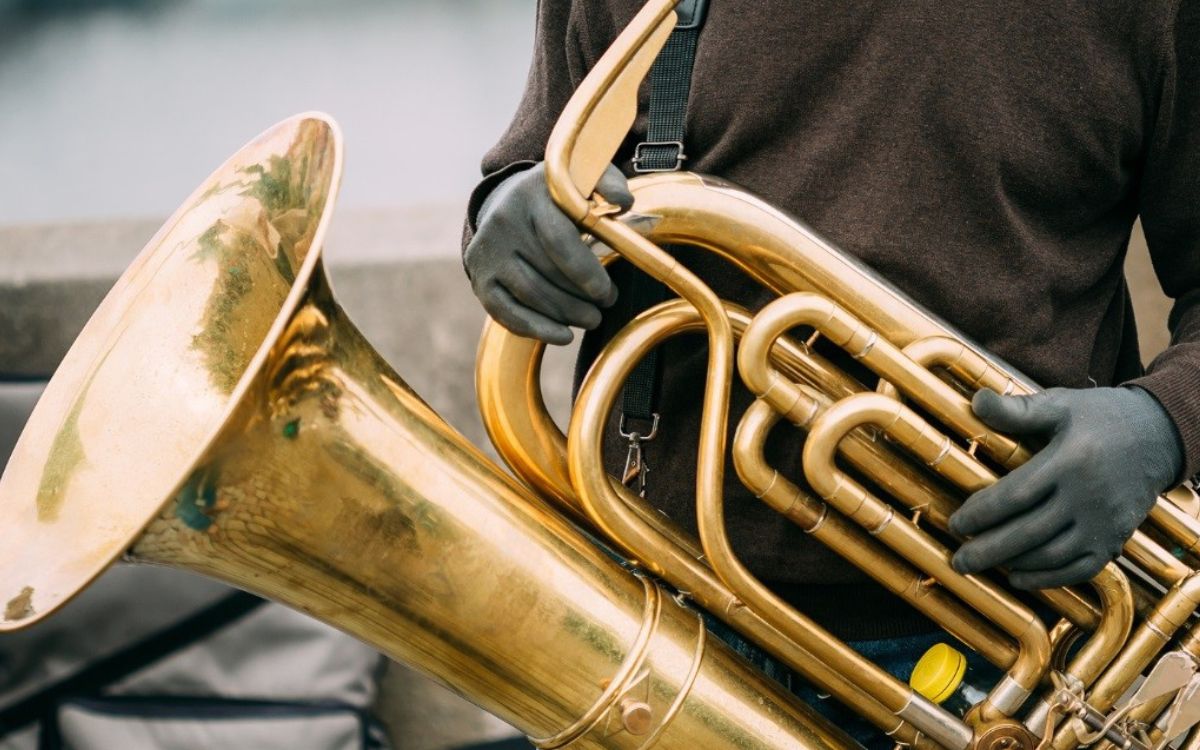
Brass Instruments
Of What Material Are Brass Instruments Made?
Published: January 15, 2024
Find out what material brass instruments are made of and learn more about the construction of these popular musical instruments.
(Many of the links in this article redirect to a specific reviewed product. Your purchase of these products through affiliate links helps to generate commission for AudioLover.com, at no extra cost. Learn more)
Table of Contents
Introduction
Welcome to the fascinating world of brass instruments! From the regal sound of a trumpet to the soul-stirring melodies of a saxophone, brass instruments have been captivating audiences for centuries. Whether you’re a musician, a music enthusiast, or simply curious about the impressive range of sounds produced by these instruments, this article will provide you with a comprehensive overview of the materials used in the construction of brass instruments.
Brass instruments belong to a family of musical instruments that are characterized by their unique sound production through the vibration of the player’s lips against a cup-shaped mouthpiece. These instruments are not only capable of producing majestic and powerful tones, but they also offer a wide range of expressive possibilities.
In order to understand the materials used in the construction of brass instruments, it is important to delve into their rich history. The origins of brass instruments can be traced back to ancient civilizations, where rudimentary versions of these instruments were made from bone, wood, and other natural materials. However, it was the advent of metallurgy that revolutionized the construction of brass instruments, allowing for the development of more refined and sophisticated designs.
Today, brass instruments are primarily made from a specific alloy known as brass. Brass is an alloy consisting primarily of copper and zinc, with varying proportions of each metal depending on the desired characteristics of the instrument. This blend of metals gives brass instruments their distinctive tone, resonance, and durability.
Most brass instruments, such as trumpets, trombones, and French horns, are traditionally made from yellow brass, which is a blend of approximately 70% copper and 30% zinc. This combination produces a bright and vibrant sound, making it the preferred choice for many musicians.
However, there are also brass instruments that incorporate different alloys to achieve specific tonal qualities. For instance, the silver-plated brass used in some trumpets adds a touch of elegance and enhances the instrument’s projection and clarity. Additionally, some manufacturers experiment with other alloys, such as rose brass or gold brass, to create instruments with a warmer and mellower sound.
In the following sections, we will explore the properties of brass, the different types of brass alloys used in instrument making, and the manufacturing process involved in crafting these remarkable musical instruments. We will also discuss the importance of caring for and maintaining brass instruments to ensure their longevity and optimal performance. So, let’s dive in and unravel the secrets behind the captivating world of brass instruments and their materials!
Overview of Brass Instruments
Brass instruments are a diverse group of musical instruments known for their characteristic warm and vibrant sound. They are classified as aerophones, as they produce sound by vibrating air through the player’s lips, which are pressed against a mouthpiece. The design of these instruments allows players to control the pitch, volume, and timbre of the sound.
Brass instruments are typically made up of three main components: the mouthpiece, the tubing, and the bell. The mouthpiece is a cup-shaped metal piece that the player blows into, creating the initial sound. The tubing, which is usually coiled in a specific shape, acts as a resonator and determines the pitch. The bell, at the end of the tubing, amplifies and projects the sound.
There are various types of brass instruments, each with its own distinctive sound and playing technique. The trumpet, for example, is known for its bright and piercing sound, and it is commonly used in classical, jazz, and popular music genres. The trombone, on the other hand, has a rich and mellow tone and possesses a unique slide mechanism that allows for smooth glissandos and expressive playing.
The French horn, also called the horn, has a cylindrical shape and is known for its round and warm sound. It is a versatile instrument that is featured in orchestras, brass bands, and chamber ensembles. The tuba, with its deep and powerful sound, is the largest and lowest-pitched member of the brass family. It provides the foundation and reinforces the harmony in various musical genres, including classical, marching band, and jazz music.
Other brass instruments include the cornet, flugelhorn, baritone horn, and euphonium, each with its own unique characteristics and role in different musical contexts. These instruments cover a wide range of musical styles and genres, from classical and orchestral music to jazz, pop, and even rock.
Brass instruments are not only renowned for their distinctive sound but also for their versatility. They can produce a wide spectrum of tones, from soft and mellow to loud and powerful, allowing musicians to express a range of emotions and musical ideas. They are also highly versatile in terms of playing techniques, with musicians employing various methods such as lip slurs, tonguing, vibrato, and articulation to create different effects and colors in their playing.
Due to their impressive range and expressive capabilities, brass instruments play a crucial role in ensemble music, orchestras, marching bands, jazz bands, and various other musical settings. Whether performing solo or as part of an ensemble, brass instruments add depth, richness, and excitement to the overall musical experience.
History of Brass Instruments
The history of brass instruments spans thousands of years, with evidence of rudimentary brass instruments dating back to ancient civilizations. The earliest known brass instruments were constructed from natural materials such as animal horns, conch shells, and bones. These early instruments were simple tubes with a mouthpiece and were played by buzzing the lips.
It was not until the development of metallurgy that brass instruments as we know them today started to take shape. The discovery and refinement of copper and zinc alloys led to the creation of brass, which became the preferred material for constructing these instruments due to its durability, resonance, and malleability.
During the Middle Ages and the Renaissance, brass instruments were primarily used in military contexts and ceremonial music. They were often associated with nobility and played a significant role in heraldic ceremonies and processions. Trumpets and horns were the most commonly used brass instruments during this period.
In the 17th and 18th centuries, brass instruments began to feature prominently in orchestral music. This was a time of great innovation and experimentation, with instrument makers continuously refining the design and construction of brass instruments to improve their sound and playability.
One of the most significant developments during this period was the invention of valves, which revolutionized brass instrument playing. The trumpet, for example, was transformed from a limited instrument with only natural harmonics to a fully chromatic instrument capable of playing any pitch with the addition of valves.
As brass instruments evolved, they gained popularity in various genres of music. In the 19th century, brass bands became a prominent feature of cultural and civic life, providing entertainment in parks, for parades, and at social events. The versatility and power of brass instruments also made them indispensable in orchestral settings, allowing composers to explore new sonic possibilities in their compositions.
The emergence of jazz music in the early 20th century brought another wave of innovation to brass instruments. Musicians such as Louis Armstrong and Bix Beiderbecke pioneered new playing techniques, infusing their performances with improvisation, syncopation, and expressive techniques like vibrato and growling.
Today, brass instruments continue to play an essential role in a wide range of musical genres, including classical, jazz, pop, rock, and world music. Instrument makers and musicians continue to push the boundaries of what can be achieved with these instruments, exploring new sounds, extended techniques, and innovative playing styles.
The evolution of brass instruments throughout history has showcased the ingenuity and creativity of musicians and instrument makers alike. These instruments have left an indelible mark on the world of music, captivating listeners with their powerful and expressive sound.
Materials Used in Brass Instruments
Brass instruments, as the name suggests, are predominantly made from a specific alloy called brass. Brass is a metallic alloy that is primarily composed of copper and zinc, although other metals may be added in varying proportions to achieve specific characteristics.
The main reason brass is used in the construction of these instruments is its unique combination of properties. Copper provides durability, malleability, and a rich tonal quality, while zinc enhances the alloy’s strength and corrosion resistance.
The specific type of brass alloy used in the manufacturing process can vary depending on the desired tone, response, and playability of the instrument. The most common type of brass used is yellow brass, which typically contains around 70% copper and 30% zinc. This alloy produces a bright and vibrant sound and is widely used in trumpets, trombones, and other brass instruments.
Another popular alloy used in brass instruments is red brass, also known as rose brass or gold brass. This alloy contains a higher proportion of copper, often around 85%, resulting in a warmer and mellower tone. Red brass is commonly found in French horns, euphoniums, and other instruments that require a softer and more lyrical sound.
While copper and zinc are the primary components of brass alloys used in instrument making, small amounts of other metals may also be added to further customize the properties of the alloy. For example, nickel or silver can be introduced to enhance the instrument’s projection, response, and resistance to tarnishing. Such alloys are often used in high-end trumpets or other brass instruments designed for professional musicians.
In addition to the main materials used in the construction of brass instruments, other components may be made from different materials. For instance, the valves and slides in brass instruments are typically made from brass or nickel silver for smooth and precise movement. The lead pipe, which connects the mouthpiece to the rest of the instrument, may also be made from specific alloys to help optimize the instrument’s response and resonance.
Overall, the choice of materials used in brass instruments is crucial in determining their sound, playability, and durability. The careful selection and combination of different alloys contribute to the unique characteristics and versatility of each instrument, allowing musicians to explore a wide range of tones and emotions in their performances.
Properties of Brass
Brass, the alloy used in the construction of brass instruments, possesses a unique set of properties that make it an ideal material for these musical instruments. The combination of copper and zinc in brass gives it a distinctive balance of strength, durability, resonance, and malleability.
One of the key properties of brass is its excellent acoustic properties. It offers a rich and vibrant tone, allowing brass instruments to produce a wide range of dynamic and expressive sounds. The composition of the brass alloy, including the specific proportions of copper and zinc, influences the tonal qualities of the instrument. For example, alloys with a higher copper content tend to produce a warmer and mellower sound, while alloys with a higher zinc content yield a brighter and more assertive tone.
Brass is also known for its durability, especially in the context of musical instruments that require frequent handling and playing. The alloy’s resistance to corrosion makes it less prone to tarnishing and oxidation, ensuring that brass instruments maintain their appearance and sound quality over time. This durability allows for years of use and enjoyment without compromising the instrument’s performance or structural integrity.
Another valuable property of brass is its malleability, which refers to its ability to be easily shaped and formed into complex structures. This malleability allows instrument makers to create the intricate tubing, curves, and components that are essential for the unique design of each brass instrument. The malleability of brass also contributes to the playability of the instrument, enabling musicians to manipulate the sound through various playing techniques, such as bending notes or executing intricate passages.
Furthermore, brass possesses good conductivity, which allows for efficient transmission of sound vibrations throughout the instrument. This property contributes to the instruments’ ability to resonate and amplify the sound, resulting in a powerful and engaging performance.
Additionally, brass instruments benefit from the thermal conductivity of brass, which enables them to respond quickly to changes in temperature. This property is particularly important for brass instruments as fluctuations in temperature can affect pitch and intonation. The conductivity of brass ensures that heat is distributed evenly throughout the instrument, helping to maintain a consistent performance even during extended playing sessions.
Overall, the properties of brass, including its acoustic capabilities, durability, malleability, conductivity, and thermal properties, play a vital role in the construction and performance of brass instruments. These properties contribute to the characteristic sound, longevity, and versatility that have made brass instruments a staple in various musical genres throughout history.
Different Types of Brass Alloys Used
While brass, the alloy of copper and zinc, is the primary material used in the construction of brass instruments, there are different types of brass alloys that offer distinct tonal characteristics and performance qualities. The specific composition of these alloys, along with any additional metals added to the mix, can greatly influence the sound, response, and overall playing experience of the instrument.
Yellow Brass: Yellow brass is the most common type of brass alloy used in brass instruments. It typically consists of approximately 70% copper and 30% zinc. This alloy offers a bright and vibrant sound, making it well-suited for instruments like trumpets, trombones, and tubas. Yellow brass instruments are known for their excellent projection and versatility across various musical genres.
Red Brass: Red brass, also known as rose brass or gold brass, contains a higher proportion of copper, often around 85%, and a lower amount of zinc. This composition results in a warmer, mellower, and more lyrical tone. Red brass is commonly used in instruments such as French horns, euphoniums, and some tubas, where a softer and more expressive sound quality is desired.
Nickel Silver: Brass instruments may also incorporate nickel silver, also known as German silver, in certain components. Nickel silver is an alloy consisting of copper, zinc, and nickel. It offers enhanced durability and resistance to corrosion, making it ideal for valves, slides, and other moving parts. In addition, nickel silver can impart a brighter and more focused tone to the instrument.
Silver Plated Brass: Some brass instruments feature a layer of silver plating on the brass alloy. This silver plating not only enhances the visual appeal of the instrument but also adds a touch of brilliance and clarity to the sound. Silver-plated brass instruments typically exhibit increased projection and improved response, making them popular among professional musicians seeking a refined and precise tone.
Leadpipe Alloys: The leadpipe, the part of the instrument that connects the mouthpiece to the rest of the instrument, can be made from various alloys. Different leadpipe alloys can affect the instrument’s response and resonance. For example, yellow brass leadpipes are commonly used for their versatile and vibrant sound, while rose brass or gold brass leadpipes offer a warmer and more focused tone.
Additional custom alloys may be used by instrument makers to achieve specific sound qualities or aesthetic preferences. These alloys can include small amounts of metals like silver, tin, or phosphorus, which can alter the instrument’s characteristics. Each brass instrument, regardless of the alloy used, offers its own unique tonal signature, allowing musicians to choose the instrument that best suits their personal playing style and musical preferences.
The selection of the appropriate brass alloy is a careful balancing act, as it must consider factors such as tonal quality, response, durability, and manufacturing feasibility. The choice of alloy contributes to the individuality and versatility that define brass instruments, ensuring that musicians can find the perfect instrument to fulfill their artistic vision and musical expression.
Manufacturing Process of Brass Instruments
The manufacturing process of brass instruments involves a combination of traditional craftsmanship and modern manufacturing techniques. From the initial design to the final assembly, each step plays a crucial role in creating an instrument that produces exceptional sound quality and exhibits outstanding craftsmanship.
The process begins with the design and prototyping stage. Instrument makers work closely with skilled designers and engineers to develop precise blueprints and specifications for the instrument. This includes determining the optimal dimensions and proportions of the tubing, placement of valves or slides, and the overall form of the instrument.
Once the design is finalized, the manufacturing process moves on to the fabrication of the instrument’s components. The main body of the instrument, including the tubing and bell, is typically formed from brass sheets or tubes. In some cases, computerized machinery may be used to shape the components based on the design specifications, ensuring accuracy and consistency.
For certain parts of the instrument, such as the valves or slides, specialized manufacturing techniques are employed. Valves are meticulously crafted using a combination of machining and hand-finishing methods to ensure precise movement and optimal airtightness. Slides, which allow for adjustments in pitch and tuning, are carefully fitted and aligned to ensure smooth operation.
Once the individual components are fabricated, they undergo various surface treatments. This can include polishing, buffing, or applying finishes such as lacquer, silver plating, or gold plating. These treatments not only enhance the visual appeal of the instrument but also protect the brass from tarnishing and provide a smooth surface for optimal playability.
After the components have been treated and prepared, the instrument is ready for assembly. Skilled craftsmen meticulously fit the valves, slides, and other parts together, ensuring proper alignment, airtight seals, and smooth operation. This step requires both precision and experience to achieve the desired sound quality and playability.
Once the instrument is fully assembled, it undergoes thorough quality control checks, including play-testing, to ensure optimal sound production and performance. Any necessary adjustments are made to fine-tune the instrument’s response, intonation, and overall playability.
The final step in the manufacturing process is the inspection and packaging of the instrument. Each instrument is carefully inspected for any imperfections or flaws before being meticulously packaged, ready to be shipped to musicians and music enthusiasts around the world.
Throughout the manufacturing process of brass instruments, a combination of traditional craftsmanship and modern technology is employed. Skilled artisans and instrument makers bring their expertise and attention to detail to ensure the highest quality instruments are produced, allowing musicians to showcase their talent and create beautiful music.
Care and Maintenance of Brass Instruments
Proper care and maintenance are essential for keeping brass instruments in optimal condition and ensuring their longevity. By following some simple guidelines, musicians can prolong the life of their instruments and maintain their sound quality. Here are some key practices to consider:
1. Cleaning: Regular cleaning is vital to prevent the build-up of dirt, oils, and debris on the instrument’s surface and inside the tubing. Use a soft cloth or a specialized instrument cleaning cloth to wipe down the instrument after each use. For more thorough cleaning, use lukewarm water and mild soap, carefully rinsing and drying the instrument afterward to prevent moisture damage.
2. Valve and Slide Maintenance: Valves and slides should be regularly inspected and lubricated to ensure smooth operation. Use a valve oil specifically designed for brass instruments to keep the valves moving freely. Slides can be lubricated with slide grease or cream to maintain their ease of movement.
3. Mouthpiece Care: The mouthpiece should be cleaned after each use to remove any residue or bacteria. Use a mouthpiece brush and warm soapy water to clean the mouthpiece gently. Avoid using harsh chemicals or abrasive materials as they can damage the mouthpiece.
4. Storage: When not in use, store the instrument in a proper case to protect it from dust, moisture, and impact. Ensure that the case is dry and has a soft interior lining to prevent scratches or damage to the instrument.
5. Avoid Excessive Heat and Humidity: Brass instruments should be kept away from extreme temperatures and high humidity levels, as these conditions can have adverse effects on the instrument’s structure, finish, and sound quality. Avoid leaving the instrument in direct sunlight or near heat sources.
6. Regular Maintenance by a Professional: Schedule regular check-ups and maintenance appointments with a qualified instrument technician. They can professionally clean and inspect the instrument, address any mechanical issues, and make adjustments for optimal performance.
7. Proper Playing Techniques: Develop good playing habits to minimize potential damage to the instrument. Avoid excessive force or bending of the tubing, and handle the instrument with care to prevent dents or scratches.
By incorporating these care and maintenance practices into your routine, you can safeguard the integrity and longevity of your brass instrument. Regular attention and a proactive approach to maintenance will ensure that your instrument continues to produce its characteristic sound and remains a joy to play for years to come.
Conclusion
Brass instruments are not only beautiful to behold, but they also possess a rich and captivating sound that has mesmerized audiences across centuries. The materials used in their construction, such as brass alloys, play a crucial role in shaping their distinctive tone, resonance, and durability.
From ancient civilizations to the modern era, brass instruments have undergone a remarkable evolution. The craftsmanship and innovation of both instrument makers and musicians have continued to push the boundaries of what these instruments can achieve. With advancements in design, manufacturing techniques, and materials, brass instruments have reached new heights of performance and versatility.
Understanding the properties and materials used in brass instruments provides valuable insight into their unique qualities and helps musicians make informed choices when selecting an instrument. Whether it’s the vibrant sound of a trumpet, the mellow tones of a French horn, or the smooth slides of a trombone, each brass instrument offers its own blend of artistry and musical expression.
Proper care and maintenance are crucial for preserving the longevity and performance of brass instruments. By following recommended cleaning, lubrication, and storage practices, musicians can ensure that their instruments remain in optimal condition and continue to delight audiences for many years to come.
Exploring the world of brass instruments, their materials, and their manufacturing processes allows us to appreciate the craftsmanship, innovation, and dedication that goes into creating these magnificent musical instruments. Whether you are a musician, a collector, or simply an enthusiast, let your journey with brass instruments be filled with beauty, harmony, and the joy of making music.