Home>Production & Technology>Acoustic>How Are Acoustic Guitars Made
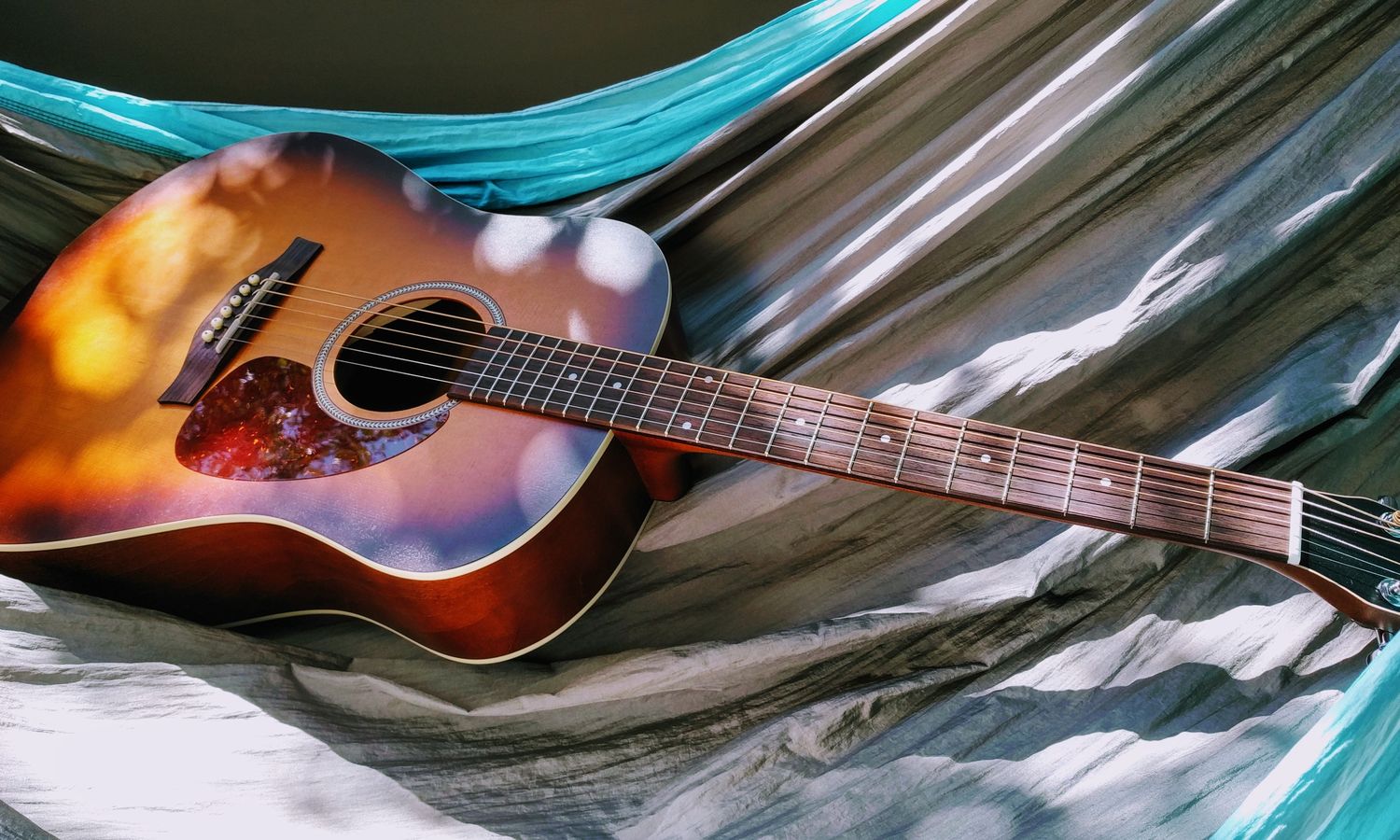
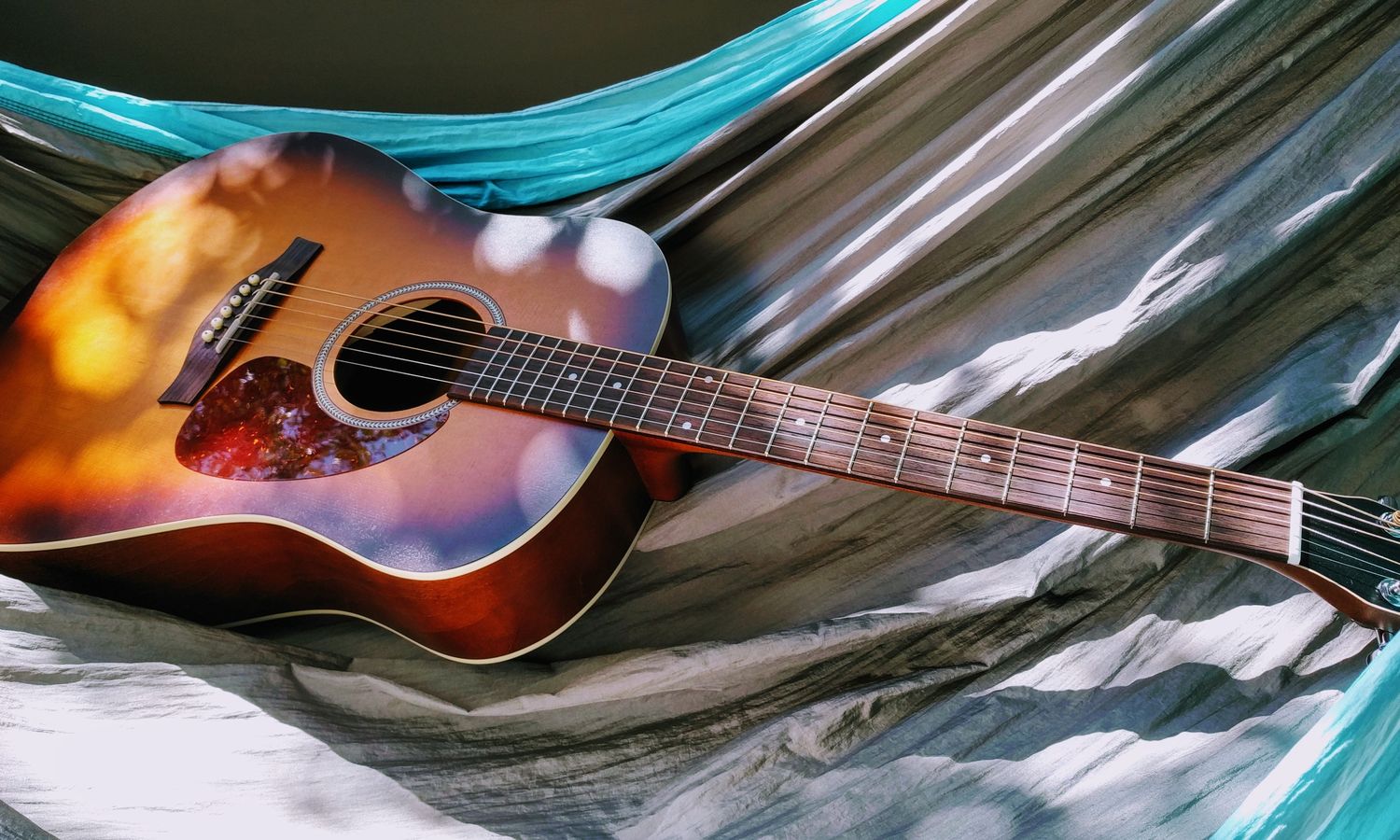
Acoustic
How Are Acoustic Guitars Made
Published: March 12, 2024
Discover the intricate process of crafting acoustic guitars, from selecting the finest materials to the skilled artistry of construction. Explore the craftsmanship and dedication behind creating these timeless instruments.
(Many of the links in this article redirect to a specific reviewed product. Your purchase of these products through affiliate links helps to generate commission for AudioLover.com, at no extra cost. Learn more)
Table of Contents
Introduction
Acoustic guitars are not just musical instruments; they are works of art that resonate with the soul of both the musician and the listener. The process of crafting an acoustic guitar is a harmonious blend of traditional craftsmanship and modern precision. From the careful selection of wood to the intricate assembly of each component, every step in the creation of an acoustic guitar contributes to its unique tone and character.
Crafting an acoustic guitar is a labor of love that requires skill, patience, and a deep understanding of acoustics. Each guitar is a testament to the dedication and artistry of the luthiers who meticulously shape, assemble, and fine-tune every detail to create an instrument that not only sounds beautiful but also feels like an extension of the musician's soul.
In this article, we will take a journey through the meticulous process of crafting an acoustic guitar, exploring the selection of wood, the shaping and assembly of the guitar body, the installation of the neck and fretboard, the attachment of the bridge and tuning pegs, the finishing touches, and the rigorous quality control and testing that ensure each guitar meets the highest standards of excellence.
Join us as we delve into the captivating world of acoustic guitar craftsmanship, where tradition and innovation converge to create instruments that inspire and enchant musicians and enthusiasts alike.
Selection of Wood
The selection of wood is a crucial stage in the crafting of acoustic guitars, as it significantly influences the instrument's tone, resonance, and overall aesthetic appeal. Luthiers, the skilled artisans who craft guitars, meticulously choose the wood for its acoustic properties and visual characteristics. The top, or soundboard, of an acoustic guitar is typically made from spruce or cedar, chosen for their ability to resonate and project sound effectively. Spruce is favored for its strength and clarity, while cedar is known for its warmth and responsiveness.
The back and sides of the guitar are commonly crafted from mahogany, rosewood, or maple, each imparting distinct tonal qualities to the instrument. Mahogany is prized for its balanced and warm sound, while rosewood offers rich overtones and a deep, resonant tone. Maple, with its bright and articulate sound, is often chosen for its striking visual appeal as well.
In addition to the tonal considerations, luthiers pay close attention to the grain patterns and visual characteristics of the wood. The figuring and color of the wood contribute to the guitar's aesthetic beauty, making each instrument a unique work of art. The careful selection of wood ensures that the acoustic guitar not only sounds exceptional but also possesses a captivating visual allure.
Furthermore, the neck of the guitar is typically crafted from sturdy yet resonant woods such as mahogany or maple, providing stability and contributing to the overall tonal characteristics of the instrument. The fretboard, often made from ebony or rosewood, is chosen for its durability and smooth playing surface.
Overall, the selection of wood is a meticulous process that requires a keen understanding of the acoustic properties and visual appeal of different wood species. By carefully choosing the right combination of woods, luthiers lay the foundation for crafting acoustic guitars that resonate with exceptional tonal clarity and possess an aesthetic charm that captivates both the eyes and ears of musicians and enthusiasts.
Cutting and Shaping the Wood
Once the wood has been carefully selected, the process of cutting and shaping the various components of the guitar begins. This stage requires precision, expertise, and a deep understanding of the acoustic properties of different wood species. The top, back, and sides of the guitar are meticulously shaped to exact dimensions, ensuring that each piece contributes to the instrument's structural integrity and tonal characteristics.
Luthiers use a combination of traditional hand tools and modern machinery to carve and shape the wood with meticulous attention to detail. The soundboard, or top, is delicately thinned to achieve the optimal balance of strength and resonance. The bracing, which supports the soundboard and influences its flexibility, is carefully shaped and positioned to enhance the guitar's tonal projection and responsiveness.
The back and sides of the guitar undergo a similar process of shaping and contouring to achieve the desired curves and dimensions. Each component is meticulously crafted to ensure a precise fit and seamless assembly, laying the foundation for a guitar body that resonates with exceptional clarity and balance.
The neck of the guitar is shaped with precision to achieve the ideal profile for comfortable playability and optimal transfer of string vibrations. The fretboard is carefully slotted and shaped, ensuring that each fret is precisely positioned for accurate intonation and effortless playability across the entire length of the neck.
Throughout the cutting and shaping process, luthiers pay close attention to the grain orientation and structural integrity of the wood, ensuring that each component is crafted to enhance the instrument's acoustic properties and visual appeal. The meticulous craftsmanship involved in cutting and shaping the wood is a testament to the dedication and skill of the luthiers, who imbue each guitar with a unique blend of artistry and functionality.
In essence, the cutting and shaping of the wood is a pivotal stage in the creation of an acoustic guitar, where raw materials are transformed into meticulously crafted components that lay the foundation for an instrument of exceptional tonal clarity, resonance, and visual beauty.
Assembly of the Guitar Body
The assembly of the guitar body marks a pivotal stage in the meticulous process of crafting an acoustic guitar. It is at this stage that the carefully shaped components, including the top, back, and sides of the guitar, come together to form the resonant core of the instrument. The assembly process requires precision, expertise, and a deep understanding of how each component contributes to the guitar's tonal characteristics and structural integrity.
Luthiers begin by delicately joining the top and back to the sides of the guitar, using traditional methods such as hand-fitted dovetail joints or modern techniques such as advanced adhesive bonding. The precise alignment and seamless joining of these components are essential to ensure the structural stability and tonal resonance of the guitar body.
The bracing, which supports the soundboard and influences its flexibility, is meticulously positioned and glued into place. The placement and shaping of the bracing are critical factors in shaping the guitar's tonal characteristics, influencing its projection, sustain, and responsiveness.
The assembly process also involves the installation of linings along the interior edges of the guitar body, providing reinforcement and enhancing the structural integrity of the instrument. These linings contribute to the overall stability of the guitar body, ensuring that it can withstand the tension of the strings and the rigors of performance.
Furthermore, the soundhole rosette, a decorative and functional element encircling the soundhole, is carefully installed, adding a touch of visual elegance to the guitar body while allowing for the transmission of sound waves from the interior of the instrument.
As the components come together, the luthier meticulously inspects and fine-tunes the alignment, fit, and overall integrity of the guitar body. This attention to detail ensures that the assembled body not only resonates with exceptional tonal clarity but also possesses a seamless and visually captivating appearance.
In essence, the assembly of the guitar body is a harmonious convergence of craftsmanship and precision, where carefully shaped components unite to form an instrument that embodies the artistry and dedication of the luthier. It sets the stage for the next steps in the creation of an acoustic guitar, leading to the installation of the neck and fretboard, the attachment of the bridge and tuning pegs, and the meticulous finishing touches that elevate the instrument to a true work of art.
Installation of the Neck and Fretboard
The installation of the neck and fretboard is a critical stage in the meticulous process of crafting an acoustic guitar. This phase requires precision, expertise, and a deep understanding of how the neck and fretboard contribute to the playability, tonal characteristics, and overall structural integrity of the instrument.
Luthiers begin by carefully fitting the neck to the body of the guitar, ensuring a seamless and stable connection. Traditional methods such as the dovetail joint or modern techniques involving advanced adhesives are employed to secure the neck in place. The precise alignment and angle of the neck are crucial factors that influence the playability and tonal response of the guitar.
Once the neck is securely attached, the fretboard is meticulously installed. The fretboard, often made from durable and resonant woods such as ebony or rosewood, is carefully positioned and glued to the neck. The luthier pays close attention to the alignment and spacing of the frets, ensuring that each fret is precisely positioned for accurate intonation and effortless playability across the entire length of the neck.
The installation of the neck and fretboard also involves the delicate task of shaping and filing the frets to achieve a smooth and consistent playing surface. This process requires meticulous attention to detail to ensure that the frets are precisely leveled and polished, allowing for comfortable and precise fretting of the strings.
Furthermore, the nut and saddle, which are essential components for transmitting the vibrations of the strings to the body of the guitar, are carefully installed and precisely positioned. The nut, located at the top of the neck, supports the strings and determines their spacing, while the saddle, located on the bridge, provides a point of contact for the strings and influences their action and intonation.
As the neck and fretboard are installed, the luthier meticulously inspects and fine-tunes the alignment, fit, and overall playability of the instrument. This attention to detail ensures that the neck and fretboard not only contribute to the guitar's tonal clarity and resonance but also provide a comfortable and responsive playing experience for the musician.
In essence, the installation of the neck and fretboard is a testament to the craftsmanship and precision of the luthier, where the careful integration of these components sets the stage for the attachment of the bridge and tuning pegs, the meticulous finishing touches, and the rigorous quality control and testing that ensure each guitar meets the highest standards of excellence.
Attaching the Bridge and Tuning Pegs
The process of attaching the bridge and tuning pegs is a pivotal stage in the meticulous construction of an acoustic guitar. This phase requires precision, expertise, and a deep understanding of how these components contribute to the instrument's playability, tuning stability, and overall tonal characteristics.
The bridge, a critical component that anchors the strings to the body of the guitar, is meticulously positioned and secured. Luthiers carefully mark the precise location for the bridge, taking into account factors such as scale length, intonation, and string action. Once the placement is determined, the bridge is delicately glued to the soundboard, ensuring a secure and resonant connection. The saddle, a small piece located on the bridge, plays a crucial role in transmitting the vibrations of the strings to the soundboard, influencing the guitar's tone and projection. The precise shaping and positioning of the saddle are essential to achieving optimal string action and intonation.
In addition to the bridge, the installation of the tuning pegs, also known as machine heads or tuners, is a meticulous process that directly impacts the guitar's tuning stability and playability. Luthiers carefully drill and install the tuning pegs, ensuring that they are aligned for smooth and precise tuning adjustments. The gearing mechanism within the tuning pegs allows for fine-tuning of the string tension, enabling musicians to achieve accurate pitch and maintain stable tuning during performance.
Furthermore, the nut, a small component located at the top of the neck, plays a crucial role in supporting the strings and determining their spacing. Luthiers meticulously shape and install the nut, ensuring that it provides optimal support for the strings and facilitates smooth string movement across the fretboard. The careful shaping and positioning of the nut contribute to the guitar's playability and intonation, allowing for comfortable fretting and accurate string spacing.
As the bridge and tuning pegs are meticulously installed, the luthier pays close attention to the alignment, fit, and overall functionality of these components. This meticulous approach ensures that the bridge and tuning pegs not only contribute to the guitar's tonal clarity and resonance but also provide a stable and responsive platform for tuning and playing.
In essence, the attachment of the bridge and tuning pegs is a testament to the craftsmanship and precision of the luthier, where the careful integration of these components sets the stage for the finishing touches and the rigorous quality control and testing that ensure each guitar meets the highest standards of excellence.
Finishing Touches
The finishing touches of an acoustic guitar represent the culmination of meticulous craftsmanship and attention to detail, elevating the instrument to a true work of art. This phase requires precision, expertise, and a deep understanding of how the final treatments and adjustments contribute to the guitar's visual appeal, tonal characteristics, and overall playability.
One of the key elements of the finishing process is the application of the guitar's finish, which serves to protect the wood, enhance its visual allure, and influence the instrument's tonal properties. Luthiers carefully apply the finish, whether it be a traditional hand-rubbed varnish or a modern lacquer, with meticulous attention to achieving a smooth and lustrous surface. The finish not only accentuates the natural beauty of the wood but also plays a role in shaping the guitar's resonance and tonal clarity.
In addition to the finish, the installation of the frets and the final shaping and polishing of the fretboard are essential aspects of the finishing touches. Luthiers meticulously press and secure the frets into the fretboard, ensuring precise alignment and consistent height for accurate intonation and effortless playability. The fret ends are delicately dressed and polished to provide a smooth and comfortable playing surface, allowing the musician to navigate the fretboard with ease and precision.
Furthermore, the installation of the nut and saddle, as well as the meticulous adjustment of the string action and intonation, are critical components of the finishing process. Luthiers carefully shape and position the nut and saddle to optimize string spacing and transmission of string vibrations, ensuring that the guitar delivers exceptional playability and tonal balance. The fine adjustments to the string action and intonation contribute to the instrument's responsiveness and tuning stability, allowing for a comfortable playing experience across the entire fretboard.
The final detailing, including the installation of decorative elements such as binding, purfling, and inlays, adds a touch of visual elegance to the guitar, further enhancing its aesthetic appeal. These ornamental details not only showcase the luthier's artistry but also contribute to the instrument's visual allure, making each guitar a unique and captivating work of art.
In essence, the finishing touches of an acoustic guitar represent the culmination of the luthier's dedication and skill, where every detail is meticulously attended to in order to create an instrument that not only sounds exceptional but also captivates the eyes and hands of musicians and enthusiasts.
Quality Control and Testing
Quality control and testing are integral aspects of the meticulous process of crafting an acoustic guitar. This phase represents the luthier's unwavering commitment to ensuring that each instrument meets the highest standards of excellence in terms of playability, tonal clarity, and overall craftsmanship.
The quality control process begins with a comprehensive inspection of every component of the guitar, from the carefully shaped body to the intricately installed neck, fretboard, and hardware. Luthiers meticulously examine the joinery, seams, and overall structural integrity of the instrument, ensuring that each component is precisely aligned and securely fastened. This meticulous scrutiny is essential to guaranteeing the guitar's resilience and stability, especially when subjected to the tension of the strings and the demands of performance.
Furthermore, the tonal characteristics of the guitar are rigorously evaluated through meticulous testing. Luthiers meticulously tap and listen to the soundboard, assessing its responsiveness and resonance. This hands-on approach allows them to discern the subtle nuances of the instrument's tonal properties, ensuring that it delivers a balanced and articulate sound across the entire frequency spectrum. Additionally, the intonation and playability of the guitar are meticulously assessed, with luthiers meticulously adjusting the string action, nut, and saddle to achieve optimal playability and accurate intonation.
In addition to the physical inspection and tonal assessment, the aesthetic details of the guitar undergo meticulous scrutiny. Luthiers meticulously examine the finish, fretwork, and decorative elements, ensuring that each detail contributes to the instrument's visual allure and overall craftsmanship. This attention to detail is essential to creating an instrument that not only sounds exceptional but also captivates the eyes and hands of musicians and enthusiasts.
Once the quality control process is complete, each guitar undergoes rigorous testing to ensure its playability, tonal balance, and overall performance. Skilled musicians meticulously play and evaluate the instrument, providing valuable feedback on its responsiveness, tonal characteristics, and overall playability. This hands-on testing allows luthiers to fine-tune and adjust the instrument, ensuring that it meets the exacting standards of playability and tonal excellence.
In essence, the quality control and testing phase represents the luthier's unwavering dedication to creating instruments of exceptional quality and craftsmanship. Through meticulous inspection, tonal assessment, and rigorous testing, luthiers ensure that each acoustic guitar embodies the artistry, precision, and dedication that define the timeless craft of guitar making.
Conclusion
In conclusion, the meticulous process of crafting an acoustic guitar is a harmonious blend of traditional craftsmanship, modern precision, and a deep understanding of acoustics. From the careful selection of wood to the intricate assembly of each component, every step in the creation of an acoustic guitar contributes to its unique tone, resonance, and visual appeal.
The selection of wood sets the foundation for the instrument's tonal characteristics and aesthetic allure. Luthiers carefully choose woods such as spruce, cedar, mahogany, rosewood, and maple, considering their acoustic properties and visual appeal. The grain patterns and color of the wood contribute to the guitar's aesthetic beauty, making each instrument a unique work of art.
The cutting and shaping of the wood require precision and expertise, as luthiers meticulously carve and contour the components to achieve the optimal balance of strength, resonance, and visual elegance. The assembly of the guitar body brings together the carefully shaped components, ensuring structural stability and tonal resonance.
The installation of the neck and fretboard, along with the attachment of the bridge and tuning pegs, sets the stage for a comfortable playing experience and stable tuning. The finishing touches, including the application of the finish, installation of frets, and final adjustments, elevate the instrument to a true work of art, both visually and tonally.
The rigorous quality control and testing process ensure that each guitar meets the highest standards of excellence in terms of playability, tonal clarity, and overall craftsmanship. Skilled musicians provide valuable feedback, allowing luthiers to fine-tune and adjust the instrument to achieve optimal performance.
In essence, the craftsmanship and dedication of luthiers shine through every stage of the guitar-making process, resulting in instruments that not only sound exceptional but also captivate the eyes and hands of musicians and enthusiasts. Each acoustic guitar is a testament to the timeless artistry and unwavering commitment to excellence that define the world of guitar making.