Home>Instruments>Guitar>How To Make A Guitar Pedal
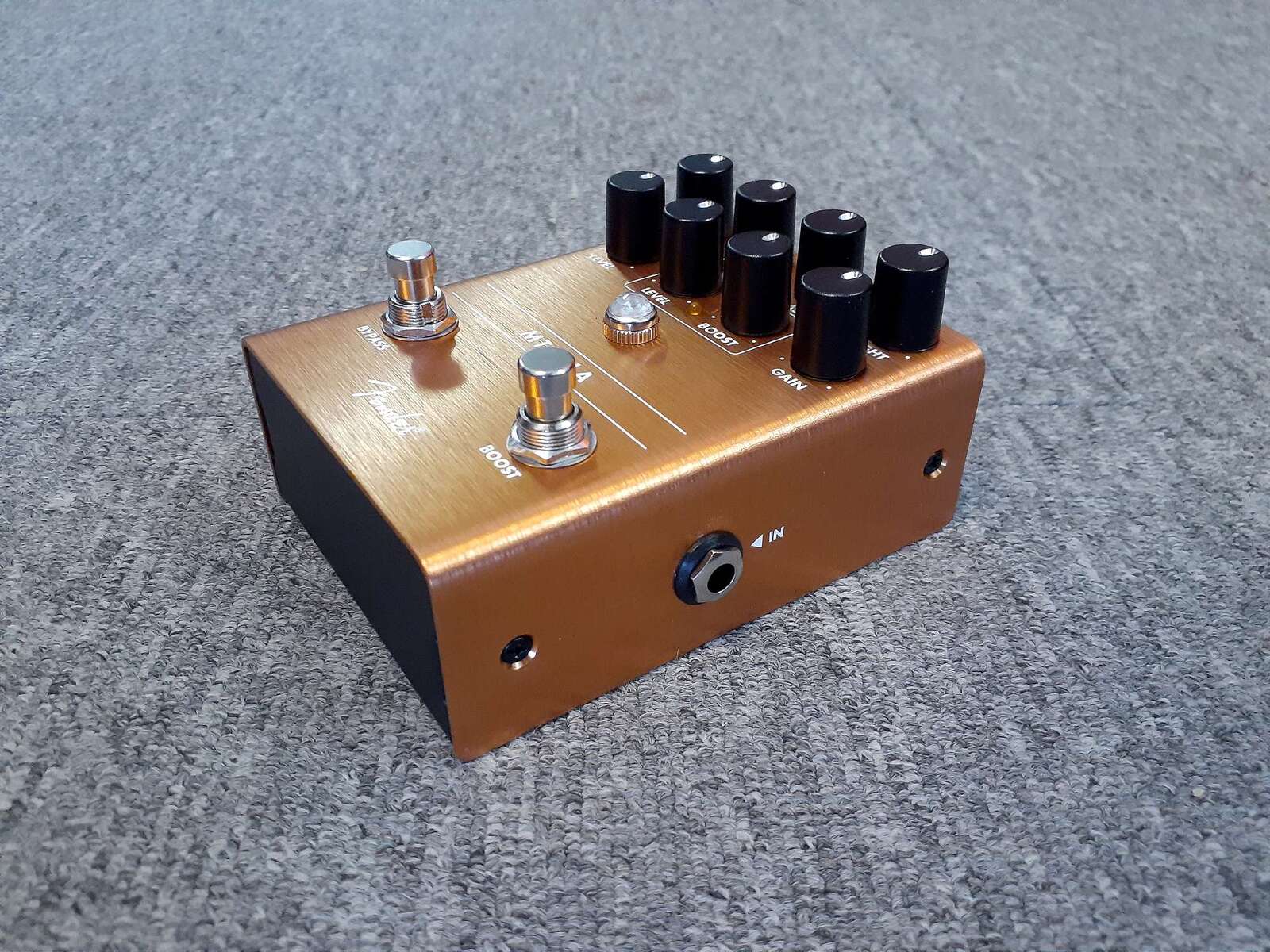
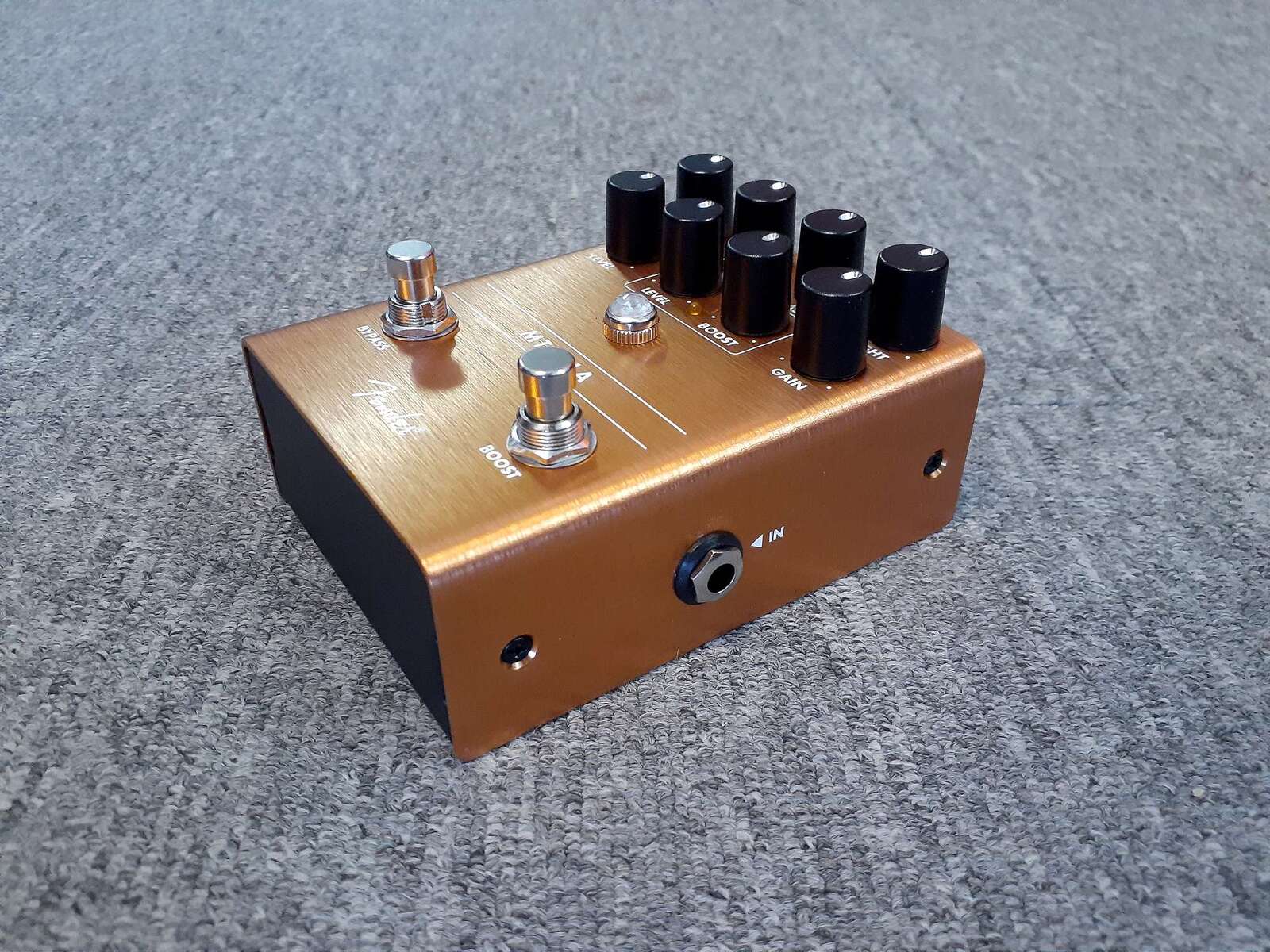
Guitar
How To Make A Guitar Pedal
Published: February 13, 2024
Learn how to make your own guitar pedal with step-by-step instructions and expert tips. Create custom effects for your guitar!
(Many of the links in this article redirect to a specific reviewed product. Your purchase of these products through affiliate links helps to generate commission for AudioLover.com, at no extra cost. Learn more)
Table of Contents
How to Make a Guitar Pedal
Introduction
So, you've been playing the guitar for a while now, and you're looking to expand your sonic horizons. One way to do that is by incorporating guitar pedals into your setup. These small devices can dramatically alter your guitar's sound, adding effects like distortion, delay, reverb, and more. While there are countless guitar pedals available for purchase, there's something uniquely satisfying about building your own.
Building a guitar pedal from scratch may seem like a daunting task, especially if you're new to electronics. However, with the right guidance and a bit of patience, it's a rewarding and educational experience. Not only will you gain a deeper understanding of how these magical little boxes work, but you'll also have the freedom to customize the pedal to your exact specifications.
In this comprehensive guide, we'll walk you through the process of building your own guitar pedal. From selecting the right materials and tools to soldering components and troubleshooting, we'll cover each step in detail. Whether you're a seasoned DIY enthusiast or a curious guitarist looking to expand your skill set, this guide will equip you with the knowledge and confidence to embark on this exciting journey.
Before we dive into the nitty-gritty of circuit design and soldering, it's important to note that building a guitar pedal requires a basic understanding of electronics and soldering techniques. If you're new to these concepts, don't worry ā we'll break down each step in a beginner-friendly manner, ensuring that you can follow along regardless of your prior experience.
By the end of this guide, you'll not only have a fully functional custom guitar pedal but also a newfound sense of accomplishment and a deeper connection to your music. So, grab your soldering iron, unleash your creativity, and let's embark on this electrifying DIY adventure together.
Materials and Tools
Before diving into the construction of your custom guitar pedal, it’s essential to gather all the necessary materials and tools. Having the right components and equipment at your disposal will streamline the building process and ensure a successful outcome. Here’s a comprehensive list of the materials and tools you’ll need:
Materials:
- Printed circuit board (PCB): This serves as the foundation for your pedal's electronic components.
- Electronic components: Resistors, capacitors, diodes, transistors, and other parts specific to your pedal's circuit design.
- Enclosure: The housing for your pedal, typically made of metal or durable plastic.
- Footswitch and potentiometers: These components control the pedal's operation and parameters.
- Wire: Insulated copper wire for connecting components on the PCB.
- Input and output jacks: These allow you to connect your guitar and amplifier to the pedal.
- Power supply: Depending on your pedal's requirements, this could be a 9V battery snap or a DC power jack.
- Graphics (optional): If you want to personalize the pedal's appearance, consider decals, paint, or custom artwork.
Tools:
- Soldering iron and solder: Essential for connecting components to the PCB.
- Wire cutters and strippers: For preparing and trimming wire connections.
- Multimeter: Used to measure electrical values and troubleshoot any potential issues.
- Drill and bits: If modifications to the enclosure are necessary for mounting components.
- Screwdriver set: For assembling the enclosure and securing components.
- Helping hands: These tools can hold the PCB and wires in place, freeing up your hands for soldering.
- Safety equipment: Safety glasses and a well-ventilated workspace are crucial for soldering and drilling.
By ensuring you have all the required materials and tools on hand, you’ll be well-prepared to embark on the construction of your custom guitar pedal. With these essentials at your disposal, you can proceed to the next phase: circuit design.
Circuit Design
Now that you’ve assembled all the necessary materials and tools, it’s time to delve into the heart of your custom guitar pedal: the circuit design. The circuit determines the pedal’s functionality and sonic characteristics, shaping the way it processes your guitar’s signal. While there are countless circuit configurations to explore, we’ll focus on a classic example: the overdrive pedal.
Understanding the Overdrive Circuit:
The overdrive pedal is a staple in many guitarists’ arsenals, delivering warm, saturated tones and dynamic responsiveness. The core of the overdrive circuit is the op-amp, a versatile component that shapes the pedal’s distortion characteristics. By adjusting the values of resistors, capacitors, and diodes within the circuit, you can fine-tune the overdrive’s gain, tone, and clipping behavior.
Choosing a Circuit Schematic:
For this guide, we’ll use a widely recognized overdrive circuit schematic as a starting point. The schematic provides a visual representation of the circuit’s components and their connections, serving as a roadmap for the pedal’s construction. While you can certainly design your own circuit from scratch, beginning with a proven schematic is an excellent way to gain hands-on experience and understand the principles behind pedal construction.
Customization and Experimentation:
Once you’ve familiarized yourself with the chosen circuit schematic, don’t hesitate to experiment with component values and configurations. Small adjustments can yield significant changes in the pedal’s sound, allowing you to tailor it to your preferences. Whether you’re aiming for a bluesy overdrive, a searing distortion, or a transparent boost, the circuit design stage is where you can inject your creativity and tonal aspirations into the pedal’s DNA.
Verifying the Circuit:
Before proceeding to the soldering stage, it’s crucial to verify the circuit’s functionality. Double-check the connections on the schematic against the physical layout of your components on the PCB. This step helps identify any potential errors or discrepancies, ensuring that the circuit is primed for successful implementation.
With a solid understanding of the overdrive circuit and a clear roadmap in the form of a schematic, you’re poised to bring your custom guitar pedal to life. The next phase, soldering components onto the PCB, will transform the circuit design from theory into tangible reality.
Soldering Components
With the circuit design finalized and the components at the ready, the next pivotal step in building your custom guitar pedal is soldering. Soldering is the process of permanently joining the electronic components to the printed circuit board (PCB), creating the interconnected network that forms the pedal’s circuit. While soldering may seem intimidating to beginners, with the right techniques and a steady hand, it becomes an accessible and rewarding skill to master.
Preparing the Workspace:
Prior to soldering, it’s essential to set up a clean and organized workspace. Ensure adequate lighting, a stable work surface, and ample ventilation to facilitate the soldering process. Additionally, arranging your components and tools within easy reach minimizes interruptions and streamlines the assembly workflow.
Understanding Soldering Techniques:
Two primary soldering techniques are commonly employed in pedal construction: through-hole soldering and surface-mount soldering. Through-hole soldering involves feeding the component leads through pre-drilled holes in the PCB, while surface-mount soldering applies solder to component pads on the PCB’s surface. For this guide, we’ll focus on through-hole soldering, which is prevalent in DIY pedal kits and offers excellent visibility and accessibility for beginners.
Applying Solder:
When soldering components, the goal is to create reliable electrical connections without creating short circuits or cold joints. To achieve this, heat the component lead and the copper pad on the PCB with a soldering iron, then apply a small amount of solder to form a smooth, shiny joint. It’s crucial to avoid excessive heat and solder, as this can damage the components or create unintended connections. Practice and patience are key to mastering the art of soldering, so don’t be discouraged by early attempts.
Inspecting and Testing:
After soldering each component, inspect the joints to ensure they are uniform and free of defects. A magnifying glass can be helpful for close examination, especially with smaller components and densely populated areas of the PCB. Once all components are soldered in place, use a multimeter to check for any unintended connections or open circuits. Thorough testing at this stage can prevent potential issues down the line.
By mastering the art of soldering, you’ll transform the inert components into a functional and interconnected circuit, bringing your custom guitar pedal one step closer to completion. The next phase, assembling the pedal within its enclosure, will merge the electronic core with its protective shell, culminating in a tangible and playable musical tool.
Assembling the Pedal
With the electronic components soldered onto the printed circuit board (PCB), it’s time to transition to the assembly phase, where the pedal takes shape within its protective enclosure. This pivotal stage combines precision and creativity, merging the functional core of the pedal with its external form. As you embark on this phase, attention to detail and a methodical approach will ensure a professional and polished outcome.
Preparing the Enclosure:
Before mounting the components, prepare the enclosure by drilling holes for the footswitch, potentiometers, input/output jacks, and any additional controls or indicators specific to your pedal’s design. Carefully measure and mark the hole placements to ensure proper alignment and fit for the components. A step drill bit is often used for this purpose, allowing for clean and precise holes without the need for multiple bit changes.
Mounting the Components:
Once the enclosure is prepped, proceed to mount the components onto the chassis. Secure the footswitch, potentiometers, and jacks in their respective positions, ensuring a snug and stable fit. It’s crucial to align the components accurately, as their placement directly impacts the pedal’s functionality and user experience. Additionally, consider using lock washers and nuts to secure the components firmly in place, preventing unintended movement during use.
Wiring the Connections:
With the components mounted, it’s time to establish the electrical connections between the PCB and the external controls. Utilize insulated wire to link the footswitch, potentiometers, and jacks to the corresponding points on the PCB, following the wiring diagram associated with your pedal’s circuit. Attention to detail during this phase ensures reliable signal flow and seamless operation of the pedal once assembled.
Securing the PCB:
Once the connections are established, carefully position the PCB within the enclosure, ensuring that it fits securely without contacting any metal components that could cause electrical interference. Consider using standoffs or spacers to elevate the PCB, preventing unintended contact with the enclosure and allowing for adequate airflow around the components.
As the pedal takes shape within its enclosure, the culmination of your efforts begins to emergeāa fully functional and personalized musical tool ready to unleash its sonic potential. The next phase, testing and troubleshooting, will ensure that your custom guitar pedal meets its performance expectations and is free from any technical issues before it hits the stage or studio.
Testing and Troubleshooting
As you near the completion of your custom guitar pedal, the crucial phase of testing and troubleshooting is paramount to ensure its functionality and performance. Thorough testing not only validates the successful assembly of the pedal but also allows for the identification and resolution of any potential issues that may compromise its operation. By methodically assessing the pedal’s functionality, you can fine-tune its performance and address any anomalies before it’s put into regular use.
Initial Functional Test:
Before sealing the enclosure, conduct an initial functional test to verify the pedal’s basic operation. Connect the pedal to a power source and an amplifier, then engage the footswitch to assess its effect on the guitar signal. Listen for any audible changes in tone, volume, or effect engagement, ensuring that the pedal responds as expected without introducing unwanted noise or distortion.
Signal Path and Controls:
Once the initial test is successful, systematically evaluate the pedal’s signal path and controls. Verify that the input and output jacks transmit the signal without impedance, and assess the functionality of the potentiometers and switches in controlling the pedal’s parameters. This comprehensive check ensures that the pedal’s core components and user interface are fully operational.
Electrical Measurements:
Utilize a multimeter to measure the pedal’s electrical characteristics, including voltage levels, resistance values, and continuity across critical points in the circuit. These measurements provide insights into the pedal’s internal workings and can reveal potential wiring errors or component issues that require attention.
Signal Integrity and Noise:
During testing, pay close attention to the pedal’s signal integrity and noise levels. Ensure that the pedal effectively processes the guitar signal without introducing unwanted hum, buzz, or interference. This assessment is crucial for delivering a clean and transparent signal path, free from electrical anomalies that detract from the pedal’s performance.
Troubleshooting and Iterative Refinement:
If any issues or irregularities are identified during testing, approach troubleshooting with a systematic mindset. Review the circuit diagram, inspect the solder joints, and recheck the component placements to pinpoint and address the root cause of any discrepancies. Iterative refinement based on testing feedback allows you to fine-tune the pedal’s performance and address any lingering issues effectively.
By conducting thorough testing and troubleshooting, you ensure that your custom guitar pedal meets its performance expectations and delivers the sonic characteristics you envisioned during the design phase. With any potential issues addressed, you can confidently move forward, knowing that your pedal is primed to enhance your musical creativity and expression.
Final Thoughts
Congratulations are in order as you’ve successfully navigated the exhilarating journey of building your own custom guitar pedal. From selecting the materials and designing the circuit to soldering components, assembling the pedal, and conducting rigorous testing, you’ve embarked on a transformative DIY endeavor that has expanded your skill set and deepened your connection to the world of guitar effects.
As you reflect on this rewarding experience, it’s important to recognize the valuable knowledge and insights gained throughout the process. Building a guitar pedal from scratch isn’t merely a technical feat; it’s a creative expression of your musical identity. The ability to shape your tone, sculpt your sound, and craft a personalized effect that resonates with your artistic vision is a testament to your ingenuity and dedication.
Moreover, the journey of building a guitar pedal transcends technical proficiency. It fosters a profound understanding of electronics, soldering techniques, and signal processing, enriching your comprehension of the inner workings of musical technology. This newfound expertise equips you with a deeper appreciation for the pedals adorning your rig and empowers you to explore further DIY projects with confidence and curiosity.
Beyond the technical and educational aspects, the act of building a guitar pedal embodies a spirit of craftsmanship and individuality. Your custom creation isn’t just a collection of components; it’s a tangible manifestation of your passion for music and a reflection of your sonic aspirations. Whether it’s a gritty overdrive, ethereal delay, or lush modulation, your pedal encapsulates your sonic identity and stands as a testament to your musical journey.
As you integrate your custom pedal into your rig, unleash its sonic capabilities, and share its unique voice with the world, remember the dedication and craftsmanship that went into its creation. Embrace the endless possibilities it offers, from inspiring new musical ideas to enhancing your live performances and studio recordings. Your custom pedal isn’t just a tool; it’s an extension of your artistic expression and a testament to the limitless creativity that thrives within you.
In closing, the journey of building a guitar pedal is a testament to your unwavering passion for music, your commitment to craftsmanship, and your relentless pursuit of sonic excellence. As you embark on future musical endeavors, may the knowledge and creativity cultivated through this experience continue to fuel your artistic pursuits and inspire others to embark on their own DIY odysseys. Your custom guitar pedal isn’t just a piece of gear; it’s a testament to the boundless creativity and innovation that define the musical landscape.